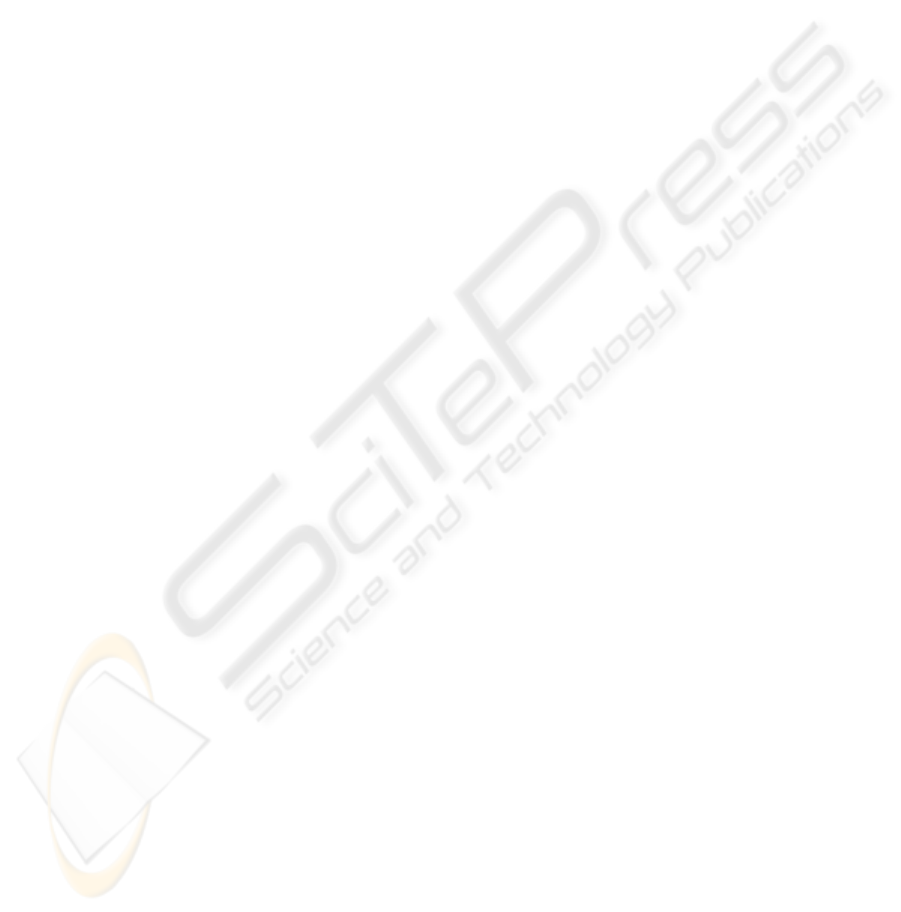
6 Conclusion
We used simulated driving maneuvers to test MLP networks for parameter estimation
in a vehicle supervision context. For this purpose, the vertical reaction force, the yaw
rate and the wheel slip have been estimated by neural network systems. The choice of
inputs for the MLPs was inspired from the physical model and the size of the hidden
layers was fixed after an exhaustive range scan up to 60 neurons. With regard to
robustness, and although only a limited number and somewhat particular cases were
studied, all results show that neural networks have an inherent degree of immunity
towards various types of errors. Thus this work concludes that a vehicle operating
system can make use of MLP estimation networks as inputs. This system can be
complementary to the multimedia and GPS services now being offered to passengers.
Its implementation should benefit from the speed of widely available neural network
integrated circuits, leaving any bottleneck to the upper software level.
Finally, the estimation results are best when the data under test is generated by the
same driver as the one used in the training phase. Therefore it is essential that the
networks be trained, under generic procedures, by the drivers that will use them.
References
1. Robert Bosch GmbH: ESP Electronic Stability Program, attributed to group effort (1999)
2. Sala, B.: Digital Device Development Group, Implementing Intelligence in Vehicles, The
Magazine of Engineers Australia, Vol. 76, N° 9, (2004) pp. 26-29
3. Guo, D. L., et al.: Neural Network Control for a Semi-Active Vehicle Suspension with a
Magnetorheological Damper, Journal of Vibration and Control, Vol. 10, No. 3, (2004) pp.
461-471
4. Gao, X. Z., et al: Acceleration signal estimation using neural networks, Measurement.
Science and Technology 12, (2001) pp. 1611-1619
5. He, Y., et al.: Engine Real-time Fault Diagnosis using Neural Networks, Automation
Technology for Off-Road Equipment, Proceedings of the July 26-27 Conference, Chicago,
Illinois, USA (2002), pp. 89-95
6. Weigl, K., Berthod, M.: Neural Networks as Dynamical Bases in Function Space, INRIA,
report N° 2124 (1993)
7. Hornik, K., et al.: Multilayer Feedforward Networks are Universal Function
Approximators, IEEE Transactions on Neural Networks, Vol 2, No. 5, (1989) pp. 359-366
8. Kiencke and Nielsen: Automotive Control Systems, SAE International, Springer (2002)
9. Canudas, C.: Dynamic Tire Friction Models for Vehicle Traction Control, Laboratoire
d’Automatique de Grenoble, Conference on Decision and Control, Phoenix, Arizona (1999)
10. Kim, Y. S., et al.: Development of RT vehicle simulation system for integration of ABS
HIL and a driving Simulator, Department of Automotive Engineering, Kookmin University,
Seoul, Korea.( 1998)
11. TESIS DYNAware veDyna Example Book - Standard Road (2002)
12. Rivals, I., et al.: Real-time control of an autonomous vehicle: A Neural Network Approach
to the Path Following Problem, 5th International Conference on Neural Networks and their
Applications, NeuroNîmes (1993)
13. Lin, Y., et al.: Artificial neural network modeling of driver handling behavior in a driver-
vehicle-environment system, International Journal of Vehicle Design - Vol. 37, No.1,
(2005) pp. 24 – 45
44