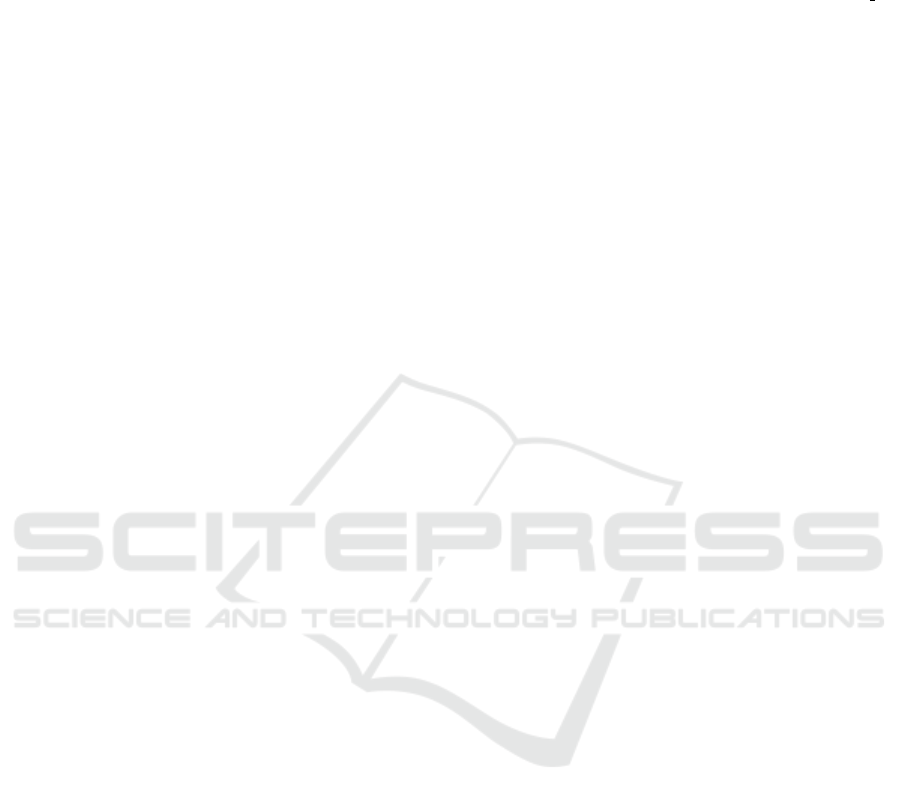
let. https://insideevs.com/reviews/395747/2020-mini-
cooper-se-first-drive-report/.
Motors, T., Berdichevsky, G., Kelty, K., Straubel, J., and
Toomre, E. (2007). The tesla roadster battery system.
tesla motors inc.
Munro (2020). Tearing down tesla segment 4: Battery
cooling system comparison on tesla model 3 vs.
bmw i3. https://leandesign.com/tearing-down-tesla-
segment-4-battery-cooling-system-comparison-on-
tesla-model-3-vs-bmw-i3/.
NIO (2021). Nio et7-ready for tomorrow-et7. https://
www.nio.com/et7.
Nisewanger (2018). Exclusive: details on hyundai’s
new battery thermal management design. https:
//electricrevs.com/2018/12/20/exclusive-details-on-
hyundais-new-battery-thermal-management-design/.
Nisewanger (2019). Lg sues sk, alleges stolen trade
secrets used to make kia niro and future vw batter-
ies. https://electricrevs.com/2019/04/30/lg-sues-sk-
alleges-stolen-trade-secrets-used-to-make-kia-niro-
and-future-vw-batteries/.
Pesaran, A. A. (2001). Battery thermal management in
ev and hevs: issues and solutions. Battery Man,
43(5):34–49.
R. Maughan (2021). What is the best electric vehicle battery
cooling system? https://avidtp.com/what-is-the-best-
cooling-system-for-electric-vehicle-battery-packs/.
Reddy, T. B. (2011). Linden’s handbook of batteries.
McGraw-Hill Education.
Roth, E. P., Crafts, C. C., Doughty, D. H., and McBreen, J.
(2004). Advanced technology development program
for lithium-ion batteries: thermal abuse performance
of 18650 li-ion cells. Sandia Nat. Lab., Albuquerque,
NM, USA, Rep. SAND2004-0584.
Schoewel, F. and Hochgeiger, E. (2014). The high-voltage
batteries of the bmw i3 and bmw i8. In Proceed-
ings of the Advanced Automotive Battery Conference
(AABC), Atlanta, GA, USA, volume 45.
Schwarz, W., Gschrey, B., Leisewitz, A., Herold, A., Gores,
S., Papst, I., Usinger, J., Oppelt, D., Croiset, I., Peder-
sen, P. H., et al. (2011). Preparatory study for a review
of regulation (ec) no 842/2006 on certain fluorinated
greenhouse gases. Final report, Sept.
Scrosati, B., Garche, J., and Tillmetz, W. (2015). Advances
in battery technologies for electric vehicles. Wood-
head Publishing.
Slowik, P., Hall, D., Lutsey, N., Nicholas, M., and Wappel-
horst, S. (2019). Funding the transition to all zero-
emission vehicles. White Paper.
Smith, J., Hinterberger, M., Hable, P., and Koehler, J.
(2014). Simulative method for determining the op-
timal operating conditions for a cooling plate for
lithium-ion battery cell modules. Journal of Power
Sources, 267:784–792.
Solyali, D. and Akinlabi, A. (2020). Configuration, de-
sign, and optimization of air-cooled battery ther-
mal management system for electric vehicles: A re-
view. Renewable and Sustainable Energy Reviews,
125(109815).
Sund
´
en, B. (2019). Hydrogen, Batteries and Fuel Cells.
Academic Press.
Tennessen, P. T., Weintraub, J. C., and Hermann, W. A.
(2014). Extruded and ribbed thermal interface for use
with a battery cooling system. US Patent 8,758,924.
Tesla (2021a). Model 3. https://www.tesla.com/en gb/
model3?redirect=no.
Tesla (2021b). Model s plain. https://ev-database.uk/car/
1405/Tesla-Model-S-Plaid.
Thakur, A. K., Prabakaran, R., Elkadeem, M., Sharshir,
S. W., Arıcı, M., Wang, C., Zhao, W., Hwang, J.-Y.,
and Saidur, R. (2020). A state of art review and future
viewpoint on advance cooling techniques for lithium–
ion battery system of electric vehicles. Journal of En-
ergy Storage, 32:101771.
Tomaszewska, A., Chu, Z., Feng, X., O’Kane, S., Liu, X.,
Chen, J., Ji, C., Endler, E., Li, R., Liu, L., et al. (2019).
Lithium-ion battery fast charging: A review. ETrans-
portation, 1:100011.
Volkswagen (2020). Battery and charging options.
https://www.volkswagen-newsroom.com/en/the-
new-id3-6240/battery-and-charging-options-6247.
Wallbox (2021). How do evs compare to gas cars?
https://blog.wallbox.com/how-do-evs-compare-to-
gas-cars/.
Wang, C., Lin, T., Huang, J., and Rao, Z. (2015a). Tempera-
ture response of a high power lithium-ion battery sub-
jected to high current discharge. Materials Research
Innovations, 19(sup2):S2–156.
Wang, Q., Jiang, B., Xue, Q. F., Sun, H. L., Li, B., Zou,
H. M., and Yan, Y. Y. (2015b). Experimental investi-
gation on ev battery cooling and heating by heat pipes.
Applied Thermal Engineering, pages 54–60.
Wu, W., Wang, S., Wu, W., Chen, K., Hong, S., and Lai,
Y. (2019). A critical review of battery thermal perfor-
mance and liquid based battery thermal management.
Energy conversion and management, 182:262–281.
Xie, J., Ge, Z., Zang, M., and Wang, S. (2017). Structural
optimization of lithium-ion battery pack with forced
air cooling system. Applied Thermal Engineering,
126.
Xu, M., Zhang, Z., Wang, X., Jia, L., and Yang, L. (2015).
A pseudo three-dimensional electrochemical–thermal
model of a prismatic lifepo4 battery during discharge
process. Energy, 80:303–317.
Yang, N., Zhang, X., Li, G., and Hua, D. (2015). Assess-
ment of the forced air-cooling performance for cylin-
drical lithium-ion battery packs: A comparative anal-
ysis between aligned and staggered cell arrangements.
Applied Thermal Engineering, 80:55–65.
Zhang, T., Gao, Q., Wang, G., Gu, Y., Wang, Y., Bao, W.,
and Zhang, D. (2017). Investigation on the promo-
tion of temperature uniformity for the designed bat-
tery pack with liquid flow in cooling process. Applied
Thermal Engineering, 116(Complete):655–662.
Zolot, M., Pesaran, A. A., and Mihalic, M. (2002). Ther-
mal evaluation of toyota prius battery pack. Technical
report, SAE Technical paper.
Zolot, M. D., Kelly, K., Keyser, M., Mihalic, M., Pesaran,
A., and Hieronymus, A. (2001). Thermal evaluation
of the honda insight battery pack. Technical report,
National Renewable Energy Lab., Golden, CO (US).
VEHITS 2022 - 8th International Conference on Vehicle Technology and Intelligent Transport Systems
68