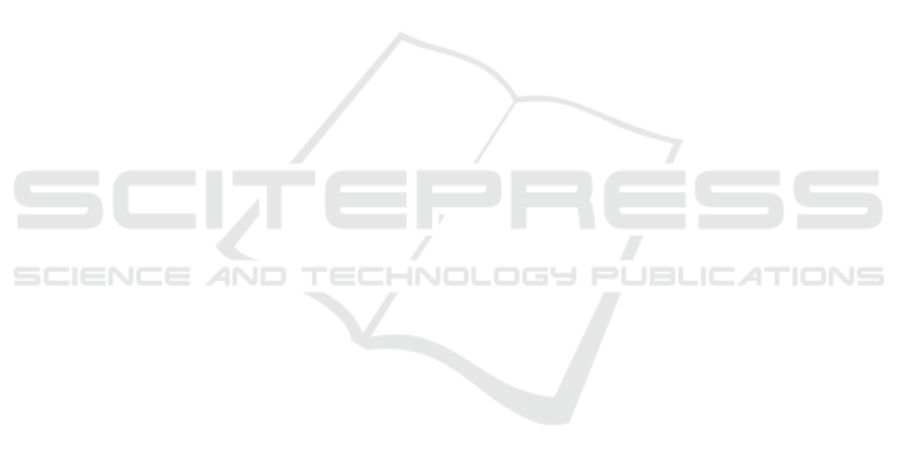
New York, NY, USA. Association for Computing Ma-
chinery.
Hahn, A., Kregel, B., Govindarasu, M., Fitzpatrick, J., Ad-
nan, R., Sridhar, S., and Higdon, M. (2010). Develop-
ment of the powercyber scada security testbed. Pro-
ceedings of the Sixth Annual Workshop on Cyber Se-
curity and Information Intelligence Research.
Holm, H., Karresand, M., Vidstr
¨
om, A., and Westring, E.
(2015). A survey of industrial control system testbeds.
In Buchegger, S. and Dam, M., editors, Secure IT Sys-
tems, pages 11–26. Springer International Publishing.
Kaspersky Lab (2021a). Apt attacks on industrial com-
panies in 2020. Technical report, AO KASPERSKY
LAB.
Kaspersky Lab (2021b). Threat landscape for industrial au-
tomation systems. Technical report, AO KASPER-
SKY LAB.
Koganti, V. S., Ashrafuzzaman, M., Jillepalli, A. A., and
Sheldon, F. T. (2017). A virtual testbed for security
management of industrial control systems. In 2017
12th International Conference on Malicious and Un-
wanted Software (MALWARE), pages 85–90.
Korkmaz, E., Dolgikh, A., Davis, M., and Skormin, V.
(2016). Industrial control systems security testbed. In
11th Annual Symposium on Information Assurance.
Krishnan, S. and Wei, M. (2019). SCADA testbed for vul-
nerability assessments, penetration testing and inci-
dent forensics. In 2019 7th International Symposium
on Digital Forensics and Security (ISDFS), pages 1–6.
Larrucea, X. and Molinuevo, A. (2020). An ICS based
scenario generator for cyber ranges. In Yilmaz, M.,
Niemann, J., Clarke, P., and Messnarz, R., editors,
Systems, Software and Services Process Improvement,
pages 543–554. Springer International Publishing.
Lewis, J. A. (2015). The role of offensive cyber operations
in nato’s collective defence. The tallin papers.
Mallouhi, M., Al-Nashif, Y., Cox, D., Chadaga, T., and
Hariri, S. (2011). A testbed for analyzing security of
scada control systems (tasscs). In ISGT 2011, pages
1–7.
Mathur, A. P. and Tippenhauer, N. O. (2016). Swat: a wa-
ter treatment testbed for research and training on ics
security. In 2016 International Workshop on Cyber-
physical Systems for Smart Water Networks (CySWa-
ter), pages 31–36.
Miru, G. (2016a). The siemens s7 communication - part 1
general structure. http://gmiru.com/article/s7comm/.
Accessed: 27.04.2021.
Miru, G. (2016b). The siemens s7 communication -
part 2. http://gmiru.com/article/s7comm-part2/. Ac-
cessed:15.05.2021.
MITRE (2021). Apt groups. https://attack.mitre.org/
groups/. Accessed: 13/03/2021.
MITRE ATT&CK® (2021). Mitre att&ck®. https://attack.
mitre.org/. Accessed: 01.04.2021.
Modbus (2021). Modbus official technical resources. https:
//www.modbus.org/tech.php. Accessed:15.05.2021.
Morris, T., Srivastava, A., Reaves, B., Gao, W., Pavurapu,
K., and Reddi, R. (2011). A control system testbed
to validate critical infrastructure protection concepts.
International Journal of Critical Infrastructure Pro-
tection, 4(2):88 – 103.
Muller, L. P. (2019). Military offensive cyber-
capabilities:small-state perspectives. Technical report,
Netherlands.
Noorizadeh, M., Shakerpour, M., Meskin, N., Unal, D., and
Khorasani, K. (2021). A cyber-security methodology
for a cyber-physical industrial control system testbed.
IEEE Access, 9:16239–16253.
Pfrang, S., Kippe, J., Meier, D., and Haas, C. (2017). De-
sign and architecture of an industrial IT security lab.
In Guo, S., Wei, G., Xiang, Y., Lin, X., and Lorenz, P.,
editors, Testbeds and Research Infrastructures for the
Development of Networks and Communities, pages
114–123. Springer International Publishing.
Reaves, B. and Morris, T. (2012). An open virtual testbed
for industrial control system security research. Inter-
national Journal of Information Security, 11.
Rosa, L., Cruz, T., Sim
˜
oes, P., Monteiro, E., and Lev, L.
(2017). Attacking SCADA systems: A practical per-
spective. In 2017 IFIP/IEEE Symposium on Inte-
grated Network and Service Management (IM), pages
741–746.
Rubio-Hernan, J., Rodolfo-Mejias, J., and Garcia-Alfaro,
J. (2017). Security of cyber-physical systems. In
Cuppens-Boulahia, N., Lambrinoudakis, C., Cuppens,
F., and Katsikas, S., editors, Security of Industrial
Control Systems and Cyber-Physical Systems, pages
3–18. Springer International Publishing.
Snap7 (2021). Step7 open source ethernet communi-
cation suite. http://snap7.sourceforge.net/. Ac-
cessed:15.05.2021.
Stamp, J., Urias, V., and Richardson, B. (2011). Cyber secu-
rity analysis for the power grid using the virtual con-
trol systems environment. In 2011 IEEE Power and
Energy Society General Meeting, pages 1–4.
Stranahan, J., Soni, T., and Heydari, V. (2019). Supervisory
control and data acquisition testbed for research and
education. In 2019 IEEE 9th Annual Computing and
Communication Workshop and Conference (CCWC),
pages 0085–0089.
Su, W., Antoniou, A., and Eagle, C. (2017). Cyber security
of industrial communication protocols. In 2017 22nd
IEEE International Conference on Emerging Tech-
nologies and Factory Automation (ETFA), pages 1–4.
Tao, Y., Xu, W., Li, H., and Ji, S. (2019). Experience and
lessons in building an ICS security testbed. In 2019
1st International Conference on Industrial Artificial
Intelligence (IAI), pages 1–6.
UK Government (2016). National cyber security strategy
2016-2021. Technical report, UK.
Urdaneta, M., Lemay, A., Saunier, N., and Fernandez, J.
(2018). A cyber-physical testbed for measuring the
impacts of cyber attacks on urban road networks. In
Staggs, J. and Shenoi, S., editors, Critical Infrastruc-
ture Protection XII, pages 177–196. Springer Interna-
tional Publishing.
Werth, A. W. and Morris, T. H. (2021). Prototyping PLCs
and IoT devices in an HVAC virtual testbed to study
Industrial and Automation Control System Cyber Range Prototype for Offensive Capability Development
489