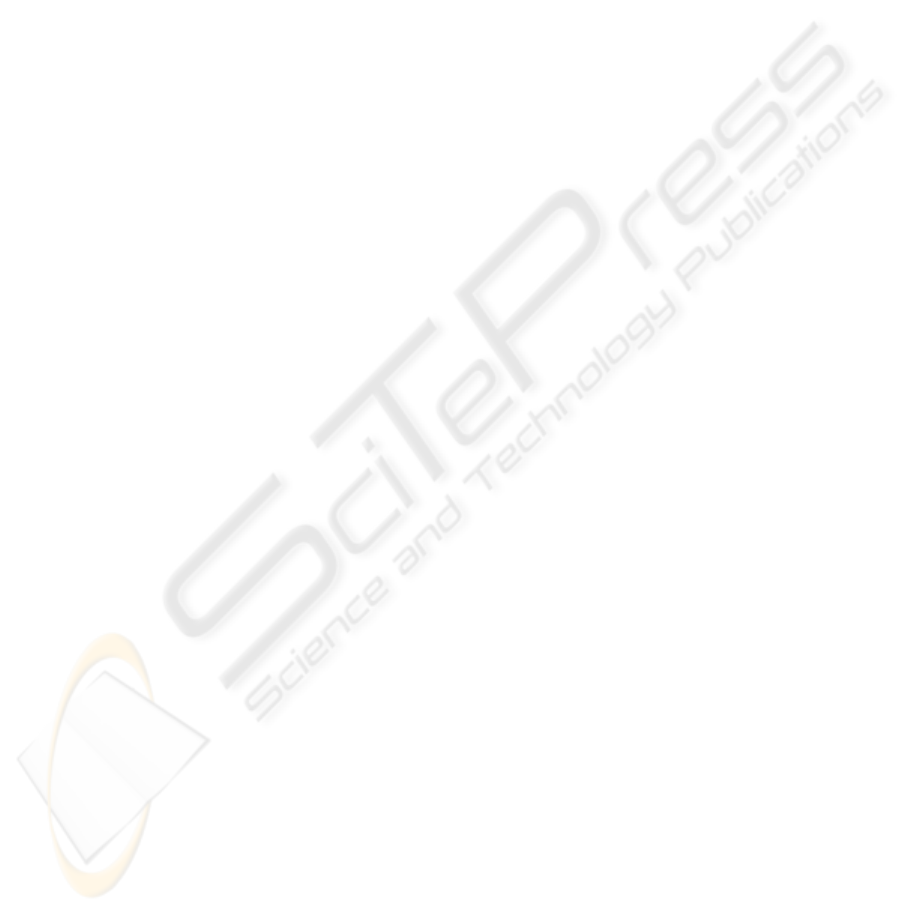
been examined in the context of patch pasting. In
the context of cylindrical pasting these implementa-
tions are expected to suffer from high evaluation costs
and/or significant algorithmic complexities. Our work
focuses upon determining a cylindrical pasting tech-
nique that is computationally inexpensive, simple to
implement, and that consistently gives the best com-
parative approximation of boundary continuity (i.e.,
C
0
continuity) between a pasted feature cylinder and
its underlying base surface. In a more general sense,
our work attempts to find a low-cost method of using
a given closed B-spline curve to approximate a dif-
ferent given closed curve, with minimal reproduction
error.
2 PASTING BASICS
We begin with an overview of surface pasting theory
since it forms the foundation for the work done in this
paper. Surface pasting combines a base surface and a
feature surface, each of which is in tensor product B-
spline form and defined over its own two-dimensional
domain. The basic idea is to adjust the feature’s con-
trol points in a manner that results in the boundary of
the pasted feature lying on or near the base surface,
while simultaneously ensuring that the shape of the
pasted feature reflects characteristics of both its orig-
inal form as well as of its base. To achieve this, the
pasting process involves the following steps:
1. The feature’s domain is embedded into its range
space. Tensor product construction ensures that
each feature control point P
i,j
has an associated
domain point at which it maximally influences the
feature surface. This domain point is referred to
as the Greville point (γ
i
,γ
j
)=γ
i,j
, where γ
i
is
the i
th
Greville abscissa in the u parametric di-
rection and γ
j
is the j
th
Greville abscissa in the
v direction. Taking the embedded Greville point
(γ
i,j
, 0) = Γ
i,j
in feature range space as a point of
origin, and using the feature’s corresponding para-
metric domain directions to define a set of basis
vectors, a local coordinate frame associated with
each P
i,j
is constructed. Now, each feature control
point can be expressed relative its local coordinate
frame in terms of a displacement from its origin
called the Greville displacement
d
i,j
.
2. The feature domain is mapped into the base domain
using an invertible transformation T . T determines
the relative size and placement of the feature sur-
face with respect to its base.
3. A base domain displacement representation of each
feature control point is created by expressing each
displacement
d
i,j
in terms of a local base coordi-
nate frame.
4. The feature control points are positioned relative
to the base surface using the local base coordinate
frame and the mapped displacement vector recom-
puted relative to this frame.
Note that surface pasting is only an approximation
technique. Rather than mapping every point of the
feature surface, it maps a small number of sample
sites, the feature Greville points. If the feature sur-
face is described by too few control points or a coarse
knot structure relative to its base, noticeable gaps at
the join boundary may appear in the composite sur-
face. In general, there is no guaranteed continuity be-
tween feature and base surfaces.
In the case of standard surface pasting, C
0
continu-
ity is approximated by defining the embedded feature
domain such that all boundary control points of the
feature coincide with their respective Greville points.
This ensures that the feature’s boundary control points
lie in the feature’s domain plane and that upon being
pasted they will lie directly on the base surface. Pro-
vided the base has low curvature relative to the spac-
ing between these points, a near C
0
join is achieved.
For further details on standard surface pasting, refer
to earlier works on the subject (Bartels and Forsey,
1991; Barghiel et al., 1995).
Cylindrical surface pasting integrates concepts
from parametric trimline-based blending to extend
surface pasting to handle a wider variety of modeling
situations. While standard pasting was designed only
to handle the pasting of one open surface atop another,
cylindrical pasting offers a method for connecting two
base surfaces smoothly using a tensor product cylin-
der as the feature surface. In this paper, we are only
concerned with pasting one end of a cylinder onto a
base tensor product surface.
To paste one end of a cylindrical feature onto
its base surface, the corresponding edge of the fea-
ture domain is mapped onto a paste curve in the
base domain. Determining the placement of con-
trol points such that the pasted cylinder’s boundary
closely matches the image of a user-defined paste
curve on the base surface is our challenge. The orig-
inal cylindrical pasting technique directly applied the
C
0
continuity approximation of standard surface past-
ing to the C
0
layer of a feature cylinder, i.e., each
boundary control point was located at its correspond-
ing Greville point. However, while zero displacement
control points reproduce the linear boundary of a ten-
sor product patch, placing the control points on the
closed curve boundary of a tensor product cylinder
does not reproduce its boundary (Figure 1). Our work
explores alternate methods that have the potential of
producing better C
0
continuity between the pasted
cylinder and its underlying base. To maintain the
prototyping nature of pasting, the methods we have
designed have low computational costs, with a paste
not costing much more than one base surface evalua-
A COMPARISON OF CYLINDRICAL PASTING METHODS
109