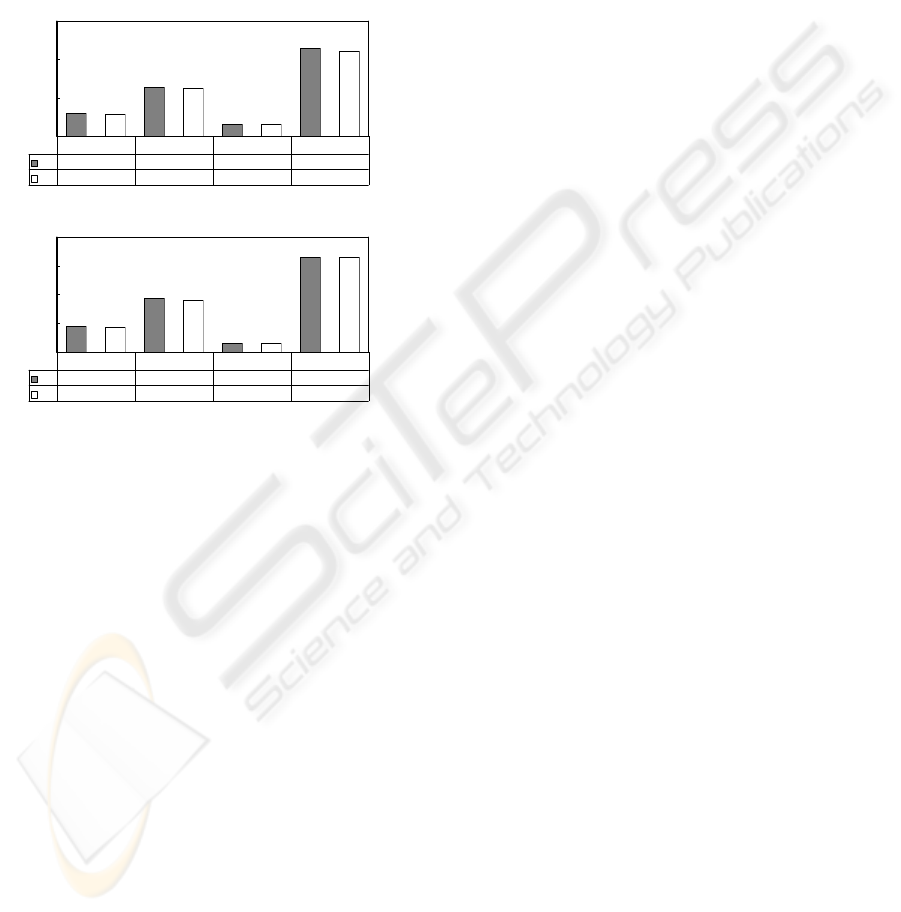
Comparing the mean of cycle time, the LS
method has an average 128.52 steps in simulation I
and 371.64 steps in simulation II. The LB method
has an average 125.63 and 356.50 steps in
simulation I and II. LB is better than LS 2.30% in
simulation I and 4.25% in simulation II. For the
deviation of steps of all wafer lots in these two
simulations, the LB approach is better than the LS
approach.
Simulation I
30
228
56.62
125.63
30
222
58.50
128.52
0
100
200
300
LS
58.50 128.52 30 228
LB
56.62 125.63 30 222
σ Mean Min Max
Simulation II
178.73
59
661
356.50
59
656
371.64
173.30
0
200
400
600
800
LS
178.73 371.64 59 661
LB
173.30 356.50 59 656
σ Mean Min Max
Figure 4: Result of simulation I & II.
Although the simulations are simplified, they
reflect the real situation we have met in the factory.
It is not difficult to extend the simulation with more
machines, wafer lots, and stages. We can use
different numbers of r
2
together, e.g., r
2
, r
2
r
2
, or
r
2
r
2
r
2
r
2
,…, for the task patterns to represent different
process time of different photolithography stages.
6 CONCLUSION
To provide the solution to the issue of dedicated
machine constraint, the proposed Load Balancing
(LB) scheduling approach has been presented. Along
with providing the LB scheduling approach to the
dedicated machine constraint, we also presented a
novel model--the representation and manipulation
method for the task patterns. The simulations also
showed that our proposed LB scheduling approach
was better than the LS method. The advantage of LB
is that we could easily schedule the wafer lots by
simple calculation on a two-dimensional matrix.
Moreover, the matrix architecture is easy for
practicing other semiconductor manufacturing
problems in the area with a similar constraint.
ACKNOWLEDGEMENTS
This research was supported in part by the Ministry
of Education under grant EX-91-E-FA06-4-4 and
the National Science Council under grant NSC-94-
2213-E-194-010 and NSC-92-2917-I-194-005. This
research was also partially supported by the U.S.
National Science Foundation grant No. IIS-0326387.
One of us, A. Shr, is grateful to Ms. Victoria Tangi
for English proof-reading.
REFERENCE
Arisha, A. and Young, P., 2004 Intelligent Simulation-
based Lot Scheduling of Photolithography Toolsets in
a Wafer Fabrication Facility. 2004 Winter Simulation
Conference, pp. 1935-1942.
Chern, C. and Liu, Y., 2003. Family-Based Scheduling
Rules of a Sequence-Dependent Wafer Fabrication
System. In IEEE Transactions on Semiconductor
Manufacturing, Vol. 16, No. 1, pp. 15-25.
Hildum, D., 1994. Flexibility in a Knowledge-based
System for Solving Dynamic Resource-Constrained
Scheduling Problem. Umass CMPSCI Technical
Report UM-CS-1994-77, University of Massachusetts,
Amherst.
Kumar, P.R., 1993. Re-entrant Lines. In Queuing Systems:
Theory and Applications, Special Issue on Queuing
Networks, Vol. 13, Nos. 1-3, pp. 87-110.
Kumar, P.R., 1994. Scheduling Manufacturing Systems of
Re-Entrant Lines. Stochastic Modeling and Analysis of
Manufacturing Systems, David D. Yao (ed.), Springer-
Verlag, New York, pp. 325-360.
Kumar, S. and Kumar, P.R., 2001. Queuing Network
Models in the Design and Analysis of Semiconductor
Wafer Fabs. In IEEE Transactions on Robotics and
Automation, Vol. 17, No. 5, pp. 548-561.
Lu, S.H. and Kumar, P.R., 1991. Distributed Scheduling
Based on Due Dates and Buffer Priorities. In IEEE
Transactions on Automatic Control, Vol. 36, No. 12,
pp. 1406-1416.
Mönch, L., et al., 2001. Simulation-Based Solution of
Load-Balancing Problems in the Photolithography
Area of a Semiconductor Wafer Fabrication Facility.
2001 Winter Simulation Conference, pp. 1170-1177.
Shen, Y. and Leachman, R.C., 2003. Stochastic Wafer
Fabrication Scheduling. In IEEE Transactions on
Semiconductor Manufacturing, Vol. 16, No. 1, pp. 2-
14 .
Wein, L.M., 1998. Scheduling Semiconductor Wafer
Fabrication. In IEEE Transactions on Semiconductor
Manufacturing, Vol. 1, No. 3, pp. 115-130.
Zhou, M. and Jeng, M.D., 1998. Modeling, Analysis,
Simulation, Scheduling, and Control of Semiconductor
Manufacturing System: A Petri Net Approach. In
IEEE Transactions on Semiconductor Manufacturing,
Vol. 11, No. 3, pp. 333-357.
A LOAD BALANCING SCHEDULING APPROACH FOR DEDICATED MACHINE CONSTRAINT
175