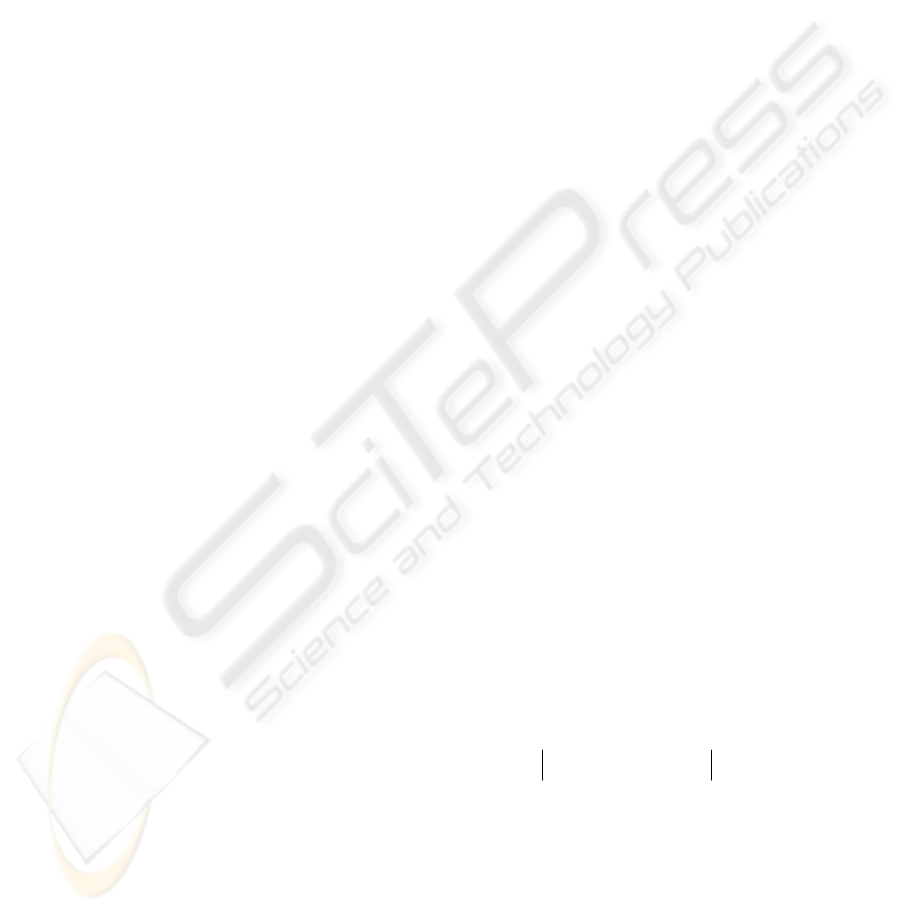
to the waste vessel (calibration phase) or to water
under test (measurement session), and the MP
(measuring pump) that is a submersible pump (1
submersible 12 VDC, 2.5A, 49 l/min Johnson pump)
and used to assure the circulation of the water
between the monitored area (river, estuary) and the
test cuvette
.
3 SYSTEM SOFTWARE
The system software includes two parts, one related
with
the smart calibration and measurement system based
on cRIO real-time controller and FPGA
reconfigurable module and another represented by
the software of the PDA Pocket PC.
The FPGA reconfigurable module software was
developed using LabVIEW for FPGA toolset and is
associated with the pump and electrovalves control
through digital output lines, the level on/off sensor
reading, the acquisition of the water quality sensors
voltage values when the system works in the
measurement mode and the sensor under test voltage
acquisition when the system works in calibration
mode. Using the FPGA onboard memory and the
memory read/write functions the FPGA embedded
algorithms for digital-code voltage to water quality
parameter (e.g. temperature) is carried out.
Taking into account the limitation of the FPGA
related the numerical values calculation (only
integers operation) the main part of processing of the
acquired data is developed on the real-time
controller level using the LabVIEW real-time. Thus
a multichannel voltage-to-WQ conversion block was
implemented. Taking into account temperature
variation influence on the measurement channel
accuracy, the temperature compensation based on
IEEE1451.2 correction engine algorithm was also
implemented.
Data logging software block was implemented on
the cRIO controller in order to store the information
about measured water samples.
Regarding data distribution in the water quality
network that includes the PDA and other PCs
(laptop or desktop PC) the cRIO real-time controller
includes a TCP server-multiple client component.
Implementing client software on the PDA level
using (LabVIEW for PDA) the PDA operator can
obtain the current values of the Water Quality
parameters and the calibration coefficients of the
water quality measurement channels. Calibration
and measurement start-up actions or measurement
channel tests when anomalous functioning is
reported (fault events) can be ordered using the PDA
software component.
3.1 Embedded FPGA Software
The embedded FPGA software is developed using
the LabVIEW FPGA toolset and is associated with:
electro-valves and centrifugal pumps control, WQ
sensor calibration, water quality measurement, fault
or pollution event detection multi-channel analog-
input and digital input control, digital filtering of
the acquired samples from the WQ measuring
channels associated with NI cRIO-9215 module.
For the particular case of WQ sensor calibration the
flowchart of the calibration session is presented in
Figure 2.
Referring the measuring mode an additional
submersible pump is used to bring the water under
test into the test cuvette and the voltages obtained on
the sensor channels are acquired. The water under
test level on the testing cuvettte is imposed constant
thus a simple on/off control of the WP and M_VEW
is implemented on the system while the level
information is obtained from the LS sensor.
When the system works in the measuring mode and
a strong variation of WQ parameter from one of the
measuring channel is detected (using the derivative
information) the pollution event detection mode is
start-up. In order to make an accurate discrimination
between the pollution and measuring channel
anomalous functioning a “one point test procedure”
is designed and implemented.
The action associated with this procedure is similar
to the calibration of the considered measuring
channel for one standard solution.
A comparison between the current acquired voltage
)(tU
CS
WQ
from the tested channel and reference
voltage value
)(
ref
CS
WQ
tU considered for the same
calibration solution (CS) is carried out.
The fault detection is expressed by the following
relation:
faultWQrefWQWQ
tUtU
ξ
≤− )()( (1)
Thus if the difference between the considered values
is greater than an imposed limit
faultWQ
(5% of
)(
ref
CS
WQ
tU in the present case) the anomalous
functioning message is delivered in the WQ
monitoring network. In opposite case the pollution
event signal is generated.
In order to increase the SNR (signal to noise ratio)
the acquired samples from the WQ measuring
channels are filtered using a FPGA embedded
ICINCO 2006 - SIGNAL PROCESSING, SYSTEMS MODELING AND CONTROL
156