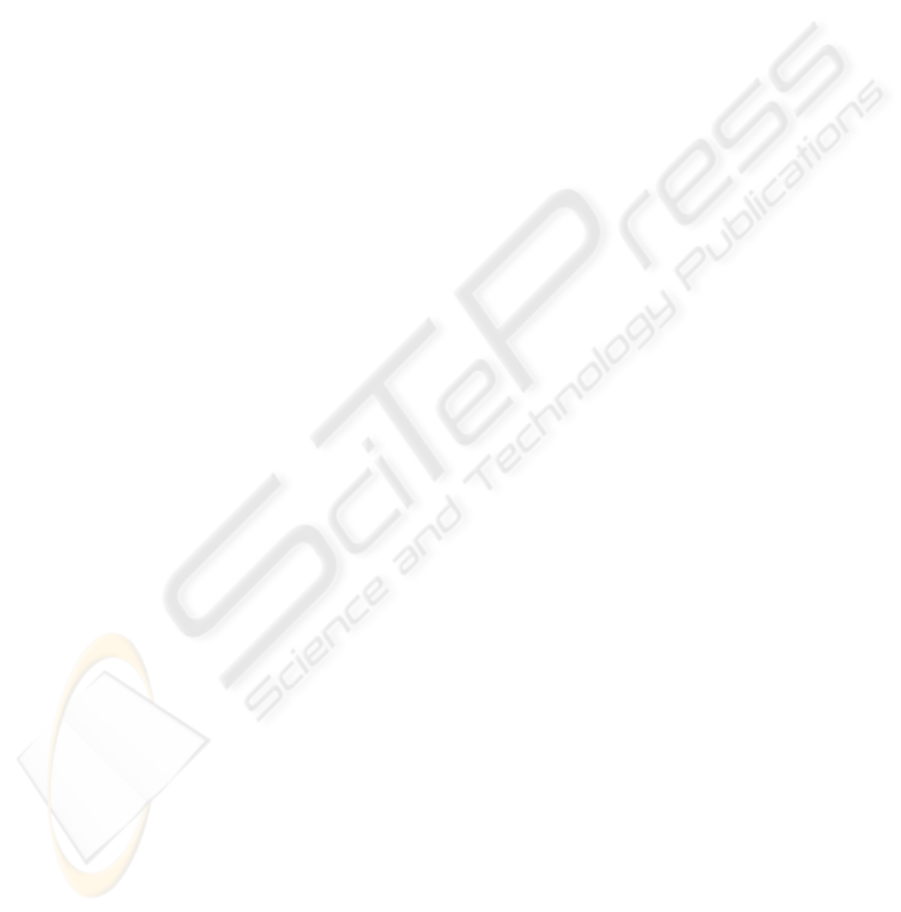
vironmental auditor); external clients (e.g. partners
interested in purchasing products with low environ-
mental impact) or for government authorities (eg. for
governance purposes). LCI service provides details of
measured and estimated energy and wastes and emis-
sions from processes in making products (on product
by product basis). The Green Purchasing Service in-
terface requires the web method, get-supplier-impact-
data to be implemented by the Supplier Registry to get
the impact rating for an item. The Green Purchasing
Service interface requires another web method, get-
green-material to be implemented by the Supplier ser-
vice. The above illustration can be seen to correspond
to the current day requirements of voluntary reporting
and greening supply chains. Life cycle impact analy-
sis and various reporting requirements may need to be
split into subprocesses. The ensuing tangling of be-
haviours will be dealt with using a model-driven ap-
proach to aspect-oriented design in a service-oriented
architectural context (Chavez et al., 2005).
5 SUMMARY AND CONCLUSION
Materials production and manufacturing are highly
important for the economic and social wellbeing of
modern society, but such activities are inherently en-
vironmentally burdensome. The concept of servicis-
ing a manufacturing business has been propounded by
experts in the field of industrial ecology and adopted
by some companies to improve their environmental
performance. Information industry has already pro-
gressed well along the service-oriented path, driven
by the advancements in web-based technologies. Tak-
ing cognizance of these developments in two differ-
ent industry areas, we have offered some conceptual
thoughts for modelling the delivery of environmental
information to sustainable manufacturing businesses
and for synthesis into service-oriented software.
We have shown the links between the business
functions of a manufacturing enterprise and the envi-
ronmental requirements relevant to the business. We
have identified the core environmental tasks to be per-
formed by a sustainable manufacturing company. We
have derived a software service model at the manu-
facturing plant level for estimating the life cycle bur-
dens of a manufactured product by a company in part-
nership with other companies in the life cycle chain
of the product. Taking diecast automotive compo-
nents as a case study, we are currently following the
model-development approach for developing service-
oriented environmental software in implementation,
testing and validation. We believe the proposed ap-
proach could form the basis for developing future
software e-business to meet evolutionary sustainabil-
ity requirements faced by manufacturing companies.
REFERENCES
Benatallah, B., Casati, F., Skogsrud, H., and Toumani, F.
(2004). Abstracting and Enforcing Web Service Pro-
tocols. International Journal of Cooperative Informa-
tion Systems, 13(4):413–440.
Burritt, R. L. (2004). Environmental Management Ac-
counting: Roadblocks on the way to Green and Pleas-
ant Land. Business Strategy and the Environment,
13(1):13–32.
Cardoso, J., Sheth, A., Miller, J. A., Arnold, J., and Kochut,
K. (2004). Quality of Service for Workflows and Web
Service Processes. Journal of Web Semantics,Elsevier
Publications, 1(3):281–308.
Carlson, R., Erixon, M., Forsberg, P., and Palsson, A. C.
(2001). System for integrated business environmental
information management. Advances in Environmental
Research, Elsevier Science, 5:369–375.
Chavez, C. F. G., Garcia, A., Kulesza, U., and andC J P Lu-
cena, C. S. (2005). Taming Heterogeneous Aspects
with Crosscutting Interfaces. In 19th Brazilian Sym-
posium on Software Engineering.
Dijkman, R. and Dumas, M. (2004). Service-oriented
Design: A Multi-Viewpoint Approach. Interna-
tional Journal of Cooperative Information Systems,
13(4):337–368.
Elkington, J. (1997). Cannibals with forks: the triple bot-
tom line of 21st century business. Capstone Publishing
Ltd, Oxford.
Graedel, T. E. and Allenby, B. R. (1995). Industrial Ecol-
ogy. Prentice-Hall: Englewood Cliffs, NJ.
Isenmann, R., Beisel, M., Brosowski, J., and Gomez, J. M.
(2004). Software tool for single source multiple me-
dia and multiple requirement sustainability reporting.
In 18th International Conference Informatics for En-
vironmental Protection, EnviroInfo2004.
Koehler, J., Hauser, R., Kapoor, S., Wu, F. Y., and Kumaran,
S. (2003). A Model-Driven Transformation Method.
In Proceedings of 7th International Enterprise Dis-
tributed Object Computing Conference (EDOC 2003),
pages 186–197. IEEE Computer Society 2003.
Milanovic, N. and Malek, M. (2005). Contract-based
Web Service Composition Framework with Correct-
ness Guarantees. In 2nd International Service Avail-
ability Symposium (ISAS2005).
Ramakrishnan, R. (2003). An industrial ecology frame-
work to assist transferring environmental technolo-
gies. In Technology Evaluation and Commercializa-
tion, TEPC 2003-2, University of the Pacific, Califor-
nia, USA, pages 323–368.
Ramakrishnan, R., Tharumarajah, A., Koltun, P., and
Roberts, M. J. (2003). Eco-Efficient Light-Metals
Component Manufacturing. In Light Metals Tech-
nology Conference (LMT 2003), Brisbane, Australia,
pages 281–286.
Schaltegger, S., Burritt, R., and Peter, H. (2003). An In-
troduction to Corporate Environmental Management.
Striving for Sustainability. Sheffield: Greenleaf.
ICE-B 2006 - INTERNATIONAL CONFERENCE ON E-BUSINESS
82