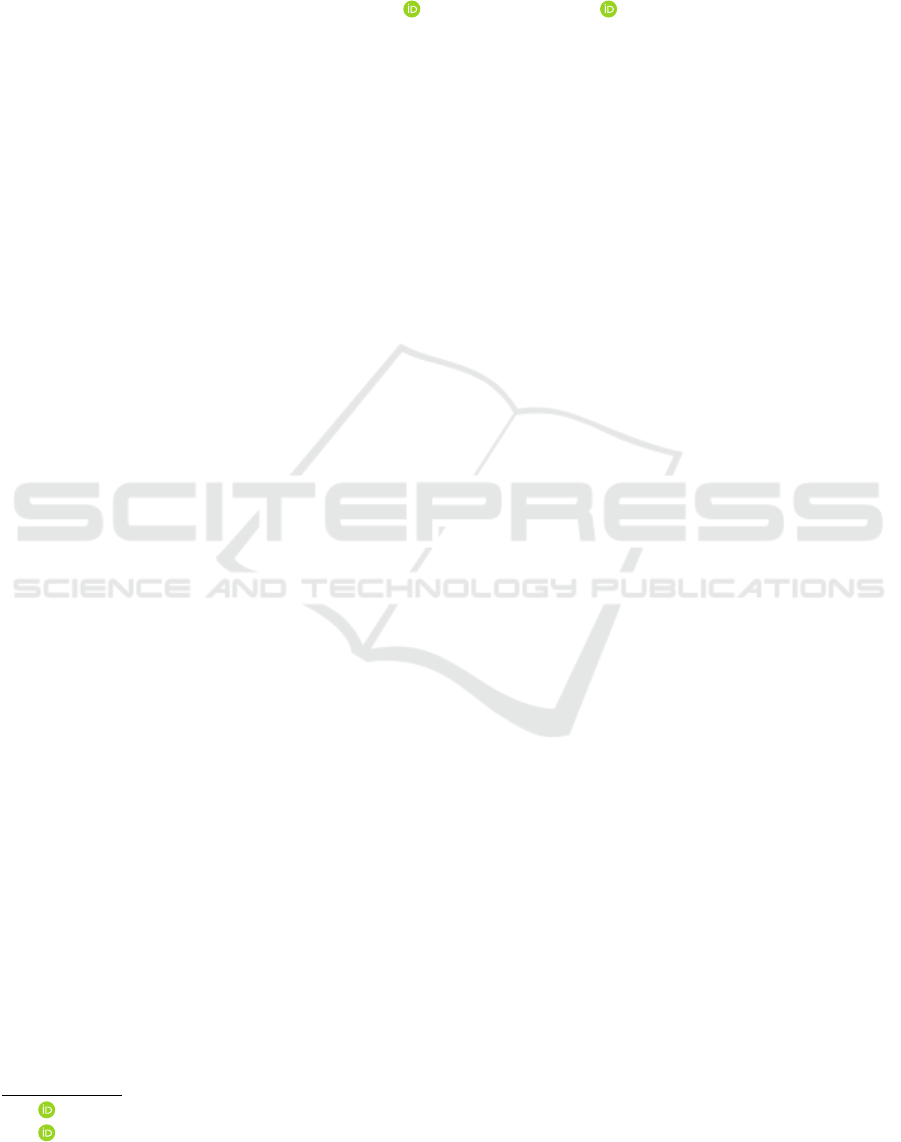
A Single Motor Driving and Steering Mechanism for a Transformable
Bicycle
Kazuki Sekine
a
and Ikuo Mizuuchi
b
Tokyo University of Agriculture and Technology, 2-24-16 Naka-cho, Koganei-shi, Tokyo 184-8588, Japan
Keywords:
Single Motor, Driving and Steering Mechanism, Self-driving Bicycle, Transforming Mechanism.
Abstract:
This research aims to propose a bicycle capable of transforming into a stable form suitable for autonomous
driving, and achieving both driving and steering with a single motor, using differential drive method. A novel
mechanism of one-motor differential drive using bevel gears and one-way clutches was devised. Then, a
prototype without transforming mechanism was fabricated. An experiment was conducted to demonstrate that
differential drive with a singke motor is possible. In the experiment, the prototype was capable of running
in straight lines and curves with small meandering. Next, to formulate the deceleration of the non-drive side
wheel in the proposed drive mechanism, another series of experiments was conducted. The equation for the
change in wheel rotating speed derived from the results enables accurate estimation of the future position of
the prototype, allowing it to run autonomously in further research.
1 INTRODUCTION
This research aims to transform a bicycle into a stable
form suitable for autonomous driving and to combine
driving and steering with a single motor.
Shared-cycle services are convenient because bi-
cycles can be easily rented, but they require the bi-
cycles to be returned after use. However, the collec-
tion of abandoned bicycles and the redistribution and
rearrangement of excess bicycles at specific return
ports are performed by trucks and other human op-
erators, which reduces the profitability of the shared-
cycle business. Therefore, we consider installing an
autonomous driving function in bicycles to automati-
cally return and relocate bicycles.
In existing research examples of autonomous bi-
cycles, such as Yeh et al.(Ting-Jen Yeh and Tseng.,
2019), two or more motors are used for driving and
steering, which makes the mechanism complex and
causes many failure factors. This makes them un-
suitable for use as shared bicycles, which are used
in large numbers and for long periods. In addition,
autonomous driving in the form of a bicycle requires
some kind of stabilizing mechanisms such as gyro-
scopic mechanism or large landing gears. Even with
those mechanism, there is always a risk of falling.
Also, those mechanisms only make the bicycle heav-
ier and become an obstacle when it is pedaled by a hu-
a
https://orcid.org/0000-0003-3727-8690
b
https://orcid.org/0000-0003-4657-2613
man. So, transforming the bicycle into a stable form
and drive autonomously with a single motor is an ef-
fective way. Naloa et al. (S
´
anchez et al., 2020) de-
veloped an autonomous bicycle with two rear wheels
with variable tread. When the bicycle is driven by hu-
man power, the rear wheels are attached to enable the
bicycle to tilt and turn. When it drives autonomously,
the tread is widened to stabilize. However, the vari-
able tread mechanism requires multiple actuators and
complex mechanisms to deploy, making it impracti-
cal.
Robots driven and steered by a single motor al-
ready exist. Ito et al. (Ito et al., 2019) developed a
single motor robot with passive wheels and propelled
by yaw moment generated by rotating weights. How-
ever, passive wheels limit the ability of robots such as
overcoming steps. So, application to a bicycle is dif-
ficult. Peidr
´
o et al. (Peidr
´
o et al., 2019) developed a
robot with two magnetic or pneumatic adhesion pads
at the bottom of each of the two ends. It can pivot
about different axes by alternately releasing or attach-
ing these pads to the floor. Howver, magnetic adhen-
sion is possible only on a ferromagnetic medium, and
pneumatic adhension needs a vacuum pump, which
requires additional energy. Ribas et al. (Ribas et al.,
2007) developed a three-wheeled robot that only front
wheel is connected to motor. The front wheel is pas-
sively steered by the direction of its rotation. How-
ever, the front wheel always faces almost sideways to
the body, which interferes with the straight-line mo-
tion of the robot. Toyoizumi et al. (Toyoizumi et al.,
Sekine, K. and Mizuuchi, I.
A Single Motor Driving and Steering Mechanism for a Transformable Bicycle.
DOI: 10.5220/0011349200003271
In Proceedings of the 19th International Conference on Informatics in Control, Automation and Robotics (ICINCO 2022), pages 531-538
ISBN: 978-989-758-585-2; ISSN: 2184-2809
Copyright
c
2022 by SCITEPRESS – Science and Technology Publications, Lda. All rights reserved
531