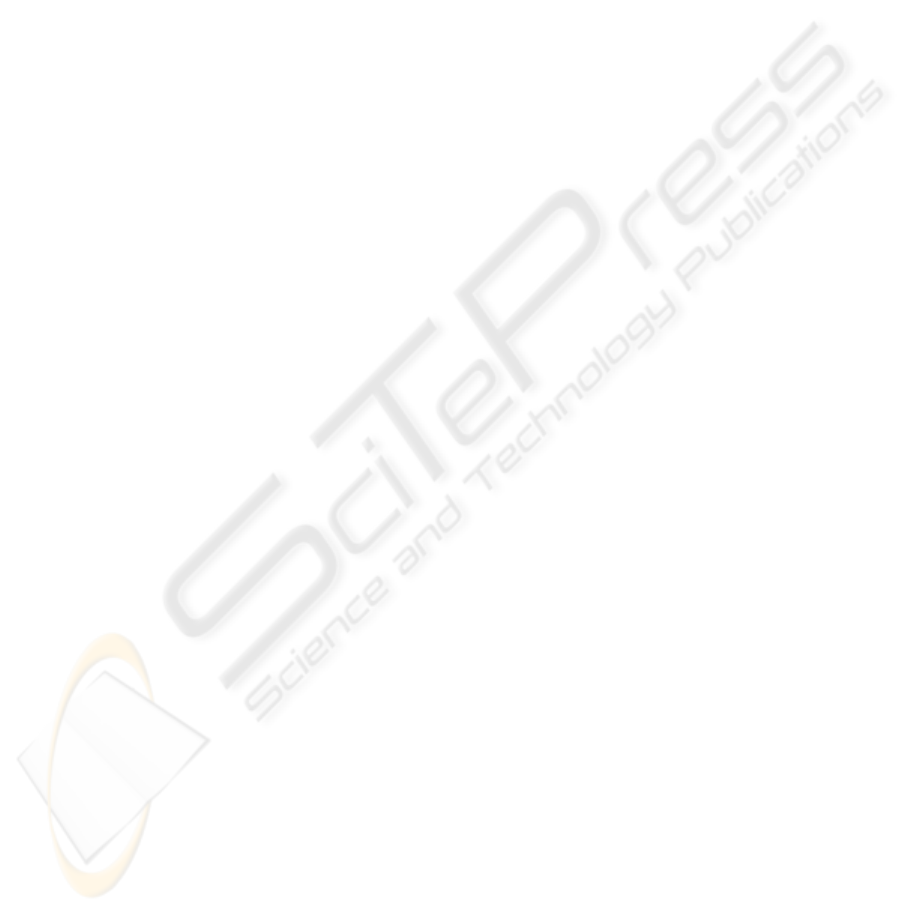
REFERENCES
Burk, R. J., 2001. Ionizing Radiation-Safety Standards for
the General Public – Position Statement of the Health
Physics Society [online]. Health Physics Society.
Available from:
http://hps.org/documents/publicdose.pdf [accessed
January 2006]
Brokk 40 robots information [online]. Available from:
http://www.brokk.com/ [accessed February 2006]
Cox, D., Cetin, M., Pryor, M., and Tesar, D., 1999.
Requirements for Modular Dual-Arm Robot
Architecture for Use in Deactivation and
Decommissioning Tasks. ANS 8
th
International
Topical meeting on Robotics and Remote Systems,
9(4), pp. 1-14, American Nuclear Society.
C. O. Alford., and S. M. Belyeu., 1984. Coordinate control
of two robot arms. IEEE International Conference of
Robotics, pp. 468-473.
Cox, J. D., Rackers, K., and Tesar, D., 1995. Cooperative
Manipulation Experiments Using a Dual-Arm Robot.
IEEE Priceedings.
Cox, D., 2004. Cooperative manipulation Testbed
Development-Kinematics. 17
th
Annual Florida
Conference on the Recent Advances in Robotics
(FCRAR), Florida.
Cox, D., 2002. Mock-up of Hazards Material Handling
Taks Using a Dual-Arm Robotic System. Proceedings
5
th
World Automation Congress, Orlando.
Dauchez, P., Fournier, A., and Jourdan, R., 1988. Hybrid
Control of a Two-Arm Robot for Complex Tasks. 2
nd
International Symposium on Robotics and
Manufacturing (ISRAM), New Mexico.
Fu, K.S., Gonzalez, R.C., and Lee, C.S., 1987. Robotics
Control, Sensing, Vision, and Intelligence. Singapore:
McGRAW-HILL.
Hydro-Lek Manipulator information [online]. Available
from:
http://www.hydro-lek.com/ [accessed October
2005]
International Atomic Energy Agency (IAEA), 2001. State
of The Art Technology of Decommissioning and
Dismantling of Nuclear Facilities. Technical Report,
no. 395, Vienna.
International Atomic Energy Agency (IAEA), 2001.
Methods for The Minimization of Radioactive Waste
From Decontamination and Decommissioning of
Nuclear Facilities . Technical Report, no. 401, Vienna.
International Atomic Energy Agency (IAEA),
1994.Classification of Radioactive Waste. A safety
guide, Vienna.
Lewis, F.L., Dawson, D.M., and Abdallah, C.T., 2004.
Robot manipulator Control Theory and Practice, 2
nd
ed. New York: Marcel Dekker.
Measson, Y., David, O., Louveau, F., and Friconneau, J.
P., 2002. Technology and Control For Hydraulic
Manipulator. 22
nd
Symposium on Fusion Technology
(SOFT), Helsinki.
Miyabe, T., Konno, A., Uchiyama, M., and Yamano, M.,
2004. An Approach Toward an Automated Object
Retrieval Operation with a Two-Arm Flexible
Manipulator. The International Journal of Robotics
Research, 23(3), pp. 275-291.
Noakes, M. W., 1999. Dual Arm Work Module
Development and Applications. Proceedings of The
American Nuclear Society Eighth ANS Topical
Meeting on Robotics and Remote Systems, Pittsburgh.
National Instruments product information [online].
Available from: http://www.ni.com/ [accessed January
2006]
Oussama, Khatib., 1987. A unified approach for motion
and force control of robot manipulators: The
operational space formulation. IEEE Journal of
Robotics and Automation, RA-3 (1), pp. 43-53.
Parker, L.E., and Drapper, J.V., 1999. Robotics
Application in Maintenance and Repair, 2nd ed. New
York: Wiley.
RODDIN, Crane-deployed work platform information
[online]. Available from:
http://www.cybernetix.fr/modules.php?&op=modload
&name=cybernetix&file=product&topic=14&bt=nucl
eaire&newlang=eng [accessed November 2005]
Roman, H.T., 1992. Nuclear Plant – Experience and
Future Projections. 40
th
Conference on Remote System
Technology.
SAMM Manipulator information [online]. Available from:
http://www.cybernetix.fr/modules.php?&op=modload
&name=cybernetix&file=product&topic=14&bt=nucl
eaire&newlang=eng [accessed November 2005]
Stevens, R., Brook, P. Jackson., K. and Arnold, S., 1998.
Systems engineering, coping with complexity. London:
Prentice Hall Europe.
Seward, D., 1999. The development of intelligent mobile
robot. Thesis (PhD). Lancaster University.
Titan Manipulators information [online]. Available from:
http://www.sub-atlantic.co.uk/products.html [accessed
March 2006]
U.S. Nuclear Regulatory Commission [online]. Available
from: http://www.nrc.gov/reading-rm/doc-
collections/cfr/part020/ [accessed November 2006]
Zied, Khaled., 2004. Investigation of processes and tools
for rapid development of intelligent robotic systems.
Thesis (PhD). Lancaster University.
HUMAN ARM-LIKE MECHANICAL MANIPULATOR - The Design and Development of a Multi -Arm Mobile Robot
for Nuclear Decommissioning
175