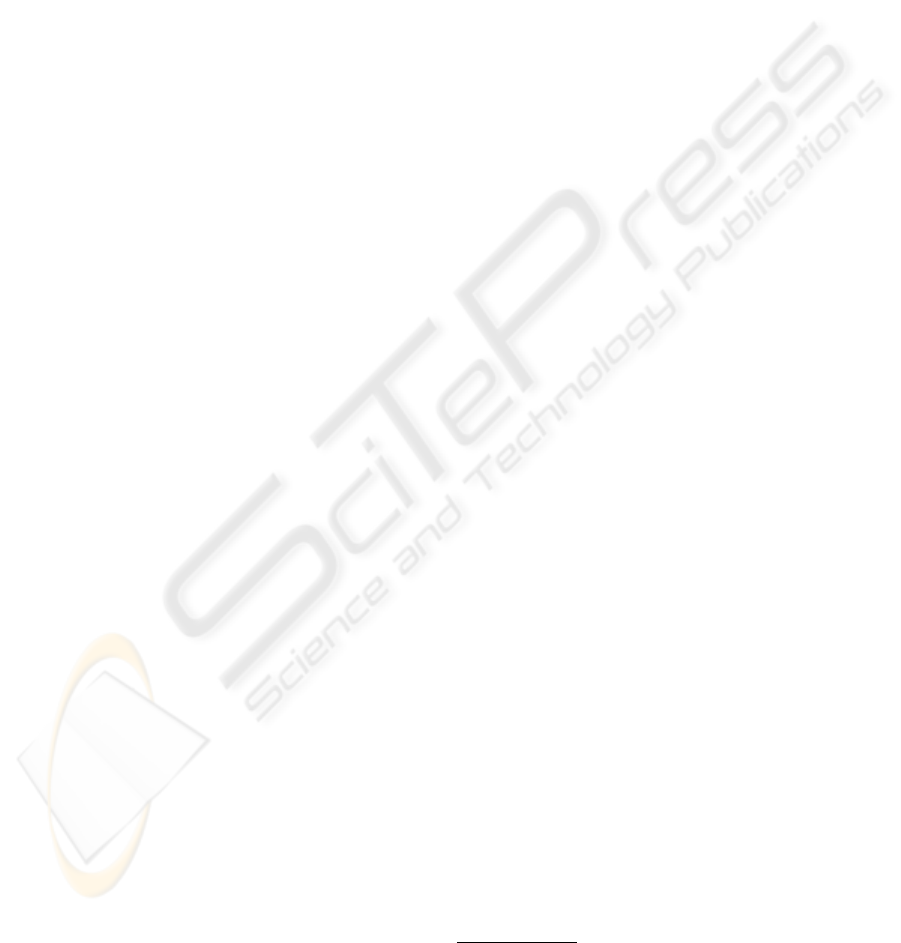
In the above example, depending on the units and
membership definitions, the −1 terms may be a dif-
ferent negative number. Note that some combinations
of faults may yield negative membership values; this
is not a problem if inequality restrictions are consid-
ered, as discussed in section 4.1.
In any of the examples, a coefficient in matrix
C lower (higher) than 1 would indicate a milder
(stronger) effect of the fault on the symptom, as de-
fined by the membership function. Modifying the co-
efficients might be needed in a fine-tuning phase be-
cause not all the faults influence with the same in-
tensity a particular variable. However, taking into ac-
count “sensor” errors f
∗
, an initial setting with mostly
0 and 1 coefficients in C may be enough in order to
achieve a reasonable output.
4 INFERENCE
A fault estimation f is consistent with the observed
symptoms if it is a solution of the basic diagnosis
equation (5). Hence, fuzzy diagnosis amounts to find-
ing the set of solutions of (5). However, some consid-
erations need to be made: indeed, if sensor faults and
modelling errors, f
∗
, are considered, the solution set
includes any conceivable primary fault f , as sensor
faults can accommodate any reading. For instance,
in (6) a value of f
∗
can be calculated for any sensor
reading and any value of f . However, if sensor faults
are not considered, with less faults than sensors the
set of consistent faults will be usually empty, as (5)
will have no solution due to modelling errors. So, the
above idea must be refined for practical usability.
Inference as optimisation. As above discussed,
sensor faults must be considered in practice. Then,
(5) are equality restrictions and a criterion should be
used in order to rank all the feasible solutions. Note
also that inequality restrictions f
i
> 0 implicitly ap-
ply, unless the user casts a meaning for negative fault
severities.
A possible criterion to be chosen is minimising the
norm of the “instrumental” fault component, i.e., giv-
ing as the diagnosis solution the one that achieves less
discrepancy between the measurements and the pre-
dictions C(q)f. The discrepancy µ − C(q)f will be
denoted as inference error.
If the chosen norm is the Euclidean one, fuzzy in-
ference is equivalent to a least squares problem. Let
us consider an equation µ = Cf where sensor faults
are also members of f. This is a linear system of
equations with more unknowns than equations, which
can be solved in the following sense:
The feasible solution f that minimises the squared
Euclidean norm of W f, where W is a diagonal
weight matrix, is given by the pseudo-inverse formula
(Meyer, 2001):
f = W
−2
C
T
(CW
−2
C
T
)
−1
µ (7)
In a practical setting, a high penalisation in W must
be specified for the sensor fault components f
∗
. For
invertibility of W , small positive weights in the pri-
mary faults need to be introduced
3
.
If the chosen norm is the 1-norm of W f (sum of
absolute value of the components), then inference can
be carried out in a linear programming setting. The
LP framework needs to introduce dummy variables
for positive and negative sensor errors f
∗
= f
+
−f
−
,
f
+
> 0, f
−
> 0, to calculate the 1-norm as the sum
of f
+
+ f
−
. This change of variables is standard in
LP textbooks.
Note that LS algorithms produce an “intermediate”
point as a result (not a vertex of the feasible region),
sharing the error between all the equations, as small
errors are not significant (because of the squaring) so
LS tries to reduce big errors. On the contrary, LP pro-
duce a result in a vertex of the feasible solution space,
and increments from either small or big errors weight
the same.
4.1 Constrained Optimisation
Under the proposed settings, it is implicitly assumed
that a reasonable diagnostic should verify f
i
≥ 0 in
all components of the primary faults.
Also, fuzzy concepts saturate in [0, 1]. Hence, si-
multaneous faults yielding the same symptom cannot
fulfill, for instance, 1 = f
1
+ f
2
if they are fully ac-
tive. However, two easy options are available (or a
combination of them) in that case:
• When a fuzzified sensor reading is saturated, re-
place the equality constraint in the diagnosis equa-
tion by an inequality (1 ≤ C
i
f, 0 ≥ C
i
f, where
C
i
denotes the i-th row of C).
• Translate an ordered fuzzy partition on a domain
into numerical values (for instance, {very low, low,
normal, high, very high} into {−2, −1, 0, 1, 2}) in
the spirit of the so-called linguistic equation (Juuso,
1999; Jarvensivu et al., 2001). In this way, the basic
diagnosis equation (5) may involve sensor values
ranging more than [0, 1], but somehow keeping the
linguistic meaning.
Algorithms. LP algorithms incorporate linear in-
equality restrictions seamlessly. However, the least
squares formula (7) must then be discarded and
quadratic programming (QP) routines used instead.
3
Solving y = Cf by standard least squares, f =
(C
T
C)
−1
C
T
µ, is equivalent to the proposed approach
when the primary-fault weights tend to zero and sensor ones
are equal to the same constant.
ENCODING FUZZY DIAGNOSIS RULES AS OPTIMISATION PROBLEMS
37