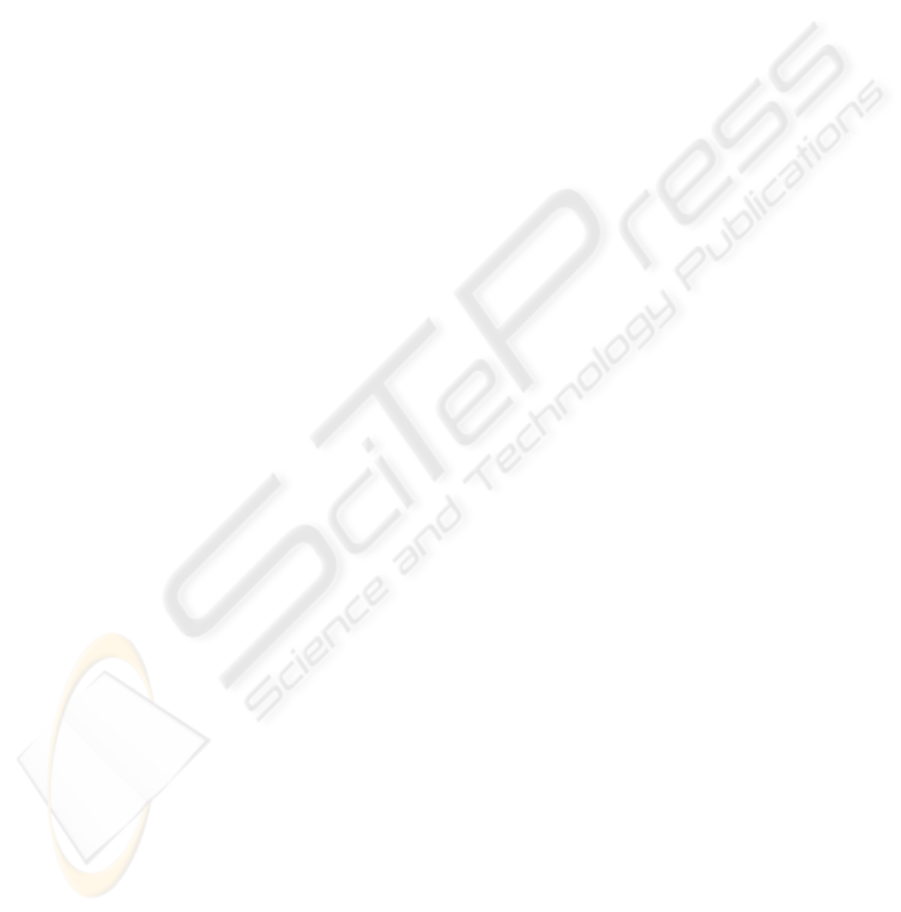
INTERACTION CONTROL EXPERIMENTS FOR A ROBOT WITH
ONE FLEXIBLE LINK
L. F. Baptista
Escola N
´
autica Infante D. Henrique
Av. Engenheiro Bonneville Franco, 2770-058 Paco de Arcos
J. M. M. Martins, J. M. G. S
´
a da Costa
Instituto Superior T
´
ecnico, GCAR/IDMEC
Av. Rovisco Pais, 1049-001 Lisboa Codex
Keywords:
Flexible-link manipulator, closed-loop inverse kinematics, interaction control, real-time control.
Abstract:
One of the major drawbacks of flexible-link robot applications is its low tip precision, which is an essential
characteristic for applications with interaction control with a contact surface. In this work, interaction control
strategies considering rigid and flexible contact surfaces are applied on a two degrees of mobility flexible-link
manipulator. The interaction strategies are based on the closed-loop inverse kinematics algorithm (CLIK) to
obtain the angular references to the joint position controller. The control schemes were previously tested by
simulation and further implemented on the flexible-link robot. The obtained experimental results exhibit a
good force tracking performance, especially for a rigid surface, and reveal the successful implementation of
these control architectures for a robot with one flexible link.
1 INTRODUCTION
The evolution of industrial manufacturing, lead to the
necessity of optimize the production, where the main
goal is to achieve best quality products at lower prices.
The manipulator robot is a crucial automation equip-
ment that fulfill these requirements, due to its high
productivity and easy adaptation to a large number of
complex and repetitive tasks. The manipulator robots
have also the ability to work in adverse environments
to the human workers. Due to these characteristics,
the study of robot manipulator control has received a
growing attention by a lot of researchers during the
last decades, in order to design robots with high per-
formance (Canudas de Wit et al., 1998).
In general, industrial robots have rigid mechanical el-
ements which leads to a high power consumption. To
overcome this disadvantage, lightweight and flexible
links have been considered in the construction of new
robots. These new links allow the same mobility ca-
pacity as the rigid robots with a lower power con-
sumption. Also, due to the lighter weight of the links,
the interaction with the environment, especially in the
case of collision, cause less damage.
When a manipulator robot executes an interaction
task, the tip or end-effector enters in contact with the
environment and a certain force is exerted on the sur-
face. Since it’s necessary to achieve an high preci-
sion tip position to obtain a good interaction force
control, advanced control algorithms have been de-
veloped to obtain a high force tracking performance
(Zeng and Hemami, 1997). However, flexible-link
manipulators exhibit an important drawback in com-
parison with rigid robots, due to the difficulty in con-
trol its tip or end-point position. The flexibility rises
the dynamic coupling, the non-linearities, and gives
to the robot infinite degrees of freedom derived from
the vibration modes of the flexible elements. Due to
these vibrations, the system becomes a non-minimum
phase system (Talebi et al., 1998). The zeros in the
right semi-plan, due to the non minimum phase lead
to an unstable system, when the tip position is directly
controlled through feedback.
To avoid these drawbacks, several techniques to ef-
ficiently control flexible-link robots have been stud-
ied. The control of a flexible manipulator at the joint
level has been established by a lot of authors like
(Khorrami and Jain, 1994) for the tracking problem
and (Vandegrift et al., 1994) for the regulation prob-
lem, among others. One of the proposed strategies
to solve the inverse kinematics problem for flexible
arms, was derived from the closed loop inverse kine-
matics algorithm (CLIK) developed for rigid manip-
ulators (Siciliano, 1990). The inverse kinematics for-
mulation with feedback of joint coordinates and de-
flection variables for constrained flexible manipula-
66
F. Baptista L., M. M. Martins J. and M. G. Sá da Costa J. (2006).
INTERACTION CONTROL EXPERIMENTS FOR A ROBOT WITH ONE FLEXIBLE LINK.
In Proceedings of the Third International Conference on Informatics in Control, Automation and Robotics, pages 66-73
DOI: 10.5220/0001204900660073
Copyright
c
SciTePress