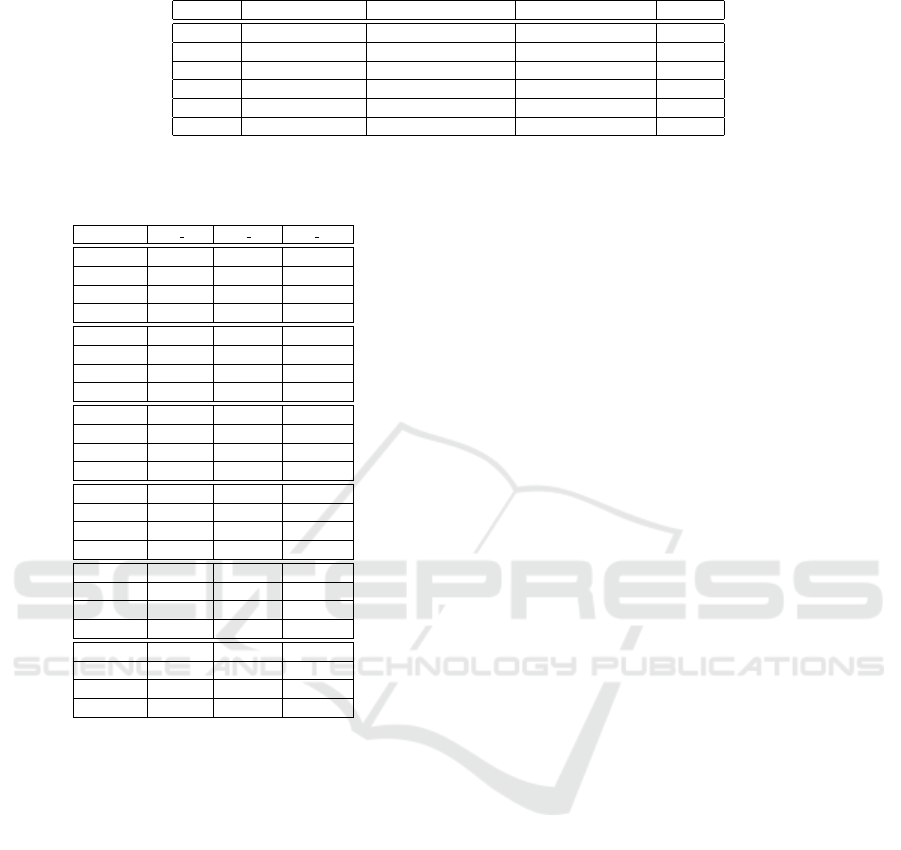
Table 2: Tests identification and parameters - Experiment 2; Alg stands for the corresponding algorithm initials.
ID Algorithms Disruption Type Dis Param Value
Alg-IT HC, SA, TS, LNS Inspection Time Disruption Strength 5
Alg-TT HC, SA, TS, LNS Travel Time Disruption Strength 5
Alg-VB HC, SA, TS, LNS Vehicle Breakdown No. Vehicles 1
Alg-UC HC, SA, TS, LNS Utility Changes Econ. Operator class III,V,VI
Alg-IB HC, SA, TS, LNS Inspection Breakdown No. Inspections 1
Alg-EI HC, SA, TS, LNS Emerging inspections No. Inspections 2
Table 3: Disruption management results. UF: utility func-
tion, UA: sum of economic operator utilities, Sim: solution
similarity.
ID avg UF avg UA avg Sim
HC-IT 13.09 11.55 0.22
SA-IT 12.88 12.88 0.00
TS-IT 13.51 11.15 0.34
LNS-IT 14.27 12.62 0.24
HC-TT 12.93 11.48 0.21
SA-TT 12.98 12.98 0.00
TS-TT 12.99 10.66 0.33
LNS-TT 13.04 10.80 0.31
HC-VB 10.74 9.67 0.20
SA-VB 10.76 10.76 0.00
TS-VB 10.72 9.30 0.270
LNS-VB 10.64 9.96 0.21
HC-UC 10.47 9.88 0.11
SA-UC 10.90 10.90 0.00
TS-UC 10.80 9.69 0.21
LNS-UC 10.70 9.47 0.23
HC-IB 13.57 11.75 0.26
SA-IB 12.89 12.89 0.00
TS-IB 13.77 11.58 0.31
LNS-IB 13.56 11.10 0.35
HC-EI -44.00 204.67 0.69
SA-EI 212.94 212.43 0.07
TS-EI 212.98 210.60 0.34
LNS-EI 211.99 209.37 0.37
REFERENCES
Atiqullah, M. M. (2004). An efficient simple cooling sched-
ule for simulated annealing. Lecture Notes in Com-
puter Science (including subseries Lecture Notes in
Artificial Intelligence and Lecture Notes in Bioinfor-
matics), 3045:396–404.
Azi, N., Gendreau, M., and Potvin, J.-Y. (2014). An adap-
tive large neighborhood search for a vehicle routing
problem with multiple routes. Computers I& Opera-
tions Research, 41:167–173.
Barros, T., Oliveira, A., Cardoso, H. L., Reis, L. P.,
Caldeira, C., and Machado, J. P. (2021). Economic
and food safety: Optimized inspection routes genera-
tion. In Rocha, A. P., Steels, L., and van den Herik, J.,
editors, Agents and Artificial Intelligence, pages 482–
503, Cham. Springer International Publishing.
Barros, T., Santos, T., Oliveira, A., Cardoso, H. L., Reis,
L. P., Caldeira, C., and Machado, J. P. (2020). In-
teractive inspection routes application for economic
and food safety. In Rocha,
´
A., Adeli, H., Reis, L. P.,
Costanzo, S., Orovic, I., and Moreira, F., editors,
Trends and Innovations in Information Systems and
Technologies, pages 640–649, Cham. Springer Inter-
national Publishing.
Cordeau, J.-F. and Laporte, G. (2005). Tabu search heuris-
tics for the vehicle routing problem. In Sharda, R.,
Voß, S., Rego, C., and Alidaee, B., editors, Meta-
heuristic Optimization via Memory and Evolution:
Tabu Search and Scatter Search, pages 145–163.
Springer US, Boston, MA.
Dantzig, G. B. and Ramser, J. H. (1959). The Truck Dis-
patching Problem. Management Science, 6(1):80–91.
Eglese, R. and Zambirinis, S. (2018). Disruption manage-
ment in vehicle routing and scheduling for road freight
transport: a review. Top, 26(1):1–17.
Genders, W. and Razavi, S. N. (2016). Impact of Connected
Vehicle on Work Zone Network Safety through Dy-
namic Route Guidance. Journal of Computing in Civil
Engineering, 30(2):04015020.
Gendreau, M., Guertin, F., Potvin, J.-Y., and Taillard, E.
(1999). Parallel tabu search for real-time vehicle rout-
ing and dispatching. Transportation Science, 33:381–
390.
Hahsler, M. and Hornik, K. (2007). TSP - Infrastructure for
the traveling salesperson problem. Journal of Statisti-
cal Software, 23(2):1–21.
Liu, J. L. and Lin, J. H. (2007). Evolutionary computa-
tion of unconstrained and constrained problems using
a novel momentum-type particle swarm optimization.
Engineering Optimization, 39(3):287–305.
Pillac, V., Gendreau, M., Gu
´
eret, C., and Medaglia, A. L.
(2013). A review of dynamic vehicle routing prob-
lems. European Journal of Operational Research,
225(1):1–11.
Psaraftis, H. N., Wen, M., and Kontovas, C. A. (2016). Dy-
namic vehicle routing problems: Three decades and
counting. Networks, 67(1):3–31.
Ritzinger, U., Puchinger, J., and Hartl, R. F. (2016). A sur-
vey on dynamic and stochastic vehicle routing prob-
lems. International Journal of Production Research,
54(1):215–231.
Shaw, P. (1998). Using constraint programming and local
search methods to solve vehicle routing problems. In
Maher, M. and Puget, J.-F., editors, Principles and
Practice of Constraint Programming — CP98, pages
417–431. Springer Berlin Heidelberg.
Wilson, N. and Colvin, N. (1977). Computer Control of the
Rochester Dial-A-Ride System. CTS report. MIT.
Disruption Management of ASAE’s Inspection Routes
817