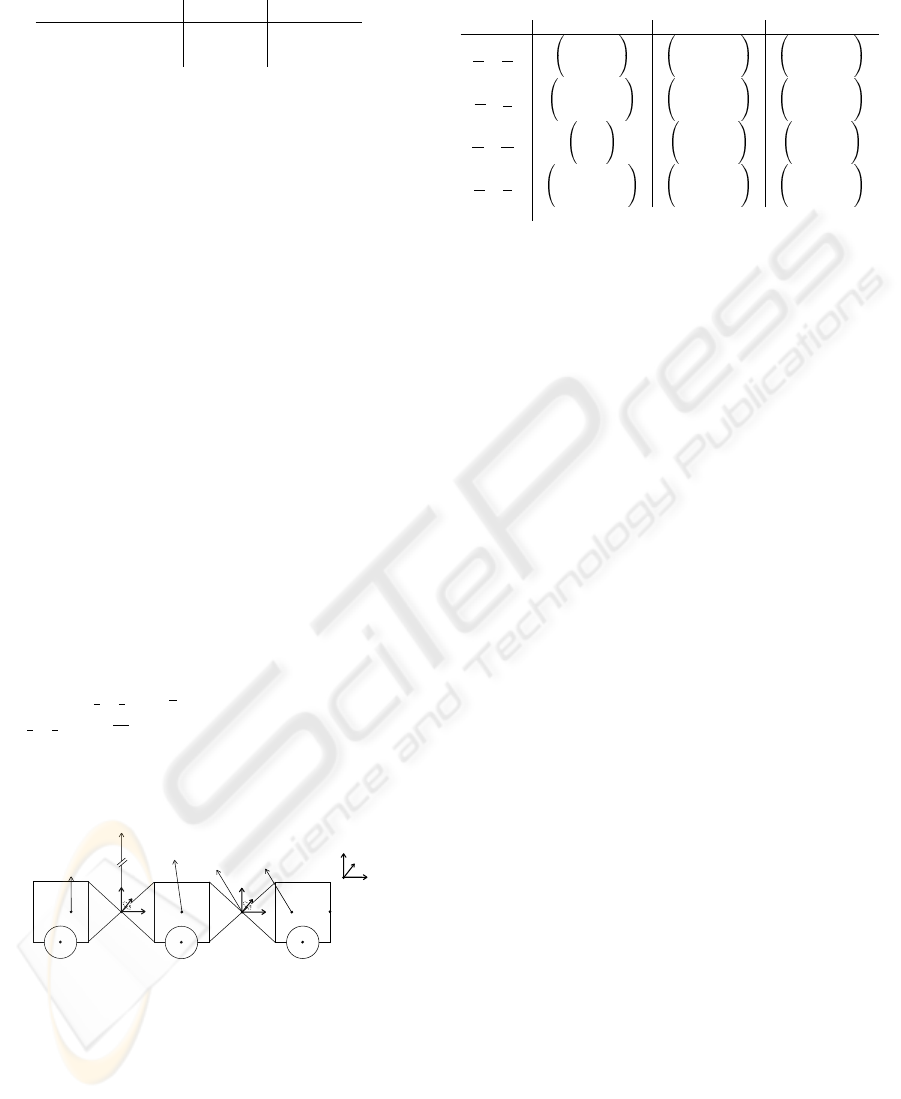
Table 1: Angular and amplitude decomposition.
25 Nm 200 Nm
angular error ±19
◦
±12, 8
◦
amplitude error ±26% ±18, 3%
2005). Amplitude resolution can be optimized by
complex material analyses. As we use the signal
for impedance control, the signal’s quality can be
weighted by impedance control factors M
d
, B
d
and
K
d
. A focus on the angular resolution signal is
therefore possible. With this method influence of the
amplitude of the signal can be minimized, whereas
the angular value of the signal gets strengthened.
5.2 Dynamic Modeling
The dynamic modeling of Kairo-II has been realized
as functional block in the software framework MCA.
Appropriate coordinate systems have been identified
to handle both efficient calculations within the model
and simple sensor fusion with other modules. There-
fore, a simplified dynamic modeling was introduced
that meets the mechanical requirements and reduces
the number of parameters drastically.
Sensor fusion can be implemented in a new module
easily, as all data sources (dynamic modeling, sensor
system) provide data in similar coordinate systems.
The following example depicts the working prin-
ciple of the algorithm (see Figure 6). All robot
joints are positioned in their nullposition. The robot
is fixed at its left end. In applying joint veloci-
ties (ALPHA M qd) 3
1
s
and joint accelerations (AL-
PHA M qdd) 3
1
s
2
to all joints. Forces and moments
within the system arise. They can be calculated ac-
cording to the RNE algorithm. Results are presented
in table 2 and depicted as vectors in Figure 6.
R
4,0
F
4
R
7,0
F
7
R
7,0
f
7
R
4,0
f
4
link 7
link 4
x
y
z
R
1,0
F
1
link 1
J
2
J
5
R
8,0
f
8
=0
COM COM COM
Figure 6: Robot configuration with three segments.
6 CONCLUSION
A control scheme for multi-segmented robots was
presented. As controlling the robot’s redundancy is
both challenging and promising, this scheme can han-
dle the ambiguity of the system. Crucial modules of
the TJ-HIC scheme were identified and implemented
in this paper. As the other - relevant - modules of the
Table 2: Sensor Outputs of the RNE algorithm (forces [N],
moments [Nm]).
i 1 4 7
R
i,0
F
i
0
0
67.17
−14.19
0
99.47
−50.06
0
82.85
R
i,0
f
i
−64.25
0
249.49
−64.25
0
182.31
−50.06
0
82.85
R
i,0
N
i
0
0
0
0
−0.41
0
0
−0.34
0
R
i,0
n
i
0
−106.28
0
0
−54.71
0
0
−10.29
0
control scheme (i.e. trajectory planning and potential
function) are kept to minimal complexity, the control
loop can be closed now.
Future work has to be done in the field of not only
handling but using the redundancy of Kairo-II. In do-
ing so, huge driving capabilities are expected. The
system is then able not only to fulfill a main task but
also an user-defined subtask like positioning an in-
spection module or avoiding obstacles.
REFERENCES
Birkenhofer, C., Hoffmeister, M., Z
¨
ollner, J.-M., and Dill-
mann, R. (2005). Compliant motion of a multi-
segmented inspection robot. In IRS, Edmonton.
Birkenhofer, C., Scholl, K.-U., Z
¨
ollner, J.-M., and Dill-
mann, R. (2004). A new modular concept for a multi-
joint, autonomous inspection robot. In (IAS 8).
Choset, H. and Henning, W. (1999). A follow-the-leader
approach to serpentine robot motion planning. SCE
Journal of Aerospace Engineering.
Fu, K., Gonzalez, R. C., and Lee, C. G. (1987). Robotics
- Control, Sensing, Viion and Intelligence. McGraw-
Hill International Editions.
Hogan, N. (1985). Impedance control: An approach to ma-
nipulation, parts i - iii. ASME J. Dynam. Syst., Meas.,
Contr., 107:1–24.
Khatib, O. (1987). A unified approach to motion and force
control of robot manip ulators: The operational space
formulation. IEEE Journal on Robotics and Automa-
tion, 3(1):43–53.
Salisbury, K. (1980). Acitve stiffness control of manipula-
tors in cartesian coordinates. IEEE Int. Conf. Robotics
and Automation, pages 95–100.
Scholl, K.-U., Albiez, J., and Gassmann, B. (2001). Mca -
an expandable modular controller architecture. In 3rd
Real-Time Linux Workshop.
Scholl, K.-U., Kepplin, V., Berns, K., and Dillmann, R.
(2000). Controlling a Multi-joint Robot for Au-
tonomous Sewer Inspection. In ICRA.
Shah, M. and Patel, R. (2005). Transpose jacobian based
hybrid impedance control of redundant manipulators.
In CCA, pages 1367– 1372.
ICINCO 2006 - ROBOTICS AND AUTOMATION
222