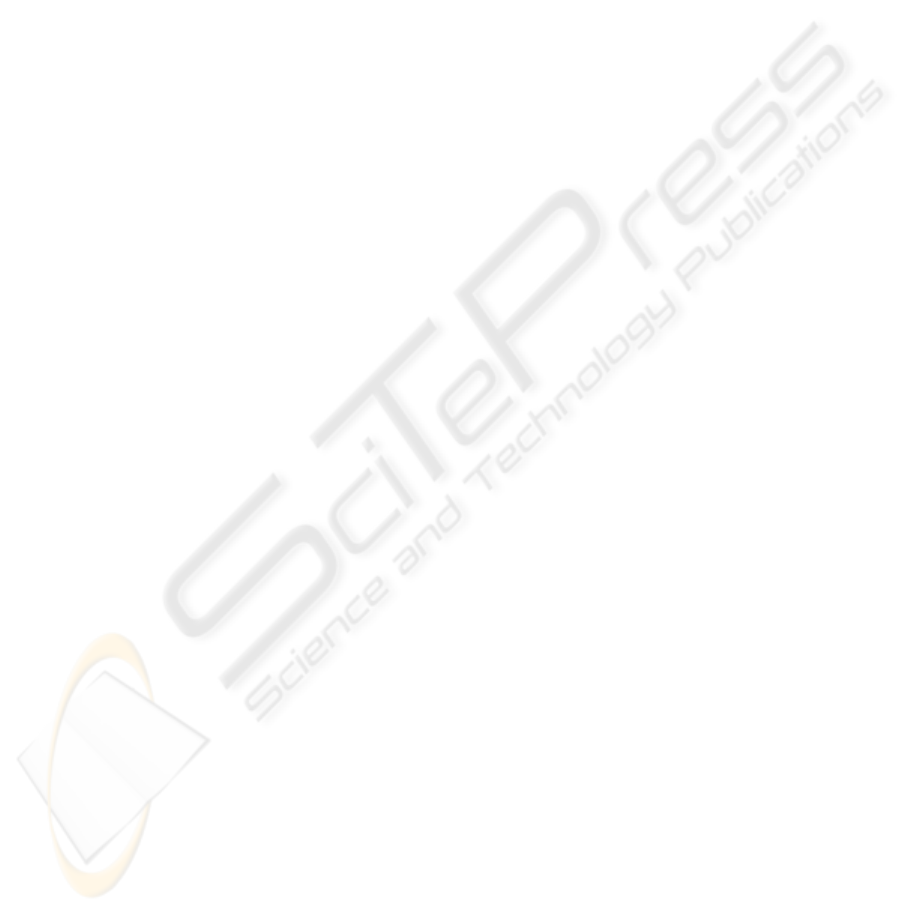
their informational views in manufacturing
environment. Then, we introduced how the holon
approach can be used for enterprise interoperability
issues. Afterwards, an implementation of our
approach in a commercial CASE tool is presented.
We also establish a translation mechanism based on
meta-model mappings that enables applications
using the holonic meta-model to exchange models
with other applications based on different meta-
models, this mechanism is based on the MDA
approach for interoperability.
Ongoing works handle experimentation of the
overall approach in an industrial case study, this
work is used to verify usability and limits of the
approach in real larger scale experiments. Tests are
organised into two classes, testing the modelling
approach in a real industrial environment and testing
the interoperability issues; results are to be published
in future papers.
ACKNOWLEDGEMENTS
This work was funded by the European Commission
IST 6th framework programme within the
framework of the Network of Excellence INTEROP.
The authors would like to thank the entire INTEROP
core.
REFERENCES
B2MML, 2003 The World Batch Forum. Business To
Manufacturing Markup Language, version 2.0, 2003.
Baïna.S, H. Panetto and G. Morel, 2005. A holonic
approach for application interopearbility in
manufacturing systems environment. In Proc of the
16
th
IFAC World Congress, Prague, July 4-8, 2005.
Berio G., et al. 2003 D3.2: Core constructs, architecture
and development strategy, UEML TN IST – 2001 –
34229, March 2003.
Breton E and Bézivin, J (2001) “Model-Driven Process
Engineering”, 25th Annual International Computer
Software and Applications Conference
(COMPSAC’01), Chicago, Illinois, Etats-Unis,
Octobre 2001.
IEC 62264, 2002. IEC FDIS 62264-1:2002. Enterprise-
control system integration, Part 1. Models and
terminology, IEC, Geneva.
Kalfoglou, Y. and Schorlemmer, M., 2004. Formal
Support for Representing and Automating Semantic
Interoperability. In Proceedings of 1st European
Semantic Web Symposium (ESWS'04), pp. 45-61,
Heraklion, Crete, Greece.
Kalfoglou, Y. and Schorlemmer, M. 2003. « Ontology
Mapping: The State of The Art. ». The Knowledge
Engineering Review, 18: 1-31. 2003. Cambridge
University Press
Koestler, A., 1967. The Ghost in the Machine Arkana,
London.
Lemesle, R., 1998. Transformation Rules Based on Meta-
Modelling. EDOC'98, La Jolla, California, 3-5
November 1998, p. 113-122.
Mc Farlane, D and Bussmann, S. (2000) Developments in
holonic production planning and control, International
Journal of Production Plannig and Control, Vol. 11,
N° 6, pp. 522-536
Morel G., H. Panetto H., M.B. Zaremba and F. Mayer
2003. Manufacturing Enterprise Control and
Management System Engineering: paradigms and
open issues. IFAC Annual Reviews in Control. 27/2,
199-209, December.
Mellor S.J., Kendall S., Uhl A. and Weise D. 2004. Model
Driven Architecture, Addison-Wesley Pub Co, March,
ISBN: 0201788918.
Naumenko, A., Wegmann, A., 2003. Two Approaches in
System Modelling and Their Illustrations with MDA
and RM-ODP. In ICEIS’03, 5th International
Conference on Enterprise Information Systems.
Panetto H., Berio, G., Benali, K., Boudjlida, N. and Petit,
M., 2004. A Unified Enterprise Modelling Language
for enhanced interoperability of Enterprise Models.
Proceedings of IFAC INCOM 2004 Symposium, April
5th-7th, Bahia, Brazil.
Panetto H. and Pétin, J.F., 2005. Metamodelling of
production systems process models using UML
stereotypes, International Journal of Internet and
Enterprise Management, 3/2, 155-169 - Inderscience
Publisher, ISSN: 1476-1300, 2005.
Seidel, D. and Mey, M. 1994, IMS - Holonic
Manufacturing Systems: Glossary of Terms, In Seidel
D. and Mey M. (eds), IMS - Holonic Manufacturing
Systems: Strategies Vol. 1, March, IFW, University of
Hannover, Germany.
Tolk, A. and Muguira J. A. (2003). The Levels of
Conceptual Interoperability Model. Simulation
Interoperability Workshop Orlando, USA, Sept 2003.
UML. 2005. Unified Modeling Language, UML2 OCL
specification, document ptc/05-06-06, OMG.
Valckenaers, P. (2001), Special issue: Holonic
Manufacturing Systems, Computer In Industry, 46 (3),
pp. 233-331.
ICEIS 2006 - INFORMATION SYSTEMS ANALYSIS AND SPECIFICATION
26