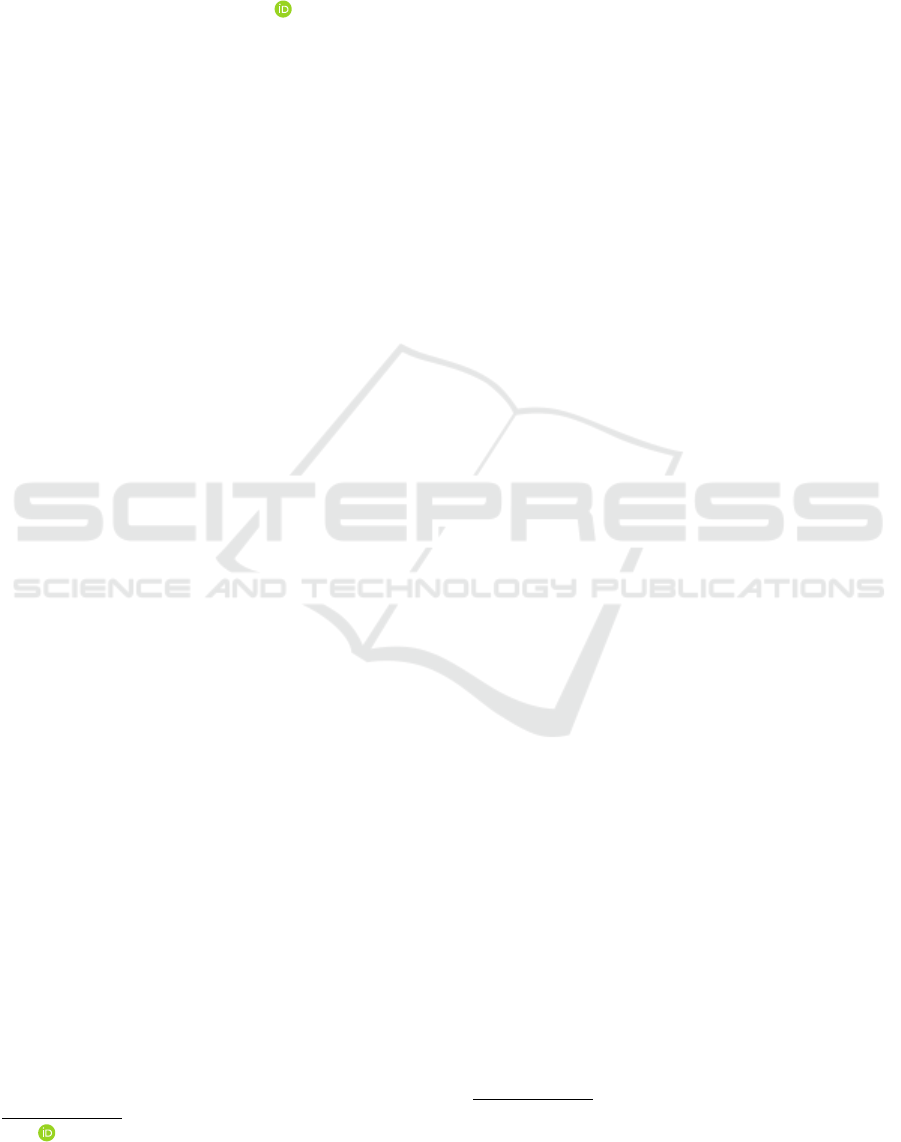
On-demand Electric Thrust Assistance for Muscle-powered Watercraft:
PADDELEC
Ren
´
e Budich
a
, Stephan Zipser, Jakob Doblaski and Jonas Seidel
Institute for Electric Mobility, University of Applied Sciences Dresden, Friedrich-List-Platz 1, Dresden, Germany
Keywords:
Paddelec, Demand-oriented Support, Electric Mobility, BEV, Canoe, SUP, Watercraft, Boat Simulation.
Abstract:
In the project PADDELEC, the implementation of an intelligent paddle (iPaddle) for controlling an electric
assisted canoe was realized. This paddle is able to record the paddle force F
B
of the blade with the help of
measurement technology integrated in the paddle shaft. The recording of the paddle stroke is used as a control
variable for operating an electric auxiliary drive in the boat. This is intended to provide on-demand thrust
assistance to the athlete, analogous to an electrified bicycle (pedelec). Existing drive solutions on motorized
boats offer the athlete the option of firmly specifying the desired thrust via a thrust lever or tiller. The paddelec
has the aim to provide intelligent and dynamic thrust assistance to the athlete as needed. This is intended to
preserve a natural driving feel, despite the auxiliary drive. A simulation model of the longitudinal dynamics
of canoes, was developed to investigate various assistance strategies. The models were validated by extensive
real driving tests. For this purpose, special hardware and software tools had to be created, which will be further
developed in the future. With the simulation and the evaluation of the practical testing, it could be shown that
thrust support for canoes can be very useful. The correct support strategy and support performance can vary
greatly depending on which water conditions the boat will use and the sporting activity, so there is still a need
for more research in this area.
1 INTRODUCTION
Water sports become more and more popular around
the world. For example, there has been a steady and
substantial increase in water touring by canoe (e.g. in
countries like Canada, Sweden and Germany). The
use of SUPs (Stand-Up-Boards) is also increasing for
some years now (BMWi, 2013).
In many cases water sports are performed at calm,
near-natural coastal, inland waters or low-current
rivers. However, it remains an outdoor sport where
wind and water current (and/or tide) often require a
powerful athlete.
To make this water sport available to a larger user
group, a battery-electric propulsion support is an ob-
vious suggestion. In case of bicycles, the idea of
battery-electric support is known as pedelec (pedal
electric cycle) and has been extraordinarily commer-
cially successful in Europe.
As known, real live disturbances like wind and
water current may affect the results of practical field
tests substantially. For this reason, physically oriented
models were developed to describe the response of a
a
https://orcid.org/0000-0002-9227-6834
boat to human and motor propulsion forces analyti-
cally. Model simulations in comparison to field tests
are also presented later.
The project was largely driven by engineering stu-
dents, who developed and implemented technical so-
lutions for measuring and controlling the boat-drives
and tested them in driving trials.
2 THE IDEA OF PADDELEC
The objective of the paddelec project is to develop a
system which provides on-demand electric thrust as-
sistance analogous to the established electric pedal as-
sistance for bicycles: the propulsion input of the user
is measured and supported electrically.
The basic principle of both technologies is identi-
cal.
1
In both cases, the mechanical input of the user
(or less technical the desire for assistance) is mea-
sured with a torque or force sensor. In the case of ca-
noeing, this is done with a paddle equipped with sen-
sors. The measurements are processed by a control
1
This is why the name analogy to the pedelec was de-
liberately chosen.
Budich, R., Zipser, S., Doblaski, J. and Seidel, J.
On-demand Electric Thrust Assistance for Muscle-powered Watercraft: PADDELEC.
DOI: 10.5220/0011380600003321
In Proceedings of the 10th International Conference on Sport Sciences Research and Technology Support (icSPORTS 2022), pages 17-28
ISBN: 978-989-758-610-1; ISSN: 2184-3201
Copyright
c
2022 by SCITEPRESS – Science and Technology Publications, Lda. All rights reserved
17