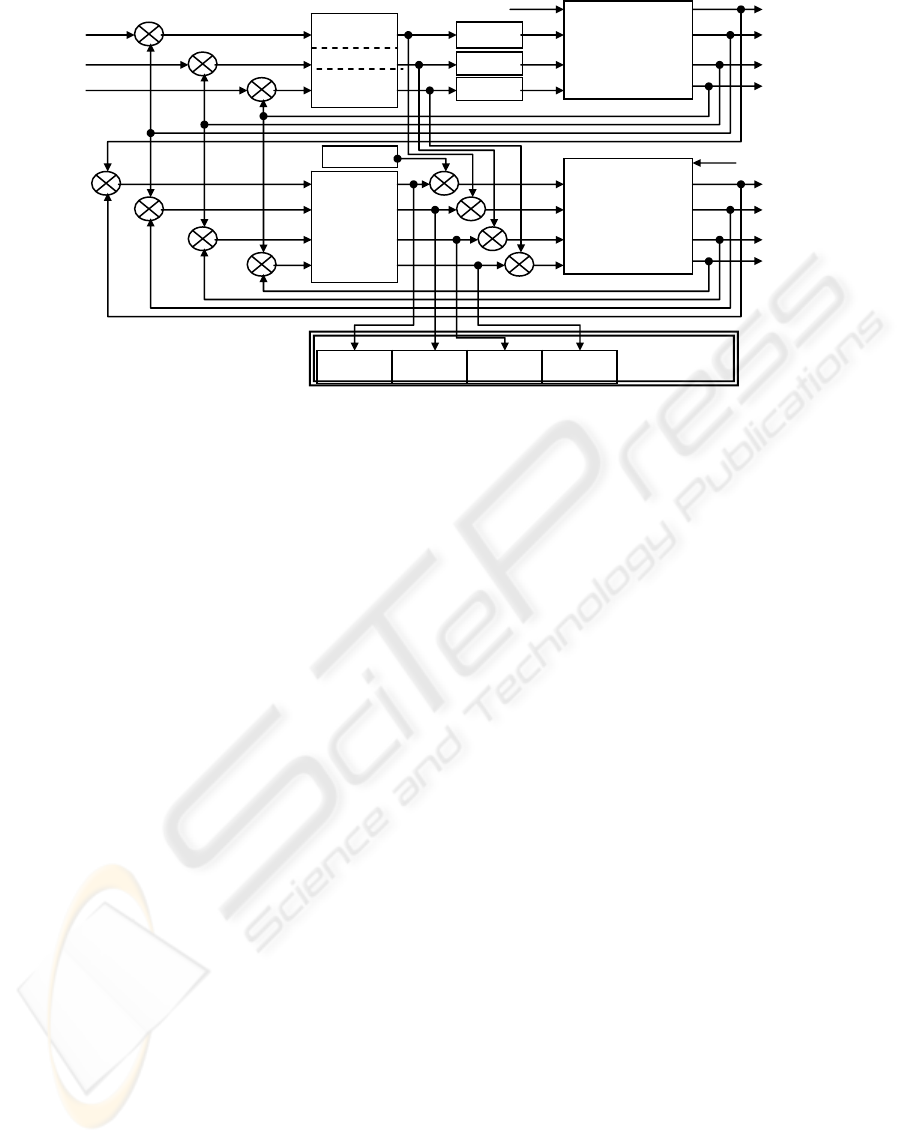
the control equipment, and this impose an adequate
method to choose the fault measurable outputs pairs.
In order to chose the corect perturbation-output
pairs, we use the sensitivity matrix method. For
experimental studies we implemented the fault
detection structure presented in figure 6, as extension
of the elements presented in the first part of the paper
(figure 2).
The structure can be easily implemented in the
robot supervising computers that collect information
about the robot arm. This structure does not require
supplimentary equipment, and it can be implemented
for the existing monitoring digital control system of
the robot.
6 CONCLUSIONS
In this paper it is presented an extension of the
algorithm developed in authors’ paper (Ivanescu,
2000). The results of this algorithm are:
- The resolute decision in fault conditions to continue
or not the movement of robot arms
- The diminution of the control times
- The diminution of memory space allocated for
database.
- The use of a simple algorithm for control imple-
mented on a small controller.
In the future it is possible to develop some control
algorithms in fault free conditions using the fault
zone definitions. As a result of this analyse it is
possible to develop the control of the robot arm only
with one or two joint command.
REFERENCES
Chow Y., A.Willsky, 1984. Analytical Redundancy and
Design of Robust Failure Detection Systems, IEEE
Trans. Aut. Contr., AC-29(7), pp. 603 – 614.
Isermann, R., 1997. Supervision, fault detection and fault
diagnosis methods - An introduction, Control
Engineering Practice, 5(5), pp. 639 – 652.
Ivanescu, M., M. Vinatoru, E. Iancu, 2000. Robotic Arm
Control in Fault Condition, Proceedings of the
IASTED International Conf. Artificial Intelligence and
Soft Computing, Banff, Canada, vol.I, pp. 361-365.
Merrill, W., B. Lehtinen, J. Zeller, 1984. The Role of the
Modern Control Theory in the Design of Control for
Aircraft Turbine Engines, AIAA Journal of Guidance
and Control, 7(6), pp. 652 – 661.
Vînătoru, M., E. Iancu, C. Vînătoru, R.J.Patton, J. Chen,
1998. Fault Isolation Using Inverse Sensitivity
Analysis, International Conference on Control'98,
Swansea, England, vol. 2, pp. 964-968.
Vinatoru, M., E. Iancu, C. Vinatoru, 1997. Robust control
for actuator failures, Proceedings of 2nd IFAC
Symposium ROCOND'97, Budapest, pp. 537 - 542.
Viswanadham, N., K. D. Minto, 1988. Robust Observer
Design with Application to Fault Detection,
Proceedings of American Control Conference, Atlanta
1988, 1393– 1399.
Viswanadham, N., J. H. Taylor, E. C. Luce, 1987. A
Frequency-Domain Approach to Failure Detection and
Isolation with Application to GE-21 Turbine Engine
Control Systems, Control Theory and Advanced
Technology, 3(1). pp. 603 - 609.
Willsky, A.S., A Survey of Design Methods for Failure
Detection in Dynamic Systems, Automatica, 12(6),
1976, 601-611.
Figure 6: Fault detection block diagram.
F
AC1
AC2
θ
1
*
θ
2
*
AC3
θ
3
*
-
-
-
Controllers
Controllers
E
4
Real
Process
Robot
θ
2r
θ
1r
X
gr
θ
3r
E
3
E
2
Fault display
X
i
=
. . . . .
Actuator3Actuator2Actuator1
Fault
Detect
DE
Robot
Process
Simulator
θ
2m
θ
1m
X
gm
θ
3m
DE
DE
DE
-
-
-
-
X
F
t
FAULT DETECTION OF THE ACTUATOR BLOCKING - Experimental Results in Robot Control Structures
551