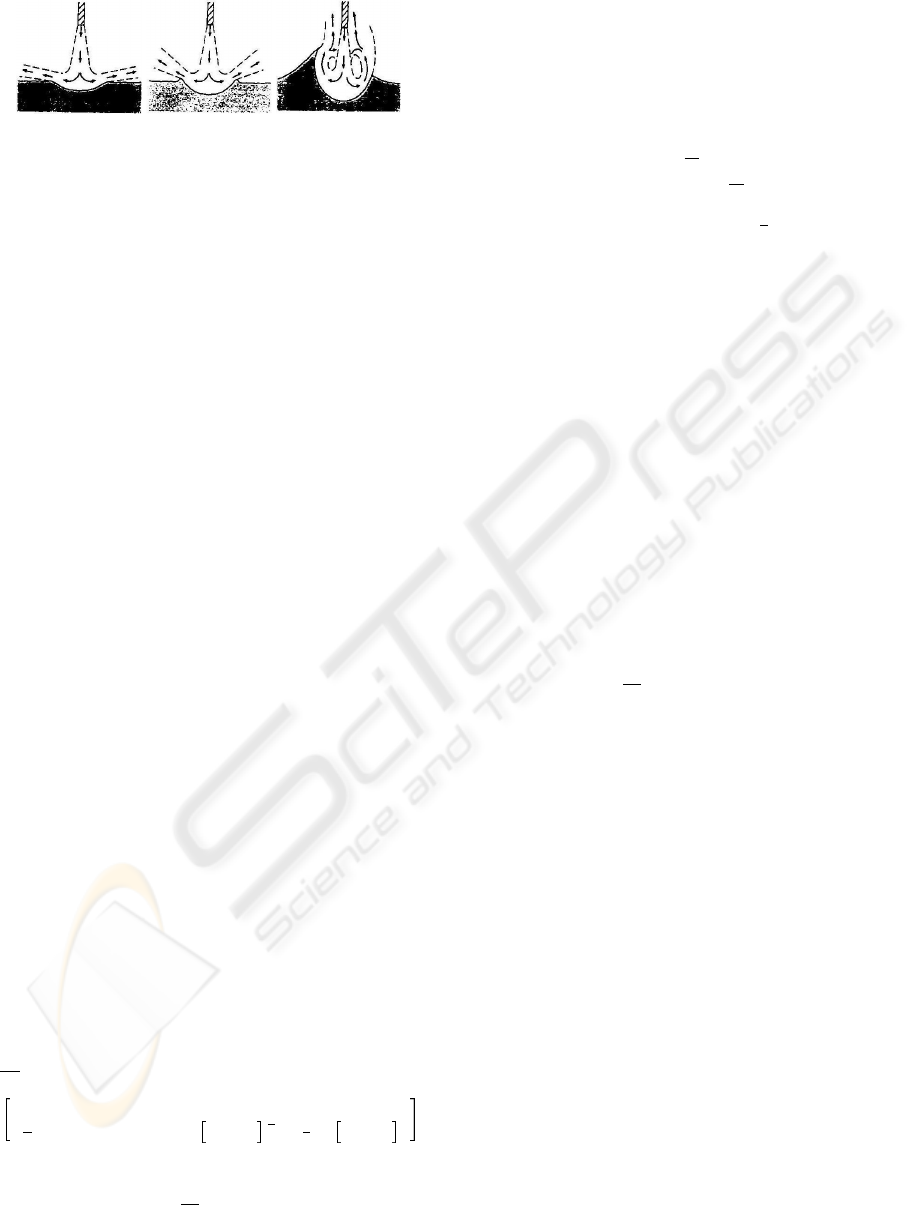
(a) (b) (c)
Figure 2: Modes of surface deformation by the imping-
ing gas jet according to (Molloy, 1970). (a) Dimpling, (b)
Splashing, (c) Penetrating.
water model the molten steel is replaced by water and
compressed air is used instead of oxygen. The sim-
ilarities between the water bath and the molten steel
are analyzed in (Lee et al., 2002).
Energy and force balances were considered in
(Rosler and Stewart, 1968), to describe the indenta-
tion profile. The results were later used in (Bergh-
mans, 1972), for a study of the stability of interfaces
between fluids in motion.
In (Evestedt and Medvedev, 2005) the cavity sur-
face model in (Berghmans, 1972) was used, together
with experimental data from a water model, to ap-
proximate the surface deformation and to quantify the
uncertainty of the depth and diameter estimates. The
uncertainty was shown to decrease when the tempo-
ral dynamics of the cavity were modelled as a sum of
sine waves.
In this paper a sampling algorithm to improve the
efficiency of the estimation procedure in (Evestedt
and Medvedev, 2005) is given. The paper is orga-
nized as follows: First a system model is introduced.
Then three approaches to choosing sampling points
for the optimization are presented, followed by a de-
scription of the experimental setup. The paper is con-
cluded with a comparison between the methods using
both simulated and experimental data.
2 PROBLEM FORMULATION
In (Berghmans, 1972) a mathematical model for the
gas-jet system was suggested. The model was in-
vestigated further in (Evestedt and Medvedev, 2005),
where it was reformulated in state-space form as
dx
dr
= f(r, x)= (1)
x
2
1
σ
(∆p +(ρ
1
− ρ
2
)gx
1
) 1+x
2
2
3
2
−
δ
r
x
2
1+x
2
2
x =[x
1
x
2
]
T
where x
1
= h, x
2
=
dh
dr
, g is the gravitational con-
stant, ∆p is the over-pressure due to the impinging
jet, δ =1, ρ
1
and ρ
2
are the densities of the liquid and
the gas, respectively and σ is the surface tension of
the specific liquid-gas combination.
To determine ∆p, Rosler and Stewart used the ex-
perimental data of Gibson, for laminar jets impinging
on a flat plate, (Gibson, 1934). The pressure distribu-
tion is approximated by:
∆p =
p
max
cos(0.826
r
r
j
) for r ≤ 1.2r
j
4.53p
max
exp(−1.76
r
r
j
) for r>1.2r
j
where r
j
is the jet radius, p
max
=
1
2
ρ
1
V
2
j
is the jet
strength and V
j
is the maximum jet velocity. In the
following, δ, σ and x
1
(0) are treated as tuning para-
meters.
The problem treated in this paper is then to estimate
the parameters θ =[δ, σ, x
1
(0)] in (1) from a video
sequence showing the liquid formation on the surface
of a water tank.
The cavity edge is extracted from the image frames.
Each point on the edge is assigned a coordinate (i, j)
describing its position in the image. A conversion
from the image coordinates (i, j) to actual coordi-
nates (h(r),r) is performed via image calibration.
Define a set of coordinates as M ∈ R
2
, and N as the
number of pixels in the set (cardinal number of M ).
In (Evestedt and Medvedev, 2005), the following cri-
terion function is used to estimate the parameters in
(1) by optimization.
ˆ
θ = arg min
θ
L(θ) (2)
L(θ)=
1
N
r∈M
(h(r) −
ˆ
h(r))
2
where
ˆ
h(r) is the model output.
The optimization is performed over the set M , us-
ing fminsearch in Matlab
c
. In the following, the
approach in (Evestedt and Medvedev, 2005), where
all data points, obtained by edge detection, belong to
M, will be referred to as Scheme 1.
The underlying algorithm for the multidimensional
unconstrained nonlinear minimization is the Nelder-
Mead search, (Nelder and Mead, 1965). It is based on
evaluating a function at the vertices of a simplex or
hypertetrahedron, then iteratively shrinking the sim-
plex as better points are found until some desired
bound is achieved. Due to the lack of convergence
results, the efficiency and complexity of the Nelder-
Mead search algorithm are hard to estimate, (Singer
and Singer, 2004). In this particular application, the
time needed for the algorithm to converge is depen-
dent on the number and placement of the data used in
the parameter tuning.
The contribution of this paper is two model-based
approaches to choose the sampling points used in the
optimization in such a way that the computation time
is substantially decreased, with acceptable reduction
of the estimation accuracy.
VISAPP 2006 - IMAGE ANALYSIS
366