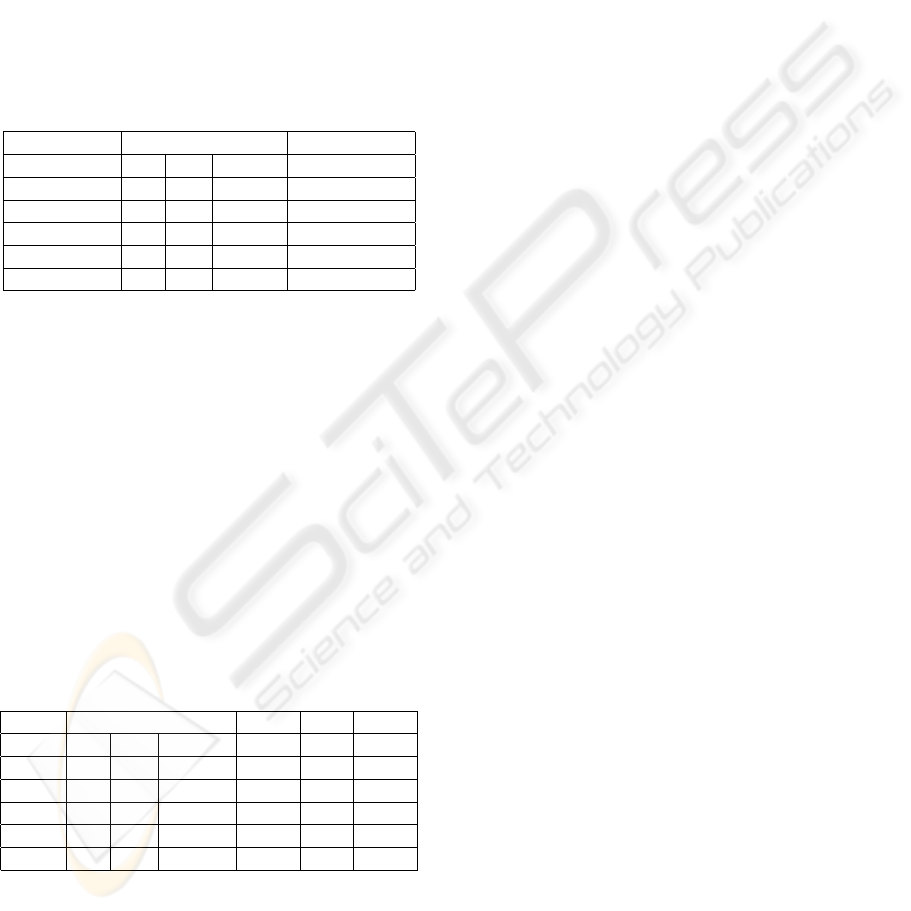
the next item, comparsion is made between TS pa-
rameters of previous works and new TS parameters
used in the presented experiments.
3.3 Comparing Results
Table 2 shows a comparsion among initial FAM solu-
tion, NTS solution (At · 1, St · 10 and Sp · 18) and
the solutions obtained with 3 minimization policies
weights in previous works (Rodrigues and G
´
omez,
2005).
Table 2: Comparsion among initial solution and policies of
minimization considering nbmax = 100 and tabu list size
= 10.
Minimizing decision variables best iteration
St Sp At
St 28 20 891 7
Sp 32 20 709 7
At 56 30 451 16
NTS 32 20 709 7
FAM 40 20 1026 -
The initial solution (FAM) groups parts with same
PF, forming a sequence with minimum switching in-
stants time (20 minutes). The increasing of Sp can-
not improve z and the tool replacement time remains
the same. The St minimization results in less tool re-
placement time and a higher tardiness value, accord-
ing to the previous experiments. The At minimization
reduces 575 minutes the tardiness time (
∼
=
56%), in-
creasing the tool removal and tool replacement time.
Table 3 shows the impact of the variation of TS pa-
rameters in the decision variables of z, considering
the initial, solution, NTS solution and minimization
policies.
Table 3: Comparsion among initial solution and policies of
minimization. BI = best iteration; TL = tabu list size; NB =
nbmax.
Min Desision variables BI TL NB
St Sp At
St 28 20 891 7 50 500
Sp 32 20 624 70 50 100
At 56 30 311 1712 500 1000
NTS 32 20 397 43 50 100
FAM 40 20 1026 - - -
The increasing of tabu list size doesn’t contribute
for improvement of any decision variable in St min-
imization. Its influence is low in Sp minimization,
reducing the tardiness time in 85 minutes. With the
NTS solution, the variation results in a better At time,
while St and Sp remain the same value. It was needed
a higher variation of TS parameters to find a better re-
sult of At, when its minimization is considered.
4 CONCLUSIONS
The experiments presented in this paper has the ob-
jective of investigate the influence of TS paramenters
in a computational model developed to deal with Job
Shop Scheduling Problem with tooling and due date
constraints. This model allows to manage three deci-
sion variables of an objective function: tardiness, tool
replacement and tool removal. Previous experiments
shows a conflict between minimizing tool replace-
ment and tool removal versus tardiness. Those expri-
ments shows the positive influence of the increasing
of the tabu list size and nbmax number in minimiza-
tion of tardiness.
Experiments were made, where these TS parame-
ters were variated. In the initial experiments, tabu
list size was variated, and the increasing of this pa-
rameter results in better At time. It noticed that some
values assigned to tabu list size minimizes At more
than other values. In the second type of experiments,
nbmax was increased, considering the best value of
tabu list size. The reduction of At value obtained was
the same of the initial experiments. The tabu list size
parameter is the main factor in the diversification of
the search, determining the variation of At compo-
nent.
REFERENCES
Glover, F. and Laguna, M. (1997). Tabu Search. Kluwer
Academic Publishers.
G
´
omez, A. T. (1996). Modelo para o seq
¨
uenciamento de
partes e ferramentas em um sistema de manufatura
flex
´
ıvel com restric¸
˜
oes
`
as datas de vencimento e
`
a ca-
pacidade do magazine. PhD thesis, Instituto Nacional
de Pesquisas Espaciais, S
˜
ao Jos
´
e dos Campos, S
˜
ao
Paulo, Brasil.
Groover, M. P. (2001). Automation, production systems and
computer-integrated manufacturing. Prentice-Hall,
second edition.
Hertz, A. and Widmer, M. (1996). An improved tabu search
approach for solving the job shop scheduling problem
with tooling constraints. Discrete Applied Mathemat-
ics, 65:319–345.
Kusiak, A. and Chow, W. S. (1987). Efficient Solving of the
Group Techonology Problem.
Rodrigues, A. G. and G
´
omez, A. T. (2005). Production time
minimization strategies: a Tabu Search approach. In
Annals of the 2nd ICINCO - International Conference
on Informatics in Control, Automation and Robotics.
ICINCO 2006 - INTELLIGENT CONTROL SYSTEMS AND OPTIMIZATION
220