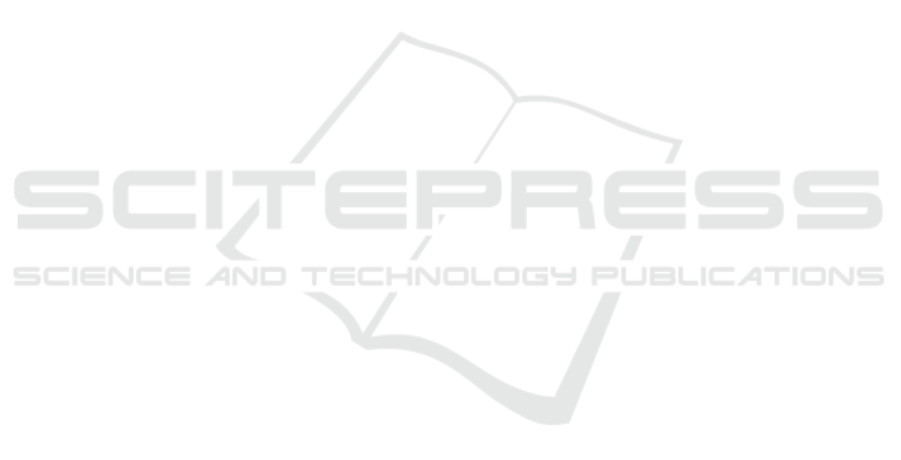
Gómez, D., & Diego, M. (2022, 7 20). Cognitive control of
Asphalt Drum [CAC1] - integrated.
doi:https://zenodo.org/record/6867477
Haber, R., Juanes, C., Del Toro, R., & Beruvides, G. (2015,
5). Artificial cognitive control with self-x capabilities:
A case study of a micro-manufacturing process.
Computers in Industry, 74, 135-150.
Jacoby, M., Jovicic, B., Stojanovic, L., & Stojanović, N.
(2021, 5). An Approach for Realizing Hybrid Digital
Twins Using Asset Administration Shells and Apache
StreamPipes. Information, 12(6), 217. Retrieved from
https://www.mdpi.com/2078-2489/12/6/217
Kaur, N., & Sood, S. (2015, 12). Cognitive decision making
in smart industry. Computers in Industry, 74, 151-161.
Koskinen, J. (1998). Fuzzy modelling of a pilot plant rotary
dryer. UKACC International Conference on Control
(CONTROL '98), 515-518.
Le Guen, L., Huchet, F., & Tamagny, P. (2011, 6). Drying
and Heating Modelling of Granular Flow : Application
to the Mix-Asphalt Processes. Journal of Applied Fluid
Mechanics, 4(2), pp 71-80. Retrieved from
https://hal.archives-ouvertes.fr/hal-00612503
Li, M.-L., Yao, Y.-Y., & Zhao, H.-X. (2017). Numerical
Analysis of Solid Materials Transport in a Rotary
Dryer. Proceedings of the 3rd Annual International
Conference on Mechanics and Mechanical Engineering
(MME 2016).
Ljung, L. (1998). System Identification. Retrieved from
http://link.springer.com/10.1007/978-1-4612-1768-
8_11
Mahmoud, K., El-Kasassy, M., & Areed, F. (2020, 11).
Variable Structure Controller for a Rotary Dryer
(Dept.E). MEJ. Mansoura Engineering Journal, 36(2),
13-21.
Measuring Coal Particles in the Pipe. (2022, 07 21).
Retrieved from https://www.power-eng.com/emissi
ons/measuring-coal-particles-in-the-pipe/
Oliveira, J., Van Der Geld, C., & Kuerten, J. (2017, 7).
Concentration and velocity statistics of inertial particles
in upward and downward pipe flow. Journal of Fluid
Mechanics, 822, 640-663.
Pang, S., Jia, J., Ding, X., Yu, S., & Liu, Y. (2021, 9).
Intelligent Control in the Application of a Rotary Dryer
for Reduction in the Over-Drying of Cut Tobacco.
Applied Sciences, 11(17), 8205.
Project Deliverables — Capri. (2022, 07 19). Retrieved from
https://www.capri-project.com/project-deliverables
Raghavan, V., Jumah, R., & Mujumdar, A. (2006, 11).
Control of Industrial Dryers. Handbook of Industrial
Drying, Third Edition.
Rožanec, J., Lu, J., Rupnik, J., Škrjanc, M., Mladenić, D.,
Fortuna, B., Kiritsis, D. (2021, 3). Actionable Cognitive
Twins for Decision Making in Manufacturing.
Retrieved from http://arxiv.org/abs/2103.12854
Rubio, F., Bordons, C., Holgado, J., & Rivas, I. (2001, 4).
Modelling and H∞ control of a rotary dryer. 2001
European Control Conference, ECC 2001, 33(4), 733-
738.
Salis, A., Marguglio, A., De Luca, G., Gusmeroli, S., &
Razzetti, S. (2022, 2). An Edge-Cloud based Reference
Architecture to support cognitive solutions in the
Process Industry.
Sánchez Boza, A., Guerra, R., & Gajate, A. (2011, 3).
Artificial cognitive control system based on the shared
circuits model of sociocognitive capacities. A first
approach. Engineering Applications of Artificial
Intelligence, 24(2), 209-219.
Schwenzer, M., Ay, M., Bergs, T., & Abel, D. (2021, 11).
Review on model predictive control: an engineering
perspective.
Sharma, A., Kosasih, E., Zhang, J., Brintrup, A., &
Calinescu, A. (2020, 11). Digital Twins: State of the Art
Theory and Practice, Challenges, and Open Research
Questions. Retrieved from http://arxiv.org/abs/
2011.02833
Singh, R., Lye, S., & Miao, J. (2019, 8). PVDF Nanofiber
Sensor for Vibration Measurement in a String. Sensors,
19(17), 3739. Retrieved from https://www.mdpi.com/
1424-8220/19/17/3739
Sivilevičius, H., & Šukevičius, Š. (2009, 6). Manufacturing
technologies and dynamics of hot-mix asphalt mixture
production.
Suppan, T., Neumayer, M., Bretterklieber, T., Puttinger, S.,
& Wegleiter, H. (2022, 1). A Model-Based Analysis of
Capacitive Flow Metering for Pneumatic Conveying
Systems: A Comparison between Calibration-Based
and Tomographic Approaches. Sensors, 22(3), 856.
Retrieved from https://www.mdpi.com/1424-
8220/22/3/856
Vega, C., & Reñones, A. (2022, 3 18). Cognitive sensor for
amount of filler. doi:https://doi.org/10.5281/zenodo.
6367575
Vega, C., Reñones, A., & Sanz, L. (2022, 7 28). Cognitive
sensor for amount of filler [CAS2] - INTEGRATED.
Retrieved from https://zenodo.org/record/6922993
Wagner, S., Milde, M., Barhebwa-Mushamuka, F., &
Reinhart, G. (2022). Digital Twin Design in Production.
Lecture Notes in Mechanical Engineering, 339-346.
Yliniemi, L., Koskinen, J., & Leiviskä, K. (1998, 9).
Advanced Control of a Rotary Dryer. IFAC
Proceedings Volumes, 31(23), 119-124.
Zaeh, M., Beetz, M., Shea, K., Reinhart, G., Bender, K.,
Lau, C., . . . Herle, S. (2008, 11). The Cognitive Factory.
Zhang, K., Huchet, F., & Hobbs, A. (2019, 5). A review of
thermal processes in the production and their influences
on performance of asphalt mixtures with reclaimed
asphalt pavement (RAP). Construction and Building
Materials, 206, 609-619.
ETCIIM 2022 - International Workshop on Emerging Trends and Case-Studies in Industry 4.0 and Intelligent Manufacturing
278