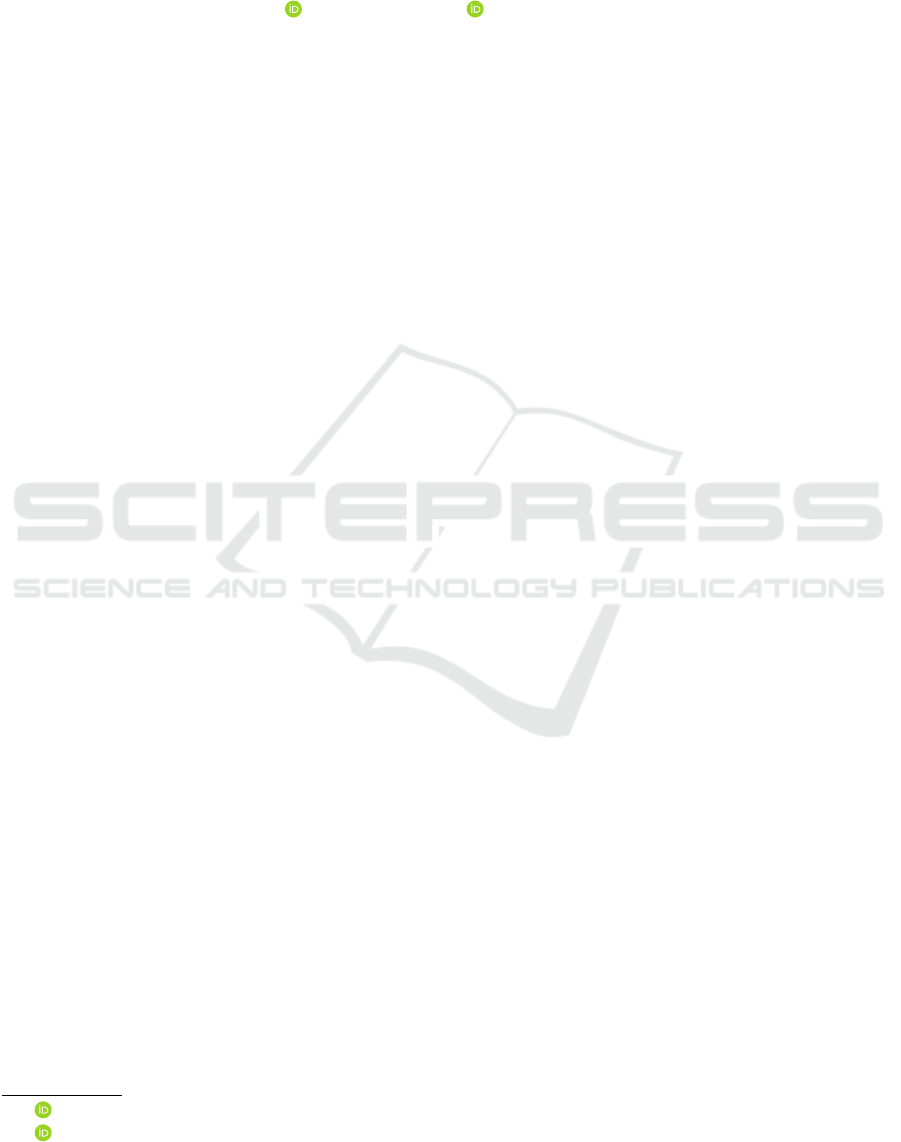
Conversion Method of MATLAB/Simulink Model for a Functional
Resonance Analysis Method-based Model
Masamichi Kakeshita
1 a
, Kenji Hisazumi
2 b
, Yasutaka Michiura
3
, Keita Sakemi
3
and Michihiro Matsumoto
3
1
Kyushu University, 744 Motooka, Nishi-ku, Fukuoka, 819-0395, Japan
2
Department of Electronic Information Systems, Faculty of Systems Science and Engineering,
Shibaura Institute of Technology, 307 Fukasaku, Minuma-ku, Saitama-shi, Saitama, 337-8570, Japan
3
Japan Manned Space Systems Corporation, 8F, Otemachi Bldg., 1-6-1, Otemachi, Chiyoda-ku, Tokyo, 100-0004, Japan
Keywords:
Embedded System, Safety Analysis, MATLAB/Simulink, Functional Resonance Analysis Method.
Abstract:
In recent years, model-based development (MBD) has become popular in control-embedded systems, and
development specifications are being written using MATLAB/Simulink and other tools. The functional res-
onance analysis method (FRAM) is used for safety analysis of socio-technical systems. It is used to foster
success factors without being trapped in failures. Application of FRAM to MBD models is expected to
improve the quality of MBD models from a new perspective; however, an approach for the application of
FRAM to MBD has not been established yet. Therefore, in this study, we proposed a method to convert
MATLAB/Simulink models into FRAM models. Consequently, the application of the proposed method to the
Simulink model led to an improvement through creation and analysis of the FRAM model. In contrast, there
are certain scenarios that can occur in the Simulink model that are not represented in the completed FRAM
model, as the FRAM model only represents the interactions inside the system, which makes it difficult to thor-
oughly analyze the system with respect to external influences. Our future work shall include a further study
on how to represent information when converting MATLAB/Simulink models to FRAM models and further
applying the method to Simulink models that users can directly modify.
1 INTRODUCTION
Previously, we wrote development specifications for
embedded systems in control systems using natu-
ral language during requirements analysis, followed
by the design process. In recent years, however,
model-based development (MBD) has gained pop-
ularity, and we now write development specifica-
tions in MBD models, such as MATLAB/Simulink
or Simulink models instead. Conventional develop-
ment specifications, which were earlier written in nat-
ural language, posed the risk of varied interpretations
by various people, owing to their ambiguous descrip-
tions. However, Simulink models can eliminate such
risks because they are expressed in an elaborate man-
ner.
The functional resonance analysis method
(FRAM)(Hollnagel, 2017) is a safety analysis
method for sociotechnical systems. Traditional safety
analysis methods, such as fault tree analysis (Vesely
a
https://orcid.org/0000-0002-0308-0566
b
https://orcid.org/0000-0003-2452-6552
et al., 1981), are based on the idea that poor outcomes
result from failures; however, success often accounts
for the majority of events. Furthermore, there are
various cases in which successful events exist despite
the occurrence of unexpected accidents. Therefore,
it is not necessarily reasonable to focus only on
failures. FRAM, on the other hand, defines functions
and characterizes each function based on six different
aspects to create a model and conduct an analysis of
the variation of these functions. Thus, it allows us
to analyze without getting trapped in failures, and
cultivate success factors, such as ”how does it work
well?”.
As mentioned earlier, new safety analysis meth-
ods are emerging, and the application of these meth-
ods to Simulink models may lead to new discoveries.
However, thus far, no method for applying FRAM to
Simulink models has been established. In fact, var-
ious difficulties have been encountered in the appli-
cation of FRAM to Simulink models. The develop-
ment specifications of MBD are often at a low level
of abstraction. However, creating a FRAM model re-
quires reverse modeling with a detailed understand-
234
Kakeshita, M., Hisazumi, K., Michiura, Y., Sakemi, K. and Matsumoto, M.
Conversion Method of MATLAB/Simulink Model for a Functional Resonance Analysis Method-based Model.
DOI: 10.5220/0010845600003119
In Proceedings of the 10th International Conference on Model-Driven Engineering and Software Development (MODELSWARD 2022), pages 234-241
ISBN: 978-989-758-550-0; ISSN: 2184-4348
Copyright
c
2022 by SCITEPRESS – Science and Technology Publications, Lda. All rights reserved