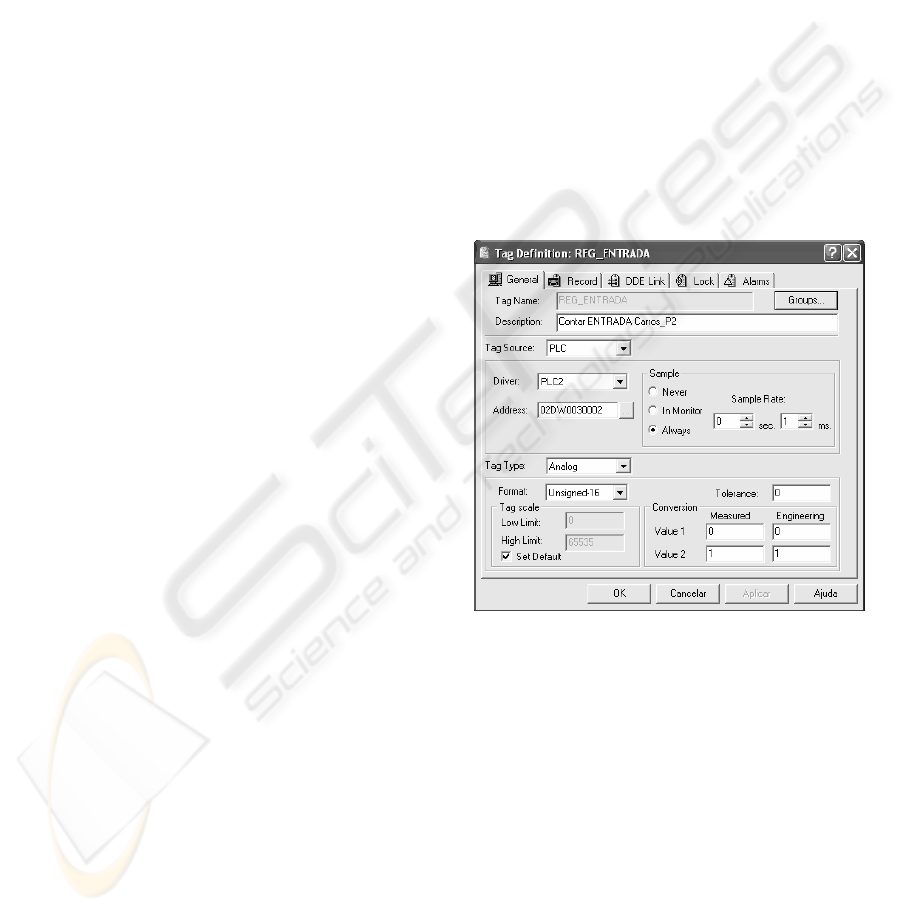
3.3 SCADA Supervisory Control
Loop
System Description: The SCADA system used to
implement this monitoring and control strategy was
a commercial platform: Axeda Supervisor Wizcon
for Windows & Internet V 8.2.
The Driver used in this application to establish the
communication Scada system – Master-PLC was the
Siemens RS232/MPI interface, via the Siemens
software Simatic S7 Prodave. According to this
communication Protocol, a PLC digital variable
address must be defined as NNTXAAAABB, where:
NN = PLC address (from 0 to 32);
T = memory area type (I for Input, Q for
Output and M for memory);
X = variable type (B for Byte, W for Word);
AAAA = slot address (from 0000 to 9999);
BB = variable address (00 to 17).
In the specific case of the prototype tested in this
paper, it is necessary to exchange integer values
between the several local PLCs in order to update
the system overall capacity (actual number of free
places in the park).
The SCADA system receives continuously the
information from all PLCs in the network through
the master-PLC and calculates the number of free
places available in the parking place. This integer
values is on-line updated to the PLC network and
according this value the corresponding state of the
entrance lights (red/ green) is determined. When the
number of free places equals zero, the entrance red
lights in all the park gates are set on, until a car exits
the park. This car exit can take place from one of the
several available gates in the parking place.
The transfer of integer values between the
SCADA system, the master-PLC, and forward, to all
slave-PLCs, it is possible through Data Base
transfer. According to the MPI protocol, an integer
value to be transferred from the PLC to the SCADA
system and vice versa, it must be addressed as
NNTXDDDAAAA, where:
NN = PLC address (from 0 to 32);
T = memory area type (D for Data Block, I
for Input, Q for Output and M for
memory);
X = variable type (B for Byte, W for Word);
DDD = Data Block identification (from 000 to
999);
AAAA = variable byte address in Data Block.
Among the main functionalities of a SCADA
system there is the so called “Tag”. A “Tag” is a
defined variable that permits the exchange of
information between the PLC network and the
SCADA system, in a real-time environment. There
are usually three types of Tags: PLC, Dummy and
Compound. In the PLC Tags the PLC sets the
variable values that are directly transferred to the
Scada program. In the Dummy Tags the value is set
by the user on the Scada interface and transferred to
the PLC address. Finally Compound Tags are set by
the Scada program, following the programmed
operations.
When defining the Tags a set of information is
required, namely: Tag name, Description, Tag
source, Driver, Sample rate, Address and Tag Type.
An example of such Tag definition is illustrated in
Fig. 7.
Figure 7: Tag definition.
The Scada main interface between the system and
the user are the application images. The image
building is a functionality of all SCADA systems
and its main function is to permit the user a quick
visual identification of all system functional
characteristics. An easy identification of the system
Inputs and Outputs permits the user an effective
monitoring and a quick actuation on the process,
when it is necessary.
The developed application used important
features that we named animated images. These
images change geometry characteristics and colours
when their digital variables change the state (on/
off).
TWO LAYER CONTROL STRATEGY APPLIED TO BUILDING AUTOMATION
213