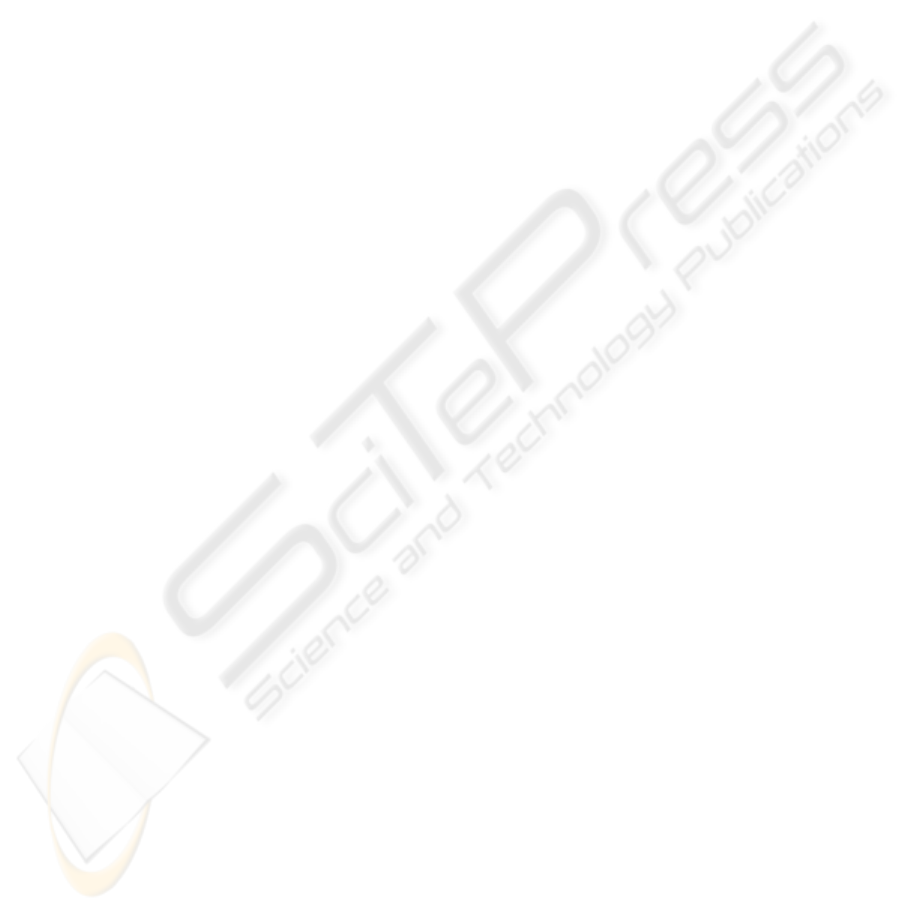
decisions U
p
(s), procedures that realize the function
f (in the most cases it is a vector function), i.e. deter-
mine the next state (x
0
, t
0
) = f(u, x, t), procedures
that examine if the state belongs to the set S
N
or S
G
.
The basic structure of a fixed DMP (Def.2.1) is usu-
ally created on a basis of process technology descrip-
tion. Basing on additional expert knowledge and/or
analysis of DMP subsets of states can be differenti-
ated, for which best decisions or some decision choice
rules R (control rules) are known. Similarly, some
subsets of advantageous or disadvantageous states for
the controlled process can be determined. Formally,
the knowledge allow us restrict sets of possible deci-
sions U
p
.
Knowledge represented by the basic knowledge
structure DMP (Def.2.1) enriched by expert knowl-
edge create the hybrid knowledge based model
(HKBM) of DMP. The knowledge can be enriched
further additionately as a result of simulation exper-
iments.
Basing on the model of DMP different classes
of algorithms can be formally defined and analysed.
For example in (Dudek-Dyduch and Dyduch, 1992),
(Tadeusiewicz and Dudek-Dyduch, 1998), classes of
branch & bound algorithms for DMP control opti-
misation have been differentiated as well as some
rules of automatic creation of lower bounds have been
given. In the next section application of HKBM of
DMP for intelligent, learning algoritm is presented.
3 SEARCH METHOD WITH
GATHERING INFORMATION
The most popular search algorithms consist in gener-
ating consecutive, possibly better and better, trajecto-
ries. They use a specially created function or local
optimisation task for the choice of the best decision
at each state of the generated trajectory. The crite-
rion for local optimisation is called a preference func-
tion or simply heuristics. In this section we present a
conception of algorithms that gain information on the
process and also use expert knowledge.
In the author’s earlier paper (Dudek-Dyduch and
Fuchs-Seliger, 1993), (Dudek-Dyduch and Dyduch,
1993), a certain general 3-stage method for designing
local optimisation task is proposed. Let us recall it
briefly.
At the first stage, one formulates some conditions
for the optimal (suboptimal) solution. They refer di-
rectly to subsets of decisions, or/and determine the
state sets that are advantageous (or disadvantageous)
from the criterion point of view or for a possibility
of generation of an admissible trajectory. The condi-
tions can result from theoretical analysis of the model
or can be formulated by experts.
At the second stage, one determines a local optimi-
sation task. In order to do it, the information about the
distinguished, at the first stage, advantageous or dis-
advantageous states as well as information on S
G
, S
N
and sets of possible decisions is used. As we need the
generated trajectory to run only through the advanta-
geous states and to avoid the disadvantageous ones, it
seems most natural to introduce any measure of dis-
tance in the state space, and to assume some local
criterions.. It was explained in (Dudek-Dyduch and
Dyduch, 1993) that different semimetrics can be used
as an approximate measures of distance. Basing on
the local change of the global criterion Q and maxi-
mization (minimization) of the mentioned distances,
we obtain the substitute local problem, usually a mul-
ticriteria one.
At the third stage, one should determine the manner
of solving the local multicriteria optimisation task.
The basic ideas of multicriteria decision approach
(Dudek-Dyduch, 1990), (Dudek-Dyduch and Fuchs-
Seliger, 1993), (Vincke, 1992), can be applied here.
For learning algorithms, however, the most useful are
these solving manners that assume priority or weight
coefficients for the particular criterions because these
priorities may be modified during consecutive simu-
lation experiments.
A learning algorithm acquires and gathers a knowl-
edge about the process in the following way. Each
new generated trajectory is analysed. If it is not ad-
missible, the reasons of the failure are examined. For
example, it is examined through which subsets of not
advantageous states the trajectory has passed. A role
of the criterions connected with this subsets should be
strengthened for the next trajectory i.e. the weights
(priorities) of these criterions should increase. When
the generated trajectory is admissible, the role of the
criterions responsible for the trajectory quality can
be strengthened, i.e. their weights can be increased.
Basing on the gained information, the local optimisa-
tion task is being improved during simulation exper-
iments. This process is treated as learning or intel-
ligent searching algorithm. The gathered knowledge
is represented by means of coefficients at particular
components of the criterium. This conception has
been examined and is presented in (Dudek-Dyduch,
2000).
If one posses additional expert knowledge then a
better algorithm can be proposed. If some state sub-
sets S
di
, i = 1, 2, . . . are distinguished and for these
states some rules for decision choice R
i
, i = 1, 2, . . .
are given by an expert then algorithm should verify
additionally to which subset the new generated state
belongs and should realise the suitable rule R
i
. If
rules given by expert excludes some decisions then
the suitable sets of possible decision U
p
(s) are de-
creased.
Another idea of learning algorithm for some
ICINCO 2006 - INTELLIGENT CONTROL SYSTEMS AND OPTIMIZATION
162