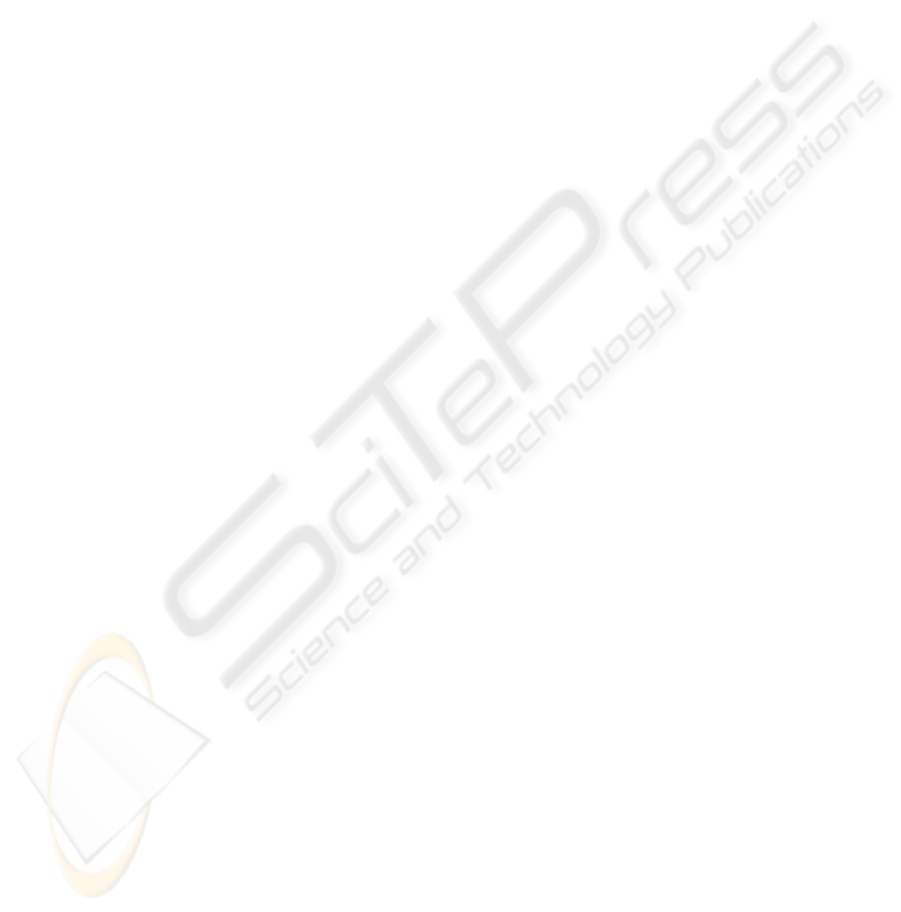
lengths along the scanning direction, only a single
sample from the centre may be considered for this
sampling.
Any major deviation from the average edge starting
and ending positions around the defect region is
considered as a side defect (edge chip) with its side
location information. The maximum value across the
defect-sampling of any such deviation provides the
across size of a side defect. Also, any additional
threshold crossings inside the edge identify an inside
defect (shiner). The size is measured as the
maximum separation between the beginning-
crossing and the ending-crossing across the defect-
sampling.
Parameter Selection for the Application Domain
The following is a discussion of a reasonable set of
guidelines for the selection of some algorithm
parameters:
Scaling Factor
The signal may be pre-processed with a scaling and
clipping before the detection stage is performed. For
the present application domain, from the
experimental data, it is observed that that a fixed
scaling can be used throughout the detection stage.
However, with varying camera/edge distance and
dynamic illumination power control, an adaptive
procedure may also be adopted.
Gaussian Functions
The number of the Gaussian functions used in the
approximation determine how well the edge signal is
approximated. Therefore, a larger number means a
better approximation. However, the increasing
number increases the computational complexity of
the approximation and decreases the smoothing
effect, resulting to also model the noise. This is
clearly not desirable. Therefore, the choice should be
as small as possible as long as a distance between
the static and adaptive models has a significant
enough peak in a defect region to allow detection.
M=3 or M=5 Gaussian functions whose centers are
distributed along the edge is observed to provide
good results. We have preferred an odd number of
Gaussian functions due to the symmetry of the
signal and in order to have maximum sensitivity in
the center of the image strip.
The Gaussian means are determined to provide a
uniform distribution along the edge. For the M=3
case, one mean can be placed in the center of the
edge and remaining two on the estimated edges.
Small, gradual changes on the edge will not have a
serious impact on the approximation.
The variances of the Gaussian functions are all the
same and determined by the choice of their number
and mean values. More specifically, the distance
between two adjacent Gaussian functions determines
this choice. The main criteria is to obtain a smooth
enough approximation. A variance value of
σ
= 2.5d
where d is the distance between adjacent Gaussian
functions gives an acceptable smoothness. This
value is used for the approximations in Figure 1.
Adaptive Model Adaptation Rate
This value determines how fast the adaptive model
will follow the changes in the edge signal. Too small
a value will render the adaptive model fixed, which
will not be able to track a gradual change in the edge
signal. Too large a value will cause the adaptive
model to follow the changes in the edge signal very
closely and the model distance signal will always
remain small making detection very difficult if not
impossible. For a reasonably steady edge signal,
values in the range 0.0005 to 0.005 are found to be
reasonable choices for this application.
Detection Threshold
This threshold determines the sensitivity of detecting
a defect and also affects the size measurement of the
defect along the strip direction. As the threshold
increases, only larger disturbances on the edge will
trigger a detection. On the experimental samples
considered for this application domain, a threshold
value of 10 to 20 were appropriate choices. The
parameter range can be tuned by experimentation
with the application domain. This parameter is
considered to be the only user controllable parameter
to adjust the sensitivity of the overall system so as to
eliminate the detection of very small defects.
4 EXPERIMENTAL RESULTS
For the experiments, we consider the application
domain of grinded glass edge inspection. The edge is
illuminated with coherent light at an oblique angle.
The properly grinded edge is a scattering surface and
back scatters enough light to generate a light signal.
The grinding problems and missing parts on the
edge can be visually observed to be present in the
signal. Figure 4 illustrates the two aforementioned
defect types on the grinded glass edge. Figure 5
SCAN-LINE QUALITY INSPECTION OF STRIP MATERIALS USING 1-D RADIAL BASIS FUNCTION NETWORK
23