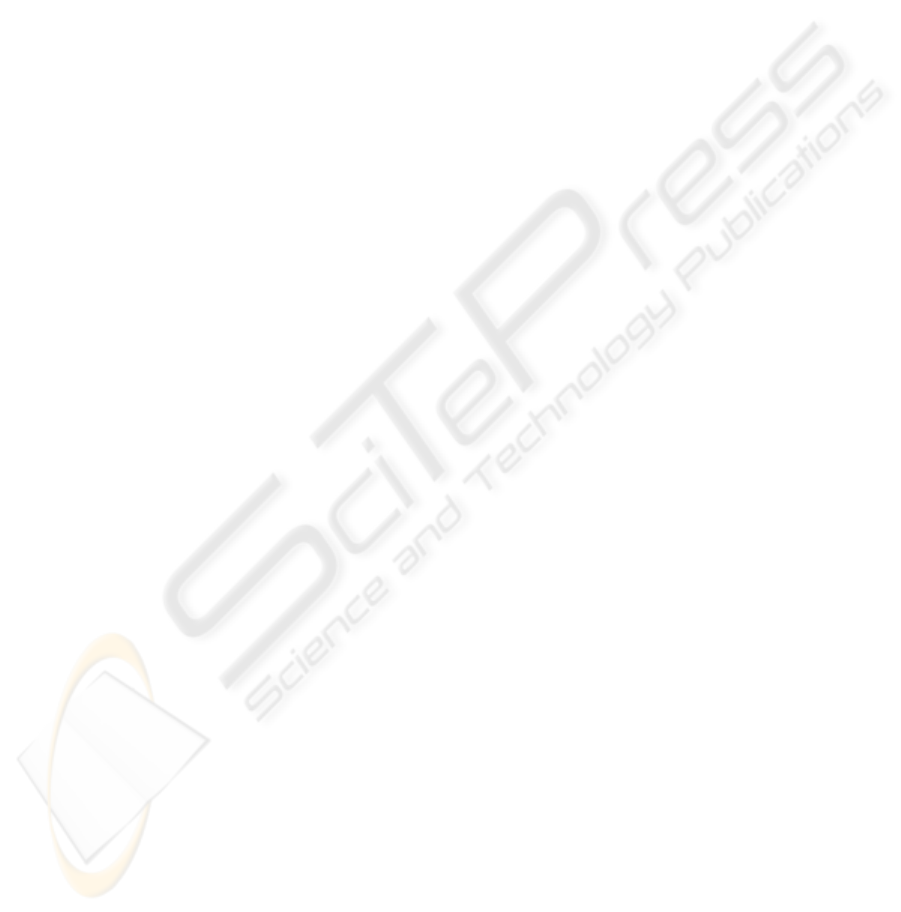
The cluster of SCs implementing the Order
Holon (OH) and Material Handling Holon (MHH)
holonic control layers is interconnected to the
process devices (Robot Controllers) via a SC server
– RC client Switched Ethernet Network, creating a
heterarchical fault-tolerant architecture:
• the failure of a Station Controller is detected by
continuous monitoring via the direct serial links
SC
i
– RC
i
and determines in consequence the
rescheduling of jobs for the (n – 1) remaining
valid Robot Controllers j, 1 ≤ j ≤ n, j ≠ i.;
• if one of the Station Computers is down, its role
is taken over by the remaining (n – 1)
workstations, as each SC data base is replicated
and updated on line in all the other (n – 1) ones;
• if the switch is down, the heterachical
communication between the SC and the RC
clusters still operates via the direct links SC
i
–
RC
i
and the Ring RC link.
The vital inter-operational conditioning between
device tasks (mutual exclusion, synchronization) is
provided by a cross connection I/O network.
4 THE FAULT TOLERANT
COMMUNICATION LEVEL
The communication level represents the key element
of the management systems and command integrated
with robot controllers of FMC.
A critical aspect in designing a communication
level is the building, partitioning and the on-line/off-
line data bases transfer, fact that involve the
multiplication of the communication links insuring
the a global fault tolerant behaviour. So, it must deal
the interoperability on the dynamic aspect, allowing
the modules connected to the communication system
to cooperate between them. The features announced
above belong to a communication level which must
combine the reliability and the performance of an
industrial network with the building simplicity of a
communication system used for parallel applications
executed on multiprocessor machines.
In a normal way, each controller is connected to
the communication network. If in the setup stage of
the manufacturing or during the manufacturing, a
controller is malfunctioning, another controller will
take the tasks. To make this possible we need to
make available the data bases on each controller, and
also a commutation of the informational routes with
the help of the network. The availability is assured
by software redundancy which involve keeping at
least one replica of each data base.
4.1 Network Reconfiguration
Rebuilding the communication route in the network
represent the last step required to restart the normal
behave of the FMC control system.
In case of malfunction of the communication
network the following important cases can appear:
1. if the connection between Switch and the
Supervisor PC is down the remote control will be
lost, but the FMC will reconfigure: the RC will
use the ethernet network for communication, and
the RC with the first IP from the class will take the
functions of the Supervisor PC. If the connexion is
re-established the Supervisor PC makes a query
finds the replacing controller, transfer the
databases and restart the normal behave.
2. if the switch is not functioning, all the Ethernet
connexions are lost, but the controllers will use the
serial “network”. The behave is like in the first
case only that the web users can view the status
from the Supervisor PC, including the images
acquired by the observation cameras.
3. if a controller lose the Ethernet connexion he will
use one of the two serial lines to reach the
Supervisor PC depending on the cpu time of the
neighbours.
5 CONCLUSION
The project is under construction; most of the Server
Application's functions are already implemented and
tested on a pilot platform in the Laboratory of
‘Robotics and AI’ of the University Politehnica of
Bucharest. The research project will provide a portal
solution for linking the existing fault tolerant pilot
platform with multiple V+ industrial robot-vision
controllers from Adept Technology located in
University Labs from various countries. The SA
module is basically finished and successfully tested.
Currently, the eCAs are under construction.
REFERENCES
Hutchinson, S.A., Hager, G.D. and P. Corke, 1996. A
Tutorial on Visual Servo Control, IEEE Trans. on
Robotics and Automation, 12, 5, pp. 1245-1266.
Koestler, A., 1968. The Ghost in the Machine, New York,
Macmillan.
Van Brussel, H., Valckenaers, P., Bongaerts, L. and P.
Peeters, 1998, Reference architecture for holonic
manufacturing systems: PROSA, Computers in
Industry, 37, pp. 255-274.
ICINCO 2006 - ROBOTICS AND AUTOMATION
560