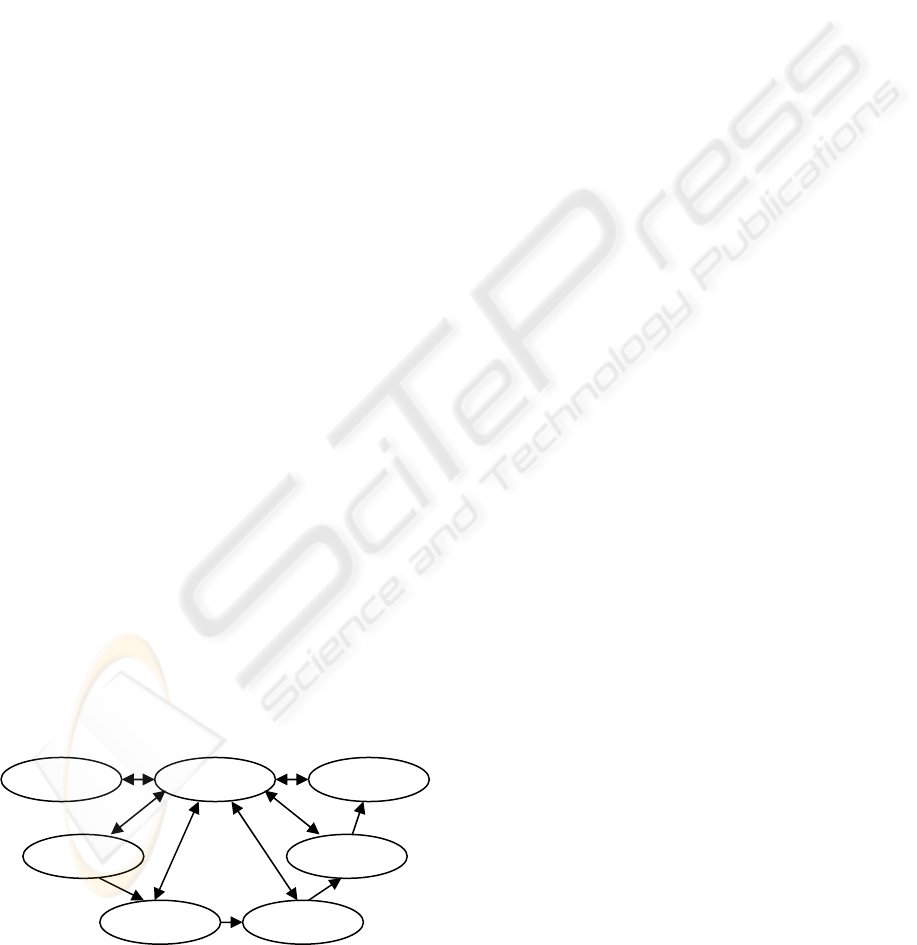
for time critical process control task. The previous
version (QNX v4) contained a lot of special features
focusing on the primary aim, the very good real-time
performance. In those times the robot control
software system was very complex, containing more
than ten separate, but heavily communicating
processes.
Recently the whole software system was ported
under the new version of the operating system, the
so called QNX Neutrino. This is the 6
th
version (the
5
th
was omitted by the developer) and the whole
software suite is called QNX Momentics. It contains
not only the core operating system and numerous
supporting utilities, but a graphical user interface
(GUI) called Photon and a full featured development
environment as well.
Both versions of the operating system have
microkernel based architecture. The small central
kernel provides only the most important services
such as pre-emptive scheduling, status handling and
the basic communication services. A whole desktop
environment is slower in a microkernel architecture
system, but the system builders and software
developers have the ability to build a reduced,
efficient, very fast environment. This aim is
supported by the modularity and the fine tuneable
scheduling mechanism. The most important change
between the mentioned versions is that the process
based scheduling changed to a thread based one.
Another significant change is made in the
philosophy, and instead of using vendor specific
methods, the solutions according to the POSIX
standard are implemented.
Following the evolution, the whole robot control
software was rewritten last year according to the
new operating system version. The process structure
of the new robot control software is shown in Figure
3. The original robot plant used the Advanced Robot
Programming System (ARPS) as the robot
programming language. This environment was
implemented using the own developed robot
controller as well. Since the scheduling is now based
on the threads instead of processes, the structure is
quite simple. The last process, the one responsible
for MiniForce communication, is the most recent
software development. It was written and fitted in a
few months later than the software relocation took
place.
The participants of this research and
development project at the Department of
Automation and Applied Informatics have important
achievements. The most important outcome is the
integration of the sensor system and the start of the
software implementation of various methods based
on the capabilities of the hardware. However, there
is a lot of work to be done in the field of modern
robot control systems.
ACKNOWLEDGEMENTS
The project of studying modern robot control
algorithms and their realization in a real
environment is supported by Hungarian Research
Found (OTKA, grant No. T029072, grant No.
T042634).
REFERENCES
Tevesz, G., Bézi, I. And Oláh, I., 1997. A Low-cost Robot
Controller and its Software Problems. In Periodica
Polytechnica Ser. El. Eng. Vol. 41, No. 3., pp. 239-
249
Hankó, T., 2004. Hatkomponensű erő-nyomatékérzékelő
illesztése PCI buszra. (A PCI bus interface for six
component force torque sensor.) Diploma work, in
Hungarian, Department of Automation and Applied
Informatics, Budapest University of Technology and
Economics
Oláh, I., Tevesz, G., 2002. Software Problems of an
Experimental Robot Controller Based on QNX Real-
Time Operating System. In Periodica Polytechnica
Ser. El. Eng. Vol. 46, No. 3-4., pp. 151-161
Oláh, I., Tevesz, G., 2005. An Experimental Robot
Controller for Force-Torque Control Tasks. The
International Journal of INGENIUM 2005 (4) –
Engineering Achievements Across the Global Village,
edited by Janusz SZPYTKO, Cracow-Glasgow-
Radom, pp. 477-484
Figure 3: The process structure.
Kernel Init
Pendant
Interprete
Pathgen
Control
MFCom
MULTIPROCESSOR ROBOT CONTROLLER - An Experimental Robot Controller for Force-Torque Control Tasks
543