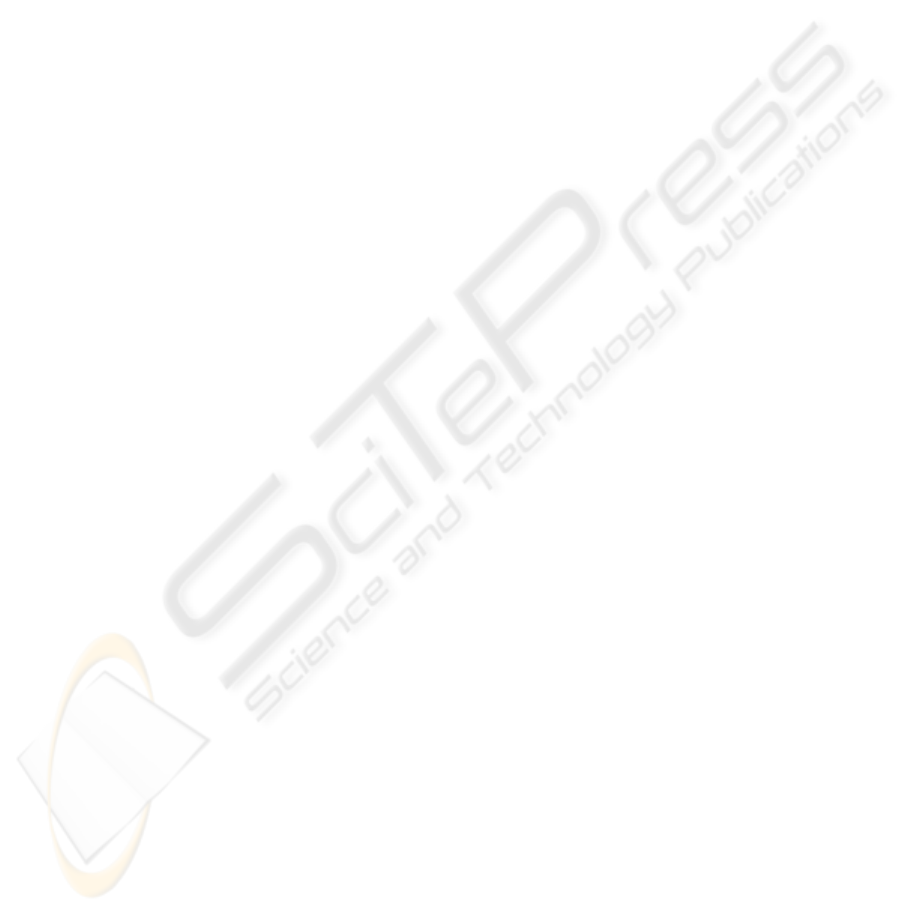
as previously commented. This HMI was tested as much in a mobile robot as in a robotic
manipulator. In both cases, the command was executed by the robotic devices.
Such works are initial parts of a system to help people with neuromotor diseases,
including those with severe dysfunctions. The next steps are: to convert a commer-
cial wheelchair in an autonomous mobile vehicle; to implement the HMI onboard such
autonomous wheelchair to assist people with motor diseases; to explore more charac-
teristics of EEG signals, making the Brain Computer Interface (BCI) more robust and
faster, allowing a secure use by people with severe motor dysfunctions.
Acknowledgements
The authors thank CAPES (Brazil) and SPU (Argentina) for their financial support
to the partnership between Federal University of Espirito Santo, Vitoria, Brazil, and
National University of San Juan, San Juan, Argentina, through the binational program
CAPG-BA. As part of this financial support, Andre Ferreira got a scholarship to stay six
months in San Juan, Argentina, where part of this work was developed. The authors also
thank FAPES/Brazil (Process 30897440/2005) for its financial support to this research.
References
1. Ferreira, A., Bastos-Filho, T. F., Sarcinelli-Filho, M., Cheein, F. A., Postigo, J. F., Carelli, R.:
Teleoperation of an Industrial Manipulator Through a TCP/IP Channel Using EEG Signals.
In: ISIE2006, Montreal, Canada, July, 2006.
2. Cheein, F. A., Postigo, J. F.: A fast finite state machine design for a brain computer interface.
In: Proceedings of XI RPIC, Rio Cuarto, Argentina, 2005.
3. Cheein, F. A.: Dise
˜
no de una Interfaz Cerebro-Computadora para la navegaci
´
on de un Robot
M
´
ovil. In: Master Thesis, San Juan, Argentina, August, 2005.
4. Neto, A. F., Celeste, W. C., Martins, V. R., Bastos-Filho, T. F., Sarcinelli-Filho, M.: Human-
Machine Interface Based on Electro-Biological Signals for Mobile Vehicles. In: ISIE2006,
Montreal, Canada, July, 2006.
5. Mill
´
an, J., Renkens, F., Mouri
˜
no, J., Gerstner, W.: Non-invasive brain-actuated control of a
mobile robot. In: Proceedings of the 18th International Joint Conference on Artificial Intelli-
gence, August, 2003.
6. Mouri
˜
no, J. E.: EEG-based analysis for the design of adaptive brain interfaces. In: Ph.D. The-
sis, Barcelona, Spain, 2003.
125