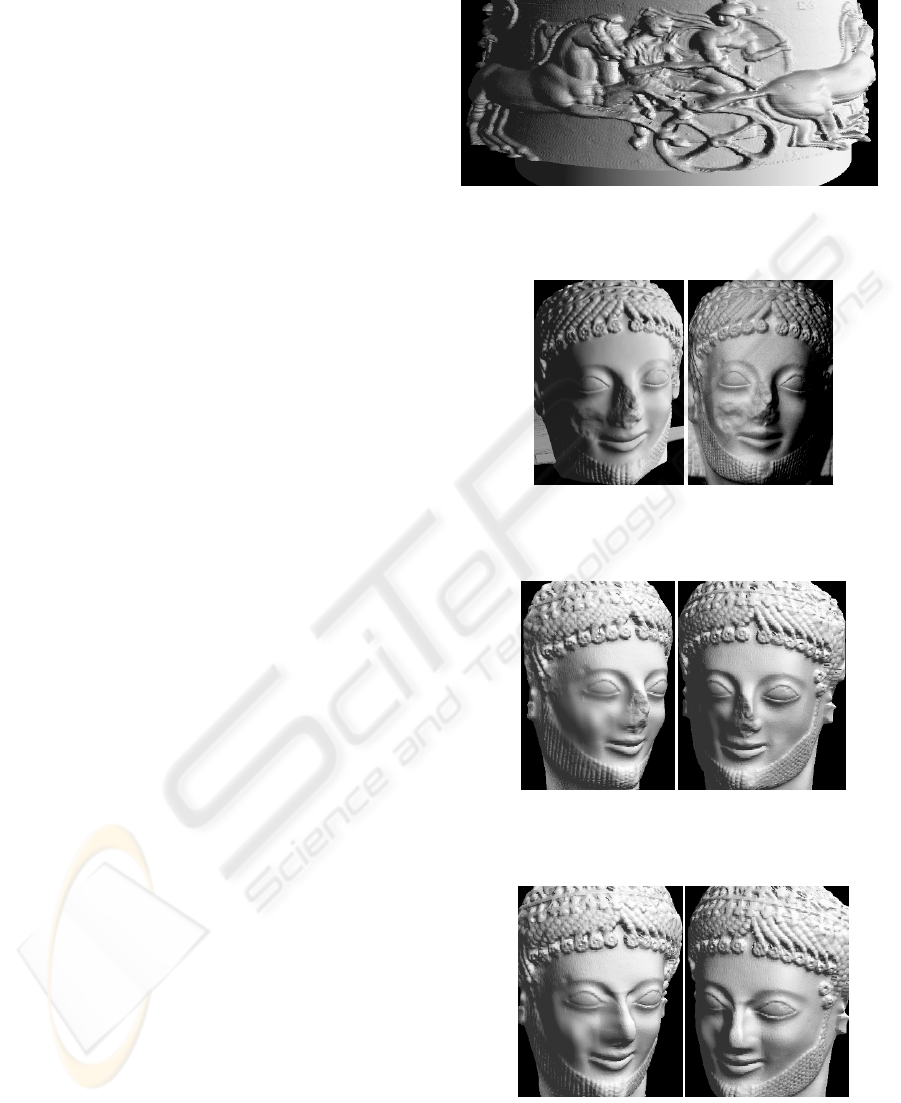
The modeling accuracy depends on the rotational
and translational positioning, and distance-sensing.
The mal-aligned positioning results in a shape distor-
tion, but still generates topologically stable models.
4 CONCLUSIONS
Some precise 3D models, within 0.01 mm 3D
resolutions, are demonstrated based on the topology-
assigned modeling procedure. The simple,
automatic, geometrically accurate and precise,
topologically stable, robust and noise-resistive object
modeling, with matrix-format meshes, for
archeological and cultural heritage applications. The
noise problem inherent in the triangulation scanning,
fatal in the so-called “retrieve topology from geometry”
algorithm, is solved using the matrix format operators
for practical usage in the exchange for some spatial
resolution reduction. We expect considerable utility
in the practical approximation and 3D shape
processing.
REFERENCES
Blais, F., 2004, Review of 20 Years of Range Sensor
Development, Journal of Electronic Imaging, 13 (1),
231-240.
Dey, T., Goswami, S., 2004, Provable Surface Reconstruc-
tion from Noisy Samples, Annual Symposium on
Computational Geometry, In Proceedings of 20th Annual
Symposium on Computational Geometry, 330-339.
Godin, G., Beraldin, J., Taylor, J., Cournoyer, L., El-
Hakim, S., Baribeau, R., Blais, F., Boulanger, P.,
Domey, J., Picard, M., 2002, Active Optical 3D
Imaging for Heritage Applications IEEE Computer
Graphics and Applications, 22, 24-36.
Levoy, M., Pulli, K., Curless, B., Rusinkiewicz, S., Koller,
D., Pereira, L., Ginzton, M., Anderson, S., Davis, J.,
Ginsberg, J., Shade, J., Fulk, D., 2000, The Digital
Michelangelo Project; 3D Scanning of Large Statues,
In Proceedings of Siggraph 2000, 131-144.
Rusinkiewicz, S., Levoy, M., 2001, Efficient Variants of
the ICP Algorithm, In Proceedings of the 3rd
International Conference on 3-D Digital Imaging and
Modeling (3DIM ’01), 145-152.
Scott, W., Roth, G., Rivest, J., 2003, View Planning for
Automated Three-Dimensional Object Reconstruction
and Inspection, ACM Computing Surveys, 35(1), 64-
96.
Simple3D, 2005, 3D Scanners, Digitizers, and Software
for Making 3D Models and 3D Measurements,
http://www. simple3d.com/
Pauly, M., Keiser, R., Kobbelt, L., Gross, M., 2003, Shape
Modeling with Point-Sampled Geometry, ACM
Transactions on Graphics (TOG), 22 (3), Special
issue: Proceedings of ACM SIGGRAPH, 641-650.
Figure 7: The modeled frieze replica in Fig. 7 is trans-
cribed onto a cylinder on the supposition of a vase design.
The left part of this figure corresponds with that of Fig. 6.
Figure 8: A photograph (left) and the shaded image of the
modeled result (right) of a plaster statue (Greek cavalier
Rampin). Resolutions are similar to those in Fig. 5.
Figure 9: The cheek bruise in the model in Fig. 8 is
restored using similar operators in Fig. 2 (left). The plump
(left) and the sunken cheeks (right) are depicted.
Figure 10: The cheek bruise and the broken nose are
restored. The nose is restored by implanting another nose in a
Greek mask and then shape modified using a depth-to-depth
trans-formation operator in Fig. 2 (left). As the data structure
is matrix-format, detailed procedures are not shown here.
GRAPP 2006 - COMPUTER GRAPHICS THEORY AND APPLICATIONS
334