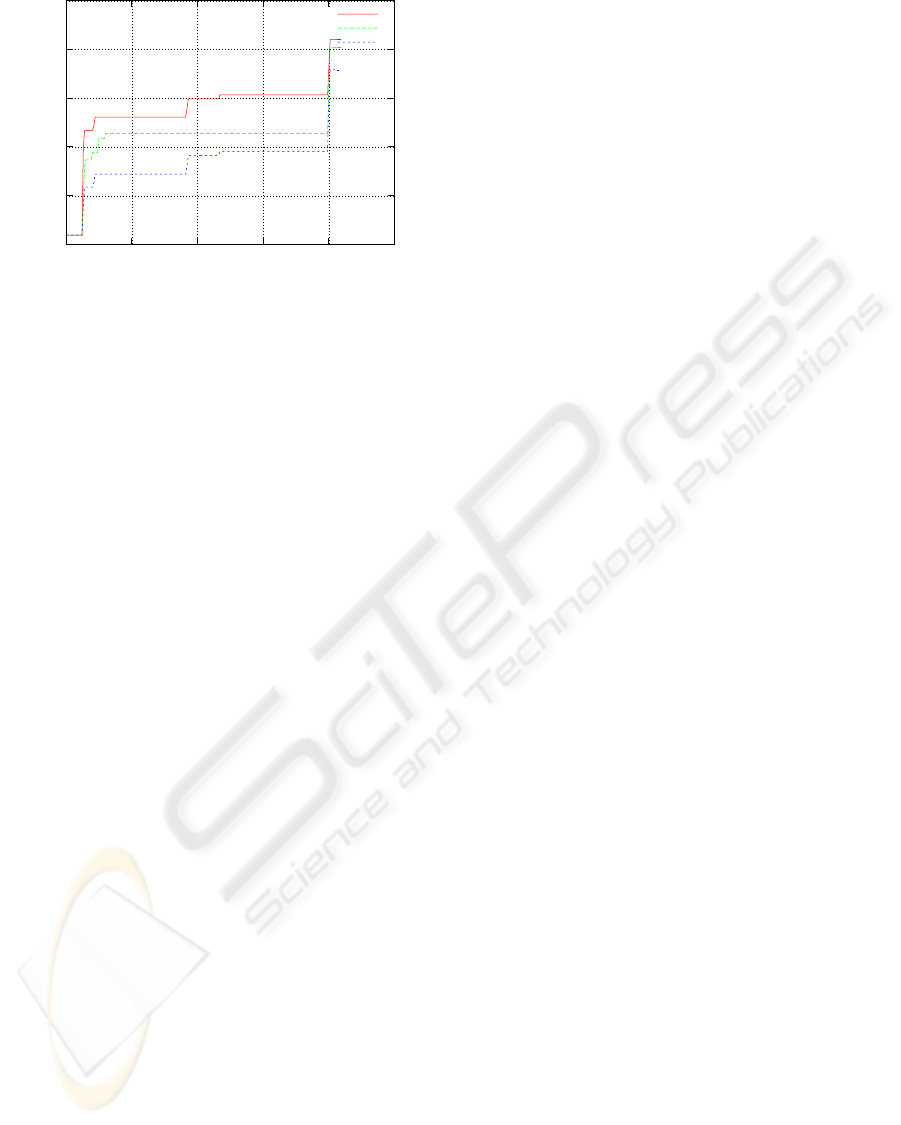
0
0.05
0.1
0.15
0.2
0.25
0 50 100 150 200 250
Bus Response [s]
CAN ID x 10e-1
Home1
Home2
Home3
Figure 4: CAN bus response.
during normal operation of SAM modules the maxi-
mum theoretical response time can not be achieved.
4.1.2 Bus Characteristics
The basic characteristics of CAN data bus used on-
board the Ae270 aircraft are:
• transfer rate 27.7 Kbps,
• average load of CAN bus on Ae270 is 33.9 %,
• probability of undetected message corruption in a
CAN network is around 1 · 10
−13
,
• probability of undetected failures per flight hours is
2.7 · 10
−8
,
• length of CAN data bus is 13.5 m,
• the number of nodes (SAM units) is 8.
System of Avionic Modules SAM was awarded the
Gold Medal of 43th International Engineering Fair
in Brno, Czech Republic, 2001. In December 2005
the Unis company obtained an approval from Czech
aviation authority (CAA) for its System of avionics
modules (SAM). Next in December 2005 the Euro-
pean Aviation Safety Agency (EASA) issued a type
certificate for an Ae270 civil aircraft produced by Aero
Vodochody. Specific functions onboard the Ae270 air-
craft is performed by SAM developed by Unis. The
type certificate for US market was issued by the Fed-
eral Aviation Agency on February 24, 2006.
5 CONCLUSION
During the development project the CAN communi-
cation data bus was successfully implemented into the
mobile robot and avionics control system. Its perfor-
mance and reliability satisfy requirements of individ-
ual systems and their standards.
The next step for the future will be implementation
of CAN communication data bus into more complex
robotic systems like a manufacturing robotic system.
Performed tests on SAM proved CAN suitability in
advanced avionics systems.
Type certification issued for avionics system with
described communication data bus for use in civil avi-
ation represents one of the first realisation of similar
project in the world.
ACKNOWLEDGEMENTS
The analysis of commercial off the shelf data buses
for robotics and airborne applications were acquired
using the subsidization of the Ministry of Industry and
Trade of the Czech Republic, research plan FI–IM/084
”Commercial Off The Shelf (COTS) Databuses De-
velopment for Advanced Avionics and Airborne Sys-
tems (AIR-COTS)”.
Hardware and software development and physical
modules were realized and project was supported by
UNIS, spol. s r.o.
REFERENCES
SZABO
´
, I., OPLUS
ˇ
TIL, V. Distributed CAN Based Control
System for Robotic and Airborne Applications. In
ICARV, 5th International Conference on Control, Au-
tomation, Robotics and Vision. Singapore: 2002.
SZABO
´
, S
ˇ
., ET AL. Autonomous mobile robot with multi-
processor control system. 7th International Workshop
on Advanced Motion Control, AMC 2002. Maribor,
Slovenia. ISBN 0–7803–7479–7.
SZABO
´
, S
ˇ
. Research of local and global navigation methods
for autonomous mobile robot with multiprocessor con-
trol system. IEEE International Conference on Indus-
trial Technology, IEEE ICIT 2003. Maribor, Slovenia.
ISBN 0–7803–7852–0, ISBN 0–7803–7853–9 (CD).
SVAC
ˇ
INA, D., MIKULA, J. Compliance Report for CRI S-2.
Description of CAN and SAM in Ae270 airplane. Doc-
ument No.: VF-401-AVIO-001, revision: 040322ds.
Unis spol. s r.o.: 3/22/2004.
CAN Specification. Bosch, 1995.
<http://www.can.bosch.com>
CANaerospace. Michael Stock, Flight Systems, 2001.
<http://www.stockflightsystems.com>
System of Aviation Modules (the SAM) for Ae270 aircraft.
Technical specification No.TP-3100-01-01-X, UNIS
Ltd, Brno, Czech Republic. rev. 0, 2001.
CANalyzer and DENalyzer 5.2. The Tools for Comprehen-
sive Network Analysis. Vector, 2005.
<http://www.vector-cantech.com>
DISTRIBUTED CONTROL SYSTEMS BASED ON COTS COMMUNICATION DATA BUS
85