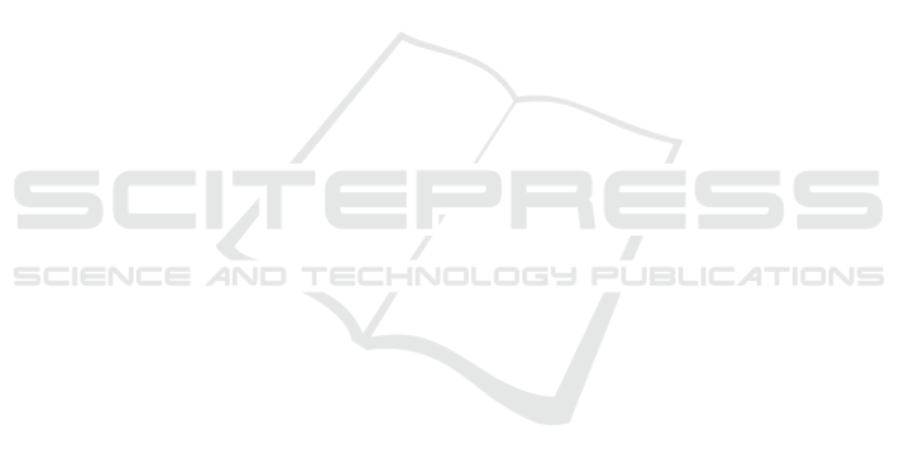
subtraction angiography images. Computer Methods
and Programs in Biomedicine, 94(3):267–278.
Imran, J. and Raman, B. (2020). Deep motion templates and
extreme learning machine for sign language recogni-
tion. The Visual Computer, 36(6):1233–1246.
Jin, H., Chen, Q., Chen, Z., Hu, Y., and Zhang, J.
(2016). Multi-leapmotion sensor based demonstration
for robotic refine tabletop object manipulation task.
CAAI Transactions on Intelligence Technology, 1.
Kiselev, V., Khlamov, M., and Chuvilin, K. (2019). Hand
gesture recognition with multiple leap motion devices.
In 2019 24th Conference of Open Innovations Associ-
ation (FRUCT), pages 163–169. IEEE.
Liu, Y. and Zhang, Y. (2014). Toward welding robot with
human knowledge: A remotely-controlled approach.
IEEE Transactions on Automation Science and Engi-
neering, 12(2):769–774.
Luzhnica, G., Simon, J., Lex, E., and Pammer, V. (2016).
A sliding window approach to natural hand gesture
recognition using a custom data glove. In 2016 IEEE
Symposium on 3D User Interfaces (3DUI), pages 81–
90. IEEE.
Mahdikhanlou, K. and Ebrahimnezhad, H. (2020). Mul-
timodal 3d american sign language recognition for
static alphabet and numbers using hand joints and
shape coding. Multimedia Tools and Applications,
79(31):22235–22259.
Marin, G., Dominio, F., and Zanuttigh, P. (2016). Hand
gesture recognition with jointly calibrated leap motion
and depth sensor. Multimedia Tools and Applications,
75(22):14991–15015.
Moro, S. B., Carrieri, M., Avola, D., Brigadoi, S., Lan-
cia, S., Petracca, A., Spezialetti, M., Ferrari, M.,
Placidi, G., and Quaresima, V. (2016). A novel
semi-immersive virtual reality visuo-motor task ac-
tivates ventrolateral prefrontal cortex: a functional
near-infrared spectroscopy study. Journal of Neural
Engineering, 13(3):1–14.
Mueller, F., Deuerlein, C., and Koch, M. (2019). Intuitive
welding robot programming via motion capture and
augmented reality. IFAC-PapersOnLine, 52(10):294–
299.
Oudah, M., Al-Naji, A., and Chahl, J. (2020). Hand gesture
recognition based on computer vision: A review of
techniques. Journal of Imaging, 6(8):73.
Petracca, A., Carrieri, M., Avola, D., Basso Moro, S.,
Brigadoi, S., Lancia, S., Spezialetti, M., Ferrari, M.,
Quaresima, V., and Placidi, G. (2015). A virtual
ball task driven by forearm movements for neuro-
rehabilitation. In 2015 International Conference on
Virtual Rehabilitation (ICVR), pages 162–163.
Placidi, G. (2007). A smart virtual glove for the hand tel-
erehabilitation. Computers in Biology and Medicine,
37(8):1100 – 1107.
Placidi, G., Avola, D., Cinque, L., Polsinelli, M., Theodor-
idou, E., and Tavares, J. M. R. S. (2021). Data inte-
gration by two-sensors in a LEAP-based virtual glove
for human-system interaction. Multimedia Tools and
Applications, 80(12):18263–18277.
Placidi, G., Avola, D., Iacoviello, D., and Cinque, L.
(2013). Overall design and implementation of the
virtual glove. Computers in Biology and Medicine,
43(11):1927–1940.
Placidi, G., Cinque, L., Petracca, A., Polsinelli, M., and
Spezialetti, M. (2017). A virtual glove system for
the hand rehabilitation based on two orthogonal leap
motion controllers. In Proceedings of the 6th Inter-
national Conference on Pattern Recognition Applica-
tions and Methods - Volume 1: ICPRAM,, pages 184–
192. INSTICC, SciTePress.
Placidi, G., Cinque, L., Polsinelli, M., and Spezialetti, M.
(2018). Measurements by a leap-based virtual glove
for the hand rehabilitation. Sensors, 18(3):1–13.
Placidi, G., Petracca, A., Spezialetti, M., and Iacoviello, D.
(2015). A modular framework for EEG web based
binary brain computer interfaces to recover communi-
cation abilities in impaired people. Journal of Medical
Systems, 40(1).
Shen, H., Yang, X., Hu, H., Mou, Q., and Lou, Y. (2019).
Hand trajectory extraction of human assembly based
on multi-leap motions. In 2019 IEEE/ASME Inter-
national Conference on Advanced Intelligent Mecha-
tronics (AIM), pages 193–198.
Smith, R., Cucco, E., and Fairbairn, C. (2020). Robotic
development for the nuclear environment: Challenges
and strategy. Robotics, 9(4):94.
Voulodimos, A., Doulamis, N., Doulamis, A., and Protopa-
padakis, E. (2018). Deep learning for computer vi-
sion: A brief review. Computational Intelligence and
Neuroscience, 2018:1–13.
Wang, Z., Wang, D., Zhang, Y., Liu, J., Wen, L., Xu, W.,
and Zhang, Y. (2020). A three-fingered force feed-
back glove using fiber-reinforced soft bending actu-
ators. IEEE Transactions on Industrial Electronics,
67(9):7681–7690.
Yang, L., Chen, J., and Zhu, W. (2020). Dynamic hand
gesture recognition based on a leap motion controller
and two-layer bidirectional recurrent neural network.
Sensors, 20:2106–2123.
Zhang, W., Cheng, H., Zhao, L., Hao, L., Tao, M., and
Xiang, C. (2019). A gesture-based teleoperation sys-
tem for compliant robot motion. Applied Sciences,
9(24):1–18.
Compact, Accurate and Low-cost Hand Tracking System based on LEAP Motion Controllers and Raspberry Pi
659