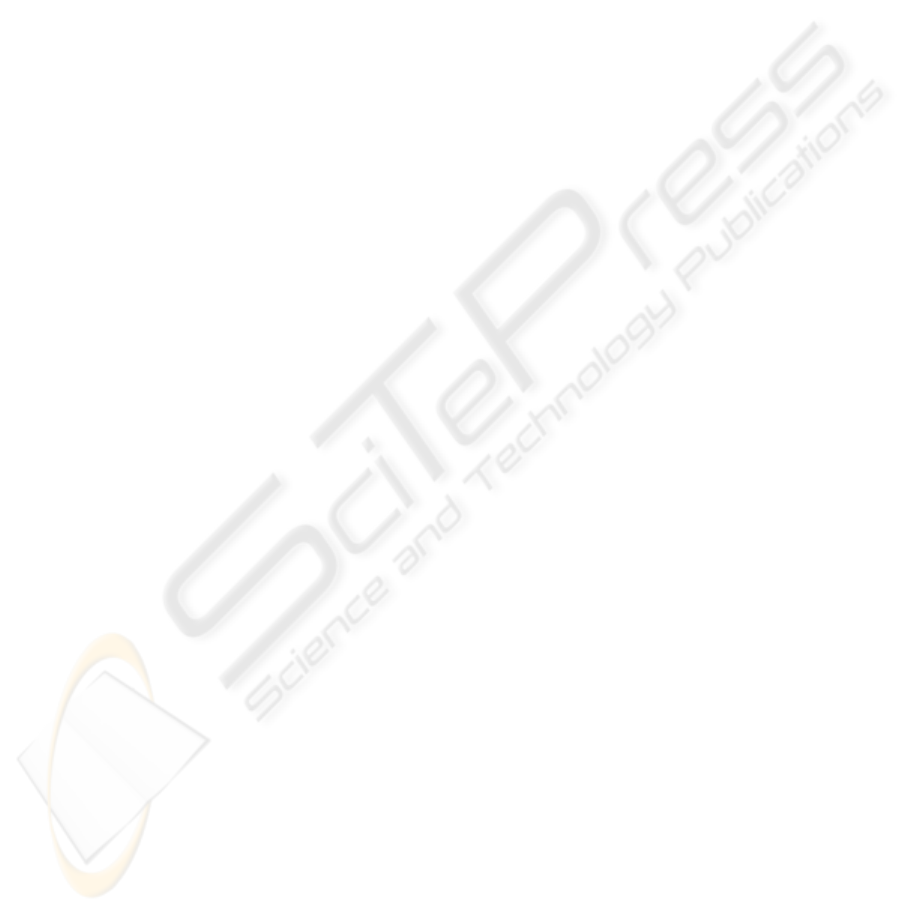
5 Conclusions
The ultra low cost system presented in this paper is capable of locating the position of
a target on a grid plane covering distances of more than one meter with adequate
accuracy (less than 10cm error). The coordinate estimation method is based on the
success rate that multiple pattern types are received at a specific position. The closer
node of the grid is located first and then a 2D interpolation search estimates the exact
target position. Using an appropriate topology of the pattern transmitting devices, the
grid squares that allow reliable position estimation were mapped. The factors
affecting the speed of the position estimation method were also discussed.
Future work will focus on studying proper topologies of more than 2 infrared
transmitting devices in order to extend optimally the area covered. Moreover, it will
be attempted to increase the degrees of freedom of the moving target. The history of
movements of the target will also be exploited in order to predict potential future
positions and increase the stability of the coordinate estimation.
References
1. Hoffman-Wellenhoff, B., Lichtenegger, H. and Collins, J.: Global Positioning Systems,
Theory and Practice. Springer-Verlang, Berlin (1997)
2. Salamah, M., Doukhnitch, E. and Devrim, D.: A Fast HW Oriented Algorithm for Cellular
Mobiles Positioning. Springer-Verlag Berlin Heidelberg LNCS 3280 (2004) 267-277
3. Borenstein, J., Everett, B. and Feng, L.: Navigating Mobile Robots: Systems and
Techniques. A.K. Peters Ltd. Wellesley, MA (1996)
4. Coor-Harbo, A.: Geometrical Modeling of a Two Dimensional Sensor Array for
Determining Spatial Position of a Passive Object. IEEE Sensors Journal, Vol 4, No 5, (Oct
2004) 627-642
5. Fox, D., Burgard, W., and Thrun, S.: Markov Localization for Mobile Robots in Dynamic
Environments. Journal of Artificial Intelligence Research, 11 (1999) 391-427
6. Krohn, A., Beigl, M., Hazas, M., Gellersen, H.-W.: Using Fine-Grained Infrared
Positioning to Support the Surface-Based Activities of Mobile Users. 5
th
IWSAWC,
ICDCSW (2005) 463-468
7. Aytac, T. and Barshan, B.: Simultaneous Extraction of Geometry and Surface Properties of
Targets Using Simple Infrared Sensors. Optical Eng. 43(10), (2004) 2437-2447
8. Kosel, J., Pfutzner, H., Mehnen, L., Kaniusas, E., Meydan, T., Vazquez, N., Rohn, M.,
Merlo, A.M. and Marquardt, B.: Non Contact Detection of Magnetoelastic Position
Sensors. Elsevier Sensors And Actuators, A 123-124 (2005) 349-353
9. Prigge, E.A. and How J.P.: Signal Architecture for Distributed Magnetic Local Positioning
System. IEEE Sensors Journal, Vol. 4, No. 6, (Dec 2004) 864-873
10. Petrellis, N., Konofaos, N. and Alexiou G.: Testing IR Photon Sensors for Target
Localization Applications. International Workshop on Advances in Sensors and Interfaces,
Bari, Italy, Apr. 19 (2005) 153-158
28