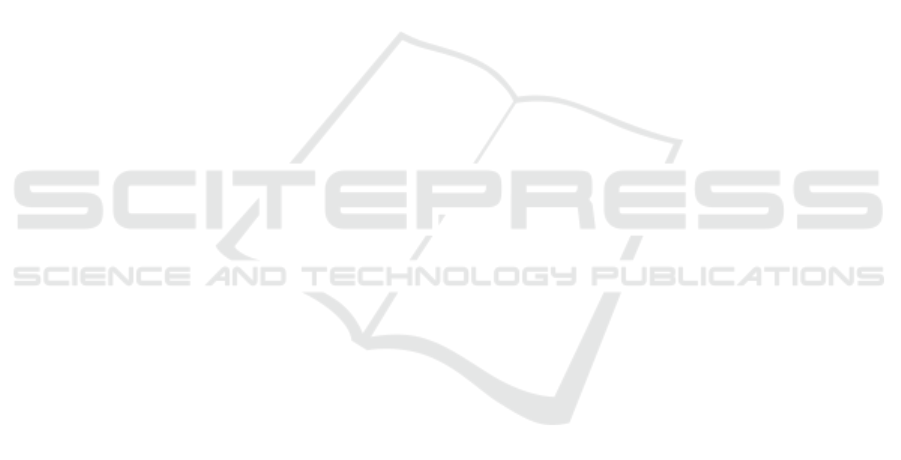
by smartly integrating the state of the art and sci-
ence. Research that focuses exclusively on restricted
areas such as depots could lead into a wrong direction.
Thus, this paper addresses two key aspects to prevent
this and to make research economically viable from
the very beginning. First the automation potential and
the saving potential has to be analyzed through sci-
entific methods and subsequent analyses. In addition,
the suitability of the transfer for operation on duty has
to be considered. The insight of this paper is, that it is
crucial to consider not only a single scenario or envi-
ronment, such as the depot, but to ensure a future op-
eration on duty, enabled with the chosen solution of
automation. Furthermore, the information gathered
on duty can be used for further optimization of the
processes at the depot, using new insights. Follow-
ing this approach, a first important step towards full
automation of public transport vehicles can be made
today in order to be better prepared for future opera-
tion and to ensure a faster market introduction and a
higher acceptance and safety of the vehicles.
ACKNOWLEDGEMENTS
Part of this work has been funded by German Federal
Ministry of Transport and Digital Infrastructure in the
project AStriD (funding no. 19F2104F).
REFERENCES
Altenburg, S., Kienzler, H.-P., and Auf der Maur, A. (2018).
Einf
¨
uhrung von Automatisierungsfunktionen in der
Pkw-Flotte. Prognos AG, 58.
Brenner, N., Lauber, A., Eckert, C., and Sax, E. (2019). Au-
tonomous driving of commercial vehicles within cor-
doned off terminals. In VEHITS 2019 : proceedings
of the 5th International Conference on Vehicle Tech-
nology and Intelligent Transport Systems : Heraklion,
Crete, Greece, May 3-5, 2019. Ed.: Oleg Gusikhin,
pages 521–527. SciTePress.
Brenner, N., Lauber, A., Meier, C., Reitmeier, W., and Sax,
E. (2021). Requirements of Automated Vehicles and
Depots for the Initial Step of Automated Public Trans-
port, page 15–26. Proceedings. Springer Fachmedien
Wiesbaden.
Chalapathy, R. and Chawla, S. (2019). Deep learning
for anomaly detection: A survey. arXiv preprint
arXiv:1901.03407.
Daimler (2021). eCitaro.Safe driving.
Drescher, T., Rossel, N., and Sax, E. (2021). Bus-Platoon
im Stadtverkehr. Der Nahverkehr, page 5.
G
¨
ohlich, D., Fay, T.-A., Jefferies, D., Lauth, E., Kunith, A.,
and Zhang, X. (2018). Design of urban electric bus
systems. Design Science, 4.
Intelligent Transport (2021). RABus: the autonomous bus
trial underway in Baden-W
¨
urttemberg.
Kavathekar, P. and Chen, Y. (2012). Vehicle platooning:
A brief survey and categorization. In Proceedings of
the ASME International Design Engineering Techni-
cal Conferences and Computers and Information in
Engineering Conference - 2011, pages 829–845, New
York, NY. ASME.
Krampitz, M. (2020). Potentiale der Automatisierung im
¨
OPNV. Der Nahverkehr, page 3.
Lauber, A., Brenner, N., and Sax, E. (2019). Automated
vehicle depots as an initial step for an automated pub-
lic transportation. Poster pr
¨
asentiert auf UITP Global
Public Transport Summit (2019), Stockholm, Schwe-
den, 9.–12. Juni 2019.
Lauth, E., Mundt, P., and Gohlich, D. (2019). Simulation-
based planning of depots for electric bus fleets consid-
ering operations and charging management. In 2019
4th International Conference on Intelligent Trans-
portation Engineering (ICITE), pages 327–333. IEEE.
Mercedes-Benz (2014). Autonomous driving in the tracks
of bertha benz. In Mercedes-Benz next.
Ngai, E. W., Cheng, T. E., Au, S., and Lai, K.-h. (2007).
Mobile commerce integrated with rfid technology in a
container depot. Decision Support Systems, 43(1):62–
76.
Noda, M., Takahashi, T., Deguchi, D., Ide, I., Murase,
H., Kojima, Y., and Naito, T. (2011). Vehicle ego-
localization by matching in-vehicle camera images to
an aerial image. In Koch, R. and Huang, F., editors,
Computer Vision – ACCV 2010 Workshops, pages
163–173, Berlin, Heidelberg. Springer Berlin Heidel-
berg.
Randhahn, A. and Knote, T. (2020). Deployment of charg-
ing infrastructure for battery electric buses. In To-
wards User-Centric Transport in Europe 2, pages
169–183. Springer.
Robert Bosch GmbH (2021). On the road to realizing Vi-
sion Zero: smart sensors for commercial vehicles.
SAE (2019). Sae standards news: J3016 automated-driving
graphic update.
Stachowiak, H. (1973). Allgemeine Modelltheorie.
Springer.
Tirachini, A. and Antoniou, C. (2020). The economics of
automated public transport: Effects on operator cost,
travel time, fare and subsidy. Economics of Trans-
portation, 21:100151.
UITP (2019). World report on metro automation.
VDV, Blumenstengel, M., Herms, R., Kamender, S.,
K
¨
ahler, H., Kr
¨
amer, T., Sievers, M., and Schmitz, J.
(2016). VDV-Schrift 822 - Richtlinie f
¨
ur den Bau von
Omnibus-Betriebsh
¨
ofen.
Verkehrswesen, I. (2016). Urbane mobilit
¨
at morgen: Future
bus, urban etruck, vision van.
Volvo Buses (2021). Volvo Bus Rapid Transit.
Walzel, B., Sturm, C., Fabian, J., and Hirz, M. (2016). Au-
tomated robot-based charging system for electric ve-
hicles. In 16. Internationales Stuttgarter Symposium,
pages 937–949. Springer.
Zekavat, R. and Buehrer, R. M. (2012). Fundamentals
of Time-of-Arrival-Based Position Locations, pages
175–212.
Automation Potentials in Public Transport based on a Depot Model
225