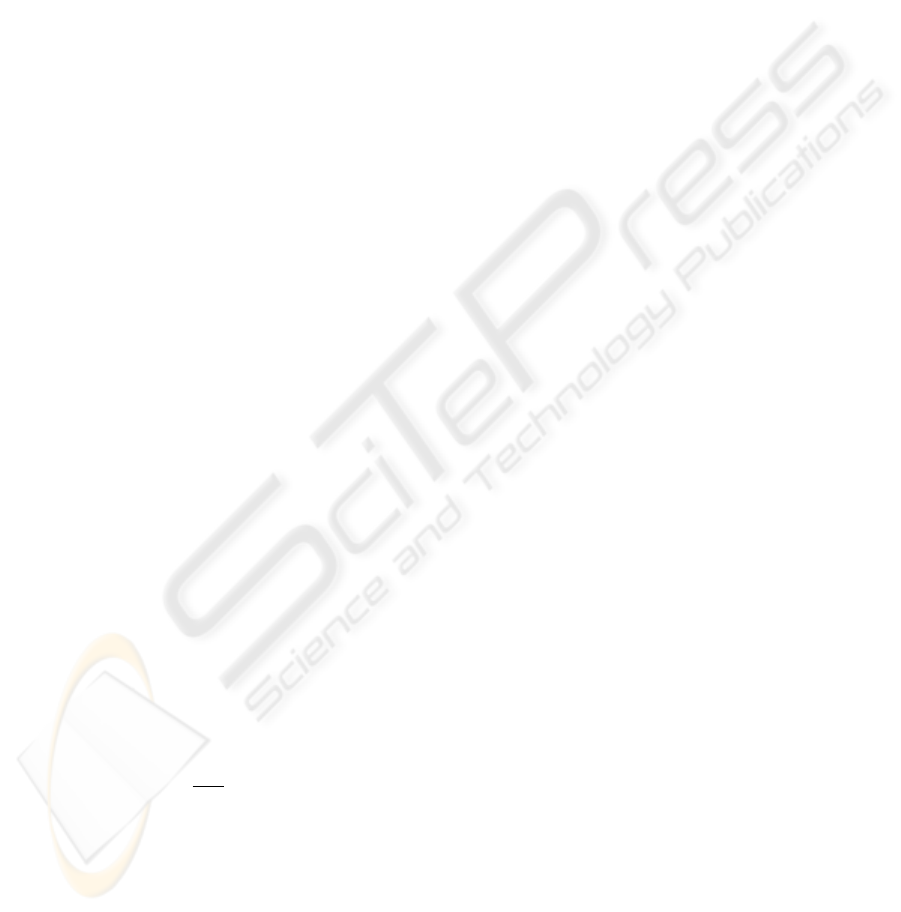
TRAJECTORY CONTROL AND MODELLING OF AN
OMNI-DIRECTIONAL MOBILE ROBOT
Andr
´
e Scolari Conceic¸
˜
ao, A. Paulo Moreira, Paulo J. Costa
Department of Electrical and Computer Engineering
University of Porto - Porto - Portugal.
Keywords:
Trajectory control, modelling and simulation, omni-directional mobile robot.
Abstract:
This paper presents a trajectory controller for an omni-directional mobile robot. The controller presents im-
portant features, as the possibility of defining different translation velocities and angular positions to the robot
during the trajectory following. The parameters of the controller are optimizated based on trajectory following
simulations, with the mobile robot model. Simulation and real results of trajectory following are presented.
1 INTRODUCTION
Omni-directional mobile robots have the ability to
move simultaneously and independently in translation
and rotation (Pin and Killough, 1994). However, non-
linearities, like motor dynamic constraints, and oth-
ers characteristics like friction, inertia moment and
mass of the robot, should be modelled, because can
greatly affect the robot behaviour. Hence, dynamic
modelling of mobile robots is very important to de-
sign of controllers, as in (Liu et al., 2003)(Watanabe,
1998)(Fraga et al., 2005), mainly when the robots
need to follow trajectories at higher velocity, with
sudden change in its direction and orientation.
The suggested controller presents interesting fea-
tures to follows the path correctly, how the possibility
to define different linear velocities and angular posi-
tions to the robot during the trajectory following. A
trajectory can be approximated with line segments. A
line segment has two distinct endpoints. We use in
this paper the name of a line segment with endpoints
A and B as ”line segment
AB”. Hence, we can define
linear velocities and angular position to the robot in
each endpoint of the line segment, moreover we can
adjust its velocities and angular position to the long
of the line segment. Another feature of the controller
is low computational time, which is essential in real
time applications.
The optimization of the parameters of the controller
is based on robot model. Due to values of time and er-
rors of position and orientation of the robot, in trajec-
tory following simulations with the robot model, we
can calculate the best parameters to the controller.
We focus attention on a omni-directional mobile
robot with four motors, as shown in Fig.1, built for
the 5dpo Robotic Soccer team from the Department
of Electrical and Computer Engineering at the Univer-
sity of Porto at Porto, Portugal(Moreira et al., 1999).
The organization of the paper is as follows. In sec-
tion 2, the omni-directional mobile robot model is de-
veloped. The controller for trajectory following is
presented in section 3. In section 4, the optimiza-
tion of the controller parameters, simulation results
and real results are presented. Finally, the conclusion
is drawn in section 5.
2 THE MOBILE ROBOT MODEL
The omni-directional mobile robot model is develo-
ped based on the dynamics, kinematics and DC mo-
tors of the robot.
The World frame (X, Y, θ), the robot’s body frame
and the geometric parameters is shown in Fig. 2.
The following symbols, in SI unit system, are used
to modelling:
• b [m] → distance between the point P(center of
chassis) and robot’s wheels
• M [kg] → robot mass
• r [m] → wheel radius
• l → motor reduction
• J [kg.m
2
] → robot inertia moment
412
Conceição A., Moreira A. and Costa P. (2006).
TRAJECTORY CONTROL AND MODELLING OF AN OMNI-DIRECTIONAL MOBILE ROBOT.
In Proceedings of the Third International Conference on Informatics in Control, Automation and Robotics, pages 412-417
DOI: 10.5220/0001220904120417
Copyright
c
SciTePress