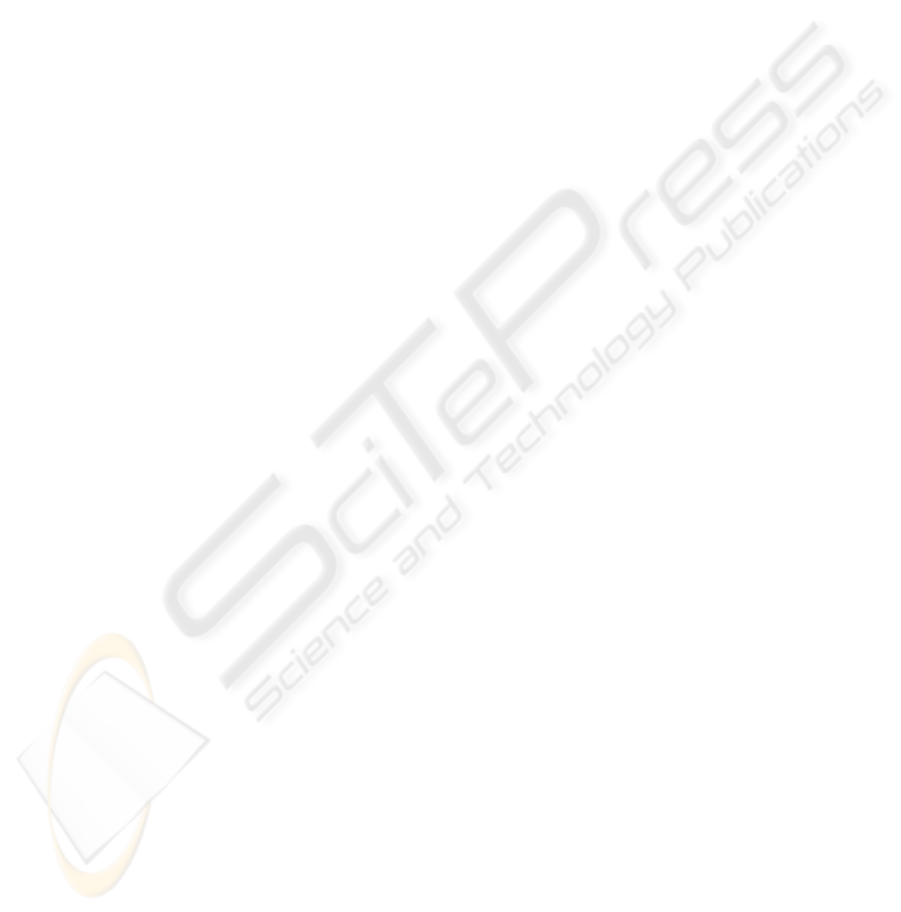
AUTOMATA BASED MODELLING AND SIMULATION
Application in an Industrial Software Environment
Vasileios Deligiannis
Electrical & Computer Engineering Dept., University of Patras, 26500, Rio-Patras, Greece
Stamatis Manesis
Electrical & Computer Engineering Dept., University of Patras, 26500, Rio-Patras, Greece
Keywords: Automata, Modelling, Simulation, Industrial systems.
Abstract: Contemporary industrial systems are hybrid systems, and hybrid automata and Petri Nets are the most used
approaches to model such systems. Despite academic efforts these two approaches did not meet wide
acceptance when proposed for industrial use, mainly because they are application depended. In this paper, a
recently proposed hyper-class of hybrid automata is presented, which seems to cover this weakness.
Illustrating its use, an application of this new formulation method in an industrial software environment is
given. The given example is taken from a chemical industry and uses PID controllers to control continuous
variables, while the whole project was developed in a SCADA software platform.
1 INTRODUCTION
Most contemporary industrial systems are described
as hybrid systems, since they are governed by
discrete state controllers, whose internal state
transitions are triggered by the value of some
measured continuous physical quantity (temperature,
flow rate, time, etc.). The importance of modelling
and simulation of industrial production systems is
generally acknowledged and hybrid automata
(Antsaklis, 2000) and Petri nets (Peterson, 1981) are
the most used approaches for modelling hybrid
systems. But these methods did not meet wide
acceptance when proposed for industrial use,
primarily because they are application depended, or
more accurate domain depended. A new automata-
type method (Deligiannis, 2005) seems to avoid this
dependence, offering the convenience of modelling
various types of industrial systems without any
restrictions on system’s properties. It borrows some
characteristics from several types of automata
(Khoussainov, 2001), such as the control graph with
a finite set of states and transitions between those
states. It models hybrid systems handling both
discrete and real valued variables combining flow,
invariant and guard conditions from hybrid
automata, with clock constraints and delayed inputs
from timed (Allur, 1994) and PLC automata (Dierks,
1997). In addition, introduces new modelling
parameters as reset table at each transition and
hierarchical classification of executable events at
each state. Application independence derives from
the fact that new method is a hyper-set of every
other type of automata and hence is less application
depended compared to any of them.
Apart from the used modelling method and despite
huge advances in the field of control systems
engineering, PID still remains the most common
control algorithm in industrial use today. It is widely
used because of its versatility, high reliability and
ease of operation (Astron, 1995). PID systems’ main
advantage on applying control is that there is no
need to obtain a dynamic model.
In this paper an example of industrial relevance
is presented. A three tank system is modelled, using
the new automata-type model, and implemented for
simulation and verification in an industrial software
environment. A PID controller was developed to
control system’s continuous dynamics.
Implementation took place in CX – Supervisor, a
Supervisory Control And Data Acquisition
(SCADA) software by OMRON. Taking advantage
of software’s animation capabilities, screens
193
Deligiannis V. and Manesis S. (2006).
AUTOMATA BASED MODELLING AND SIMULATION - Application in an Industrial Software Environment.
In Proceedings of the Third International Conference on Informatics in Control, Automation and Robotics, pages 193-196
DOI: 10.5220/0001211401930196
Copyright
c
SciTePress