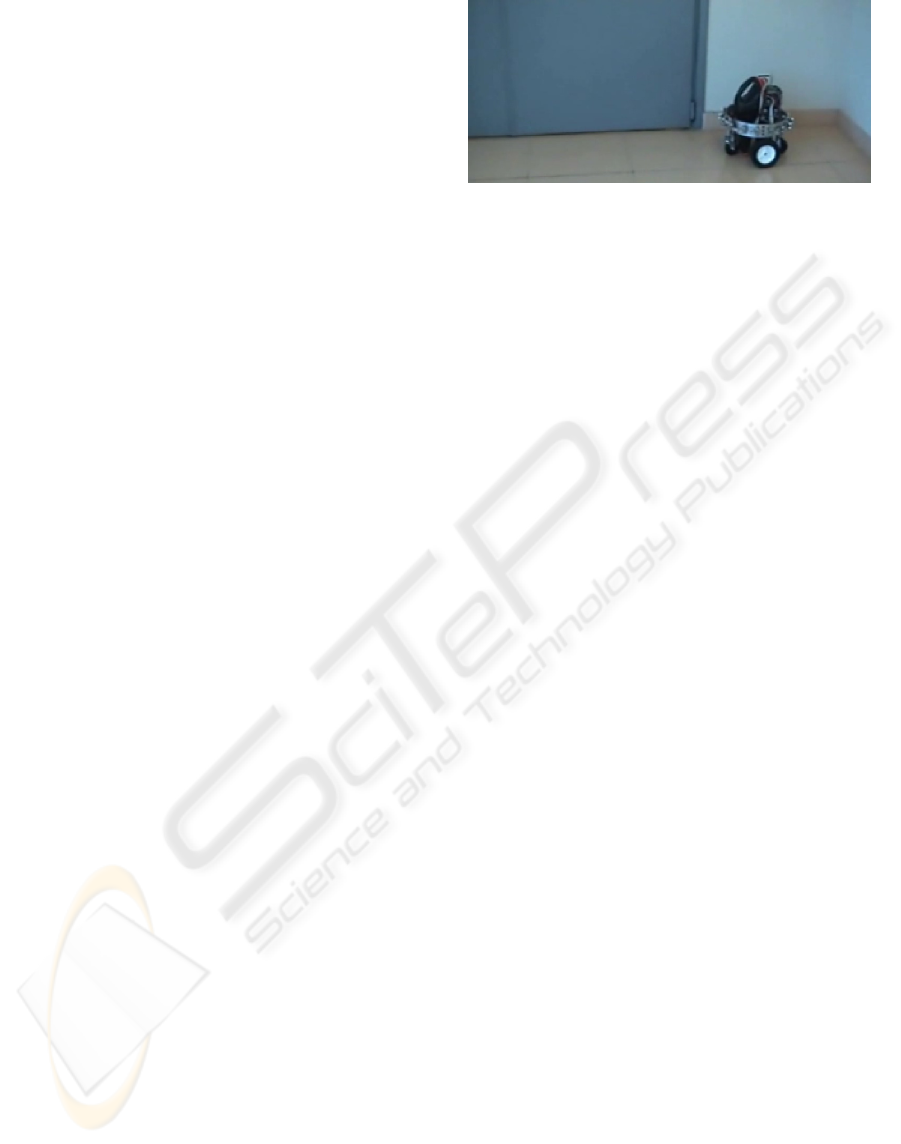
alternatives and navigation strategies. The
conclusions reached (Martinez, 2004) provided the
starting point for the design and construction of the
real prototype described and presented in this paper.
Once the robot had been designed (Figure 2), the
virtual prototype of the robot and the domestic
environment was updated and enhanced (Figure 9),
as described in section 5. The new virtual prototype
was used to test, above all, the controller in the real
prototype and particularly the navigation and
sweeping strategies. The activation of a trace
mechanism showing the robot’s path, as shown in
Figure 9b, was extremely useful for checking the
effectiveness of the sweeping algorithm.
By the end of the process, the real prototype of
the robot vacuum cleaner had been tested
experimentally in simple wall-following and living-
space sweeping tasks. The results for wall following
were positive (Figure 10), although variations were
detected in the estimation of the distance to the wall
whenever the wall material changed (e.g. when the
robot passed in front of a wooden door). By contrast,
the results for the sweeping tasks were worse due to
errors in estimating position using measurements
from the wheel encoders. These errors led to the fact
that the algorithm used for the sweeping of enclosed
areas was inefficient. The main reason for this was
that due to the wheels slipping the measurements
provided by the wheel encoders were inaccurate.
This problem had already been detected in the SIL
simulation with the virtual prototype whenever there
was a change in the surface friction coefficient (e.g.
when the robot moved from a rug onto parquet
flooring, Figure 9b), but was much more serious in
the real prototype.
To draw conclusions from the experimental tests
conducted: the sensing system must be modified or
completed before moving on to a commercial
prototype so that an accurate estimate of the real
position of the robot (the basis of the designed
sweeping algorithm) can be obtained.
7 CONCLUSIONS
This paper presented the prototype of a robot
vacuum cleaner designed and constructed by
IKERLAN. It detailed, above all, the hardware and
software components used, in addition to the
navigation algorithm, the design of which was based
on fuzzy logic. Moreover, an existing virtual
prototype of the robot and its domestic environment
were updated, thereby enabling the fine-tuning and
testing of the real in-built control of the autonomous
robot using SIL (Software-in-the-Loop) simulations.
Finally, the problems arising from the experimental
tests conducted were described in detail, and the
conclusion reached that the sensing system must be
improved so that the real position of the robot,
which forms the basis of the sweeping algorithm
designed, can be estimated accurately.
ACKNOWLEDGEMENTS
The material used in this paper was partly funded by
the Spanish Ministry of Science and Technology and
FEDER (research project DPI2002-04438-C02-01).
REFERENCES
Acroname. 2006. www.acroname.com
Advantech. 2006. www.advantech.com
Electrolux. 2006. http://trilobite.electrolux.co.uk/
Fernandez, M., S. Casas, A. Martinez, L. Nuñez, D.
Guzman, D. Villaverde and J. Landaluze. 2003.
Virtual Prototyping of a Domestic Robot for Design
and Navigation Optimisation. In Industrial Simulation
Conference ISC’2003. 9-11 June, Valencia, Spain.
Irobot. 2006. http://www.irobot.com/home.cfm
Jumptec. 2006. www.jumptec.com
Kahney, L. 2003. Robot Vacs Are in the House. Wired
News. Retrieved January, 2006, from
http://www.wired.com/news/technology/0,1282,59237
,00.html
Karcher. 2006. http://www.robocleaner.de
LinkSys. 2006. www.linksys.com
Martinez, A., L. Nuñez, M. Fernandez, S. Casas and J.
Landaluze. 2004. Virtual Prototyping of a Domestic
Mobile Robot for Design and Navigation
Optimisation. In the International Journal of
Engineering Simulation, ISSN 1468-1137, vol. 5,
number 2, pp. 12-20. July.
Robot Electronics. 2006. www.robot-electronics.co.uk
RTD. 2006. www.rtd.com
Tri-M. 2006. www.tri-m.com
Urzelai, J., J.P. Uribe and J.M. Ezkerra. 1997. Fuzzy
Controller for Wall Following with a Non-
Holonomous Mobile Robot. Fuzzy IEEE.
Zagros Robotics. 2006. www.zagrosrobotics.com
Figure 10: Real Prototype in the wall-following task.
ICINCO 2006 - ROBOTICS AND AUTOMATION
468