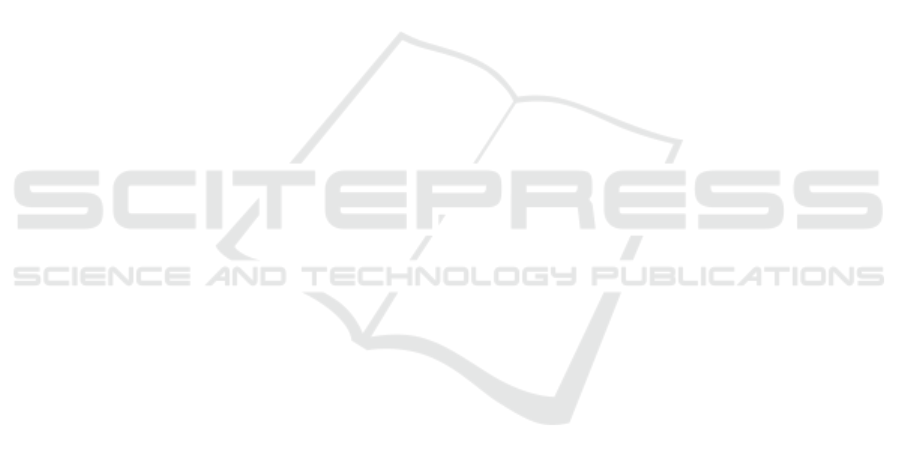
loss of information, for later process the information
in our predictive tool.
Using industry 4.0 technology a tool developed to
control the machine in real time has been created, fol-
lowing the OEM trend of transform their current man-
ufacturing facilities in smart factories. The tool devel-
oped works as expected in real-time and give accurate
and valuable information about the slide state work-
ing, been able to control parallelism and friction in
the gibs reducing maintenance activity and premature
wear altogether with reduction of electrical consump-
tion. Furthermore the developed tool result as a ro-
bust and powerful method that gives a lot of opportu-
nities when talking about predictive maintenance and
knowing the machine health, taking the lead predict-
ing breakdowns.
ACKNOWLEDGEMENTS
This study was supported by the Universidad CEU
Cardenal Herrera, Ford Spain S.L. and Fundaci
´
on
para el Desarrollo y la Investigaci
´
on (FDI), Spain,
which the authors gratefully acknowledge.
REFERENCES
Ahmetoglu, M., Broek, T., Kinzel, G., and Altan, T. (1995).
Control of blank holder force to eliminate wrinkling
and fracture in deep-drawing rectangular parts. CIRP
annals, 44(1):247–250.
Endelt, B., Tommerup, S., and Danckert, J. (2013). A
novel feedback control system–controlling the ma-
terial flow in deep drawing using distributed blank-
holder force. Journal of Materials Processing Tech-
nology, 213(1):36–50.
Garcia, E. and Montes, N. (2019). Mini-term, a novel
paradigm for fault detection. IFAC-PapersOnLine,
52(13):165–170.
Garc
´
ıa, E., Mont
´
es, N., and Alacreu, M. (2018). Towards
a knowledge-driven maintenance support system for
manufacturing lines. In ICINCO (1), pages 53–64.
Hardt, D. E. (1993). Modeling and control of manufacturing
processes: getting more involved.
Hardt, D. E. (2017). Forming processes: Monitoring and
control. The Mechanical Systems Design Handbook:
Modeling, Measurement, and Control.
Hardt, D. E. and Fenn, R. C. (1993). Real-time control of
sheet stability during forming.
Hoffman, H. (1998). Metal forming handbook. Springer
Science & Business Media.
Hsu, C.-W., Ulsoy, A., and Demeri, M. (2000). An ap-
proach for modeling sheet metal forming for process
controller design. J. Manuf. Sci. Eng., 122(4):717–
724.
Hsu, C.-W., Ulsoy, A., and Demeri, M. (2002). Develop-
ment of process control in sheet metal forming. Jour-
nal of Materials Processing Technology, 127(3):361–
368.
Lim, Y., Ulsoy, A. G., and Venugopal, R. (2013). Process
control for sheet-metal stamping. Springer.
Lim, Y., Venugopal, R., and Ulsoy, A. (2012). Auto-tuning
and adaptive stamping process control. Control Engi-
neering Practice, 20(2):156–164.
Lim, Y., Venugopal, R., and Ulsoy, A. G. (2008). Advances
in the control of sheet metal forming. IFAC Proceed-
ings Volumes, 41(2):1875–1883.
Lim, Y., Venugopal, R., and Ulsoy, A. G. (2010). Multi-
input multi-output (mimo) modeling and control for
stamping. Journal of dynamic systems, measurement,
and control, 132(4).
Magraner, E. G. (2016). An
´
alisis de los sub-tiempos
de ciclo t
´
ecnico para la mejora del rendimiento de
las l
´
ıneas de fabricaci
´
on/tesis doctoral presentada
por Eduardo Garc
´
ıa Magraner; dirigida por Nicol
´
as
Mont
´
es S
´
anchez. PhD thesis, Universidad CEU-
Cardenal Herrera.
Maugin, G. (1980). The method of virtual power in con-
tinuum mechanics: application to coupled fields. Acta
Mechanica, 35(1):1–70.
Ng, Y.-M. H., Yu, M., Huang, Y., and Du, R. (2007). Di-
agnosis of sheet metal stamping processes based on
3-d thermal energy distribution. IEEE transactions on
automation science and engineering, 4(1):22–30.
Shang, J. and Daehn, G. (2011). Electromagnetically as-
sisted sheet metal stamping. Journal of Materials Pro-
cessing Technology, 211(5):868–874.
Siegert, K., Ziegler, M., and Wagner, S. (1997). Closed
loop control of the friction force. deep drawing pro-
cess. Journal of materials processing technology,
71(1):126–133.
Song, J., Kim, S., Liu, Z., Quang, N. N., and Bien, F.
(2016). A real time nondestructive crack detection
system for the automotive stamping process. IEEE
Transactions on Instrumentation and Measurement,
65(11):2434–2441.
Ubhayaratne, I., Xiang, Y., Pereira, M., and Rolfe, B.
(2015). An audio signal based model for condition
monitoring of sheet metal stamping process. In 2015
IEEE 10th Conference on Industrial Electronics and
Applications (ICIEA), pages 1267–1272. IEEE.
Viswanathan, V., Kinsey, B., and Cao, J. (2003). Experi-
mental implementation of neural network springback
control for sheet metal forming. J. Eng. Mater. Tech-
nol., 125(2):141–147.
Wagener, H.-W. (1997). New developments in sheet metal
forming: sheet materials, tools and machinery. Jour-
nal of materials processing technology, 72(3):342–
357.
Yagami, T., Manabe, K.-i., Yang, M., and Koyama, H.
(2004). Intelligent sheet stamping process using seg-
ment blankholder modules. Journal of Materials Pro-
cessing Technology, 155:2099–2105.
ICINCO 2021 - 18th International Conference on Informatics in Control, Automation and Robotics
402