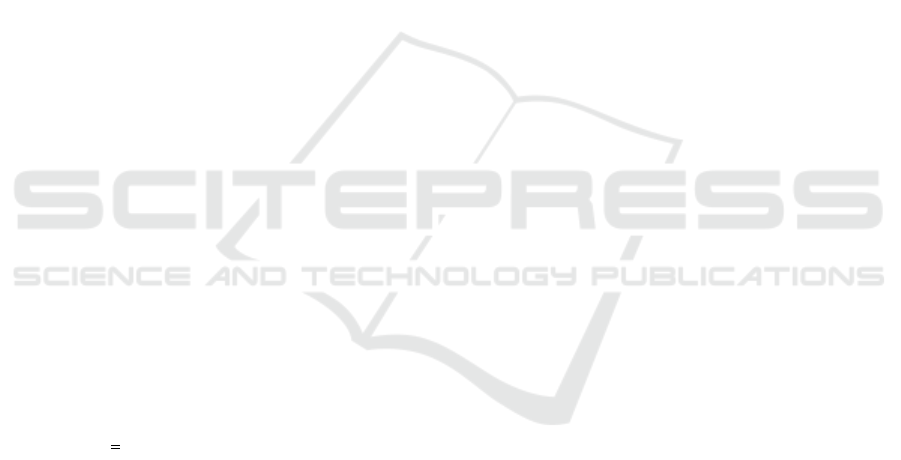
ference on Computer Vision and Pattern Recognition
(CVPR), pages 770–778.
Hruaia, V., Kirani, Y., and Singh, N. (2017). Binary face
image recognition using logistic regression and neural
network. pages 3883–3888.
ICRISAT (2020). International crop research institute
for the semi-arid tropics , labor scarcity and rising
wages in indian agriculture. https://www.icrisat.org/
labor-scarcity-and-rising-wages-in-indian-agriculture/.
Ku, L. (2019). How automation is trans-
forming the farming industry. https:
//www.plugandplaytechcenter.com/resources/
how-automation-transforming-farming-industry/.
Lakhiar, I., Jianmin, G., Syed, T., Chandio, F. A., Buttar, N.,
and Qureshi, W. (2018). Monitoring and control sys-
tems in agriculture using intelligent sensor techniques:
A review of the aeroponic system. Journal of Sensors,
2018:18.
Lu, X., Ono, E., lu, S., Zhang, Y., Teng, P., Aono, M.,
Shimizu, Y., Hosoi, F., and Omasa, K. (2020). Re-
construction method and optimum range of camera-
shooting angle for 3d plant modeling using a multi-
camera photography system. Plant Methods, 16.
Ma, C., Xu, S., Yi, X., Li, L., and Yu, C. (2020). Re-
search on image classification method based on dcnn.
In 2020, ICCEA, pages 873–876.
Mussabayev, R., Kalimoldayev, M., Amirgaliyev, Y.,
Tairova, A., and Mussabayev, T. (2018). Calculation
of 3d coordinates of a point on the basis of a stereo-
scopic system. Open Engineering, 8(1):109–117.
Nandi, C., Tudu, B., and Koley, C. (2013). Machine vision
based techniques for automatic mango fruit sorting
and grading based on maturity level and size. Sens-
ing Technology: Current Status and Future Trends II,
8:27–46.
Payne, A., Walsh, K., Subedi, P., and Jarvis, D. (2014). Es-
timating mango crop yield using image analysis us-
ing fruit at ‘stone hardening’ stage and night time
imaging. Computers and Electronics in Agriculture,
100:160–167.
Prabakar, C., Devi, K., and Selvam, S. (2011). Labour
scarcity
ˆ
aC“ its immensity and impact on agriculture.
Agricultural Economics Research Review.
Quigley, M., Conley, K., Gerkey, B., Faust, J., Foote, T.,
Leibs, J., Wheeler, R., and Ng, A. (2009). Ros: an
open-source robot operating system. volume 3.
Riquelme, M., Barreiro, P., Ruiz-Altisent, M., and Valero,
C. (2008). Olive classification according to external
damage using image analysis. Journal of Food Engi-
neering, 87:371–379.
Santos, T. T., Koenigkan, L. V., Barbedo, J. G. A., and Ro-
drigues, G. C. (2015). 3d plant modeling: Localiza-
tion, mapping and segmentation for plant phenotyping
using a single hand-held camera. In Agapito, L., Bron-
stein, M. M., and Rother, C., editors, Computer Vi-
sion - ECCV 2014 Workshops, pages 247–263, Cham.
Springer International Publishing.
Sodhi, P., Vijayarangan, S., and Wettergreen, D. (2017).
In-field segmentation and identification of plant struc-
tures using 3d imaging. In 2017 IEEE/RSJ (IROS),
pages 5180–5187.
Stajnko, D., Lakota, M., and Ho
ˇ
cevar, M. (2004). Estima-
tion of number and diameter of apple fruits in an or-
chard during the growing season by thermal imaging.
Computers and Electronics in Agriculture, 42(1):31–
42.
Sun, X., Liu, L., Wang, H., Song, W., and Lu, J. (2015).
Image classification via support vector machine. In
2015 4th ICCSNT, volume 01, pages 485–489.
Sun, Y., Gao, W., Pan, S., Zhao, T., and Peng, Y. (2021).
An efficient module for instance segmentation based
on multi-level features and attention mechanisms. Ap-
plied Sciences, 11(3).
Takikawa, T., Acuna, D., Jampani, V., and Fidler, S. (2019).
Gated-scnn: Gated shape cnns for semantic segmen-
tation.
Tian, H., Wang, T., Liu, Y., Qiao, X., and Li, Y. (2019).
Computer vision technology in agricultural automa-
tion ——a review. Information Processing in Agri-
culture, 7.
TOMBE, R. (2020). Computer vision for smart farming
and sustainable agriculture. In 2020 IST-Africa Con-
ference (IST-Africa), pages 1–8.
Torrey, L. and Shavlik, J. (2009). Transfer learning. Hand-
book of Research on Machine Learning Applications.
Unay, D., Gosselin, B., Kleynen, O., Leemans, V., Destain,
M.-F., and Debeir, O. (2011). Automatic grading
of bi-colored apples by multispectral machine vision.
Computers and Electronics in Agriculture - COMPUT
ELECTRON AGRIC, 75:204–212.
ˇ
Svec, M. and Farkas, I. (2014). Calculation of object posi-
tion in various reference frames with a robotic simu-
lator.
Wu, H., Zhang, J., Huang, K., Liang, K., and Yu, Y. (2019).
Fastfcn: Rethinking dilated convolution in the back-
bone for semantic segmentation.
Xia, C., Wang, L., Chung, B.-K., and Lee, J.-M. (2015). In
situ 3d segmentation of individual plant leaves using
a rgb-d camera for agricultural automation. Sensors,
15(8):20463–20479.
Xu, D. and Li, H. (2008). Geometric moment invariants.
Pattern Recognit., 41:240–249.
Yang, L. and Albregtsen, F. (1995). Fast and exact compu-
tation of moments using discrete green’s theorem.
Zamora-Izquierdo, M., Santa, J., Martinez, J., Mart
´
ınez, V.,
and Skarmeta, A. (2019). Smart farming iot platform
based on edge and cloud computing. Biosystems En-
gineering, 2019:4–17.
Zhang, M. and Smart, W. (2004). Multiclass object classi-
fication using genetic programming. In Raidl, G. R.,
Cagnoni, S., Branke, J., Corne, D. W., Drechsler, R.,
Jin, Y., Johnson, C. G., Machado, P., Marchiori, E.,
Rothlauf, F., Smith, G. D., and Squillero, G., editors,
Applications of Evolutionary Computing, pages 369–
378, Berlin, Heidelberg. Springer Berlin Heidelberg.
Zhao, Z.-Q., Zheng, P., Xu, S.-T., and Wu, X. (2019). Ob-
ject detection with deep learning: A review. IEEE
Transactions on Neural Networks and Learning Sys-
tems, 30(11):3212–3232.
P2Ag: Perception Pipeline in Agriculture for Robotic Harvesting of Tomatoes
129