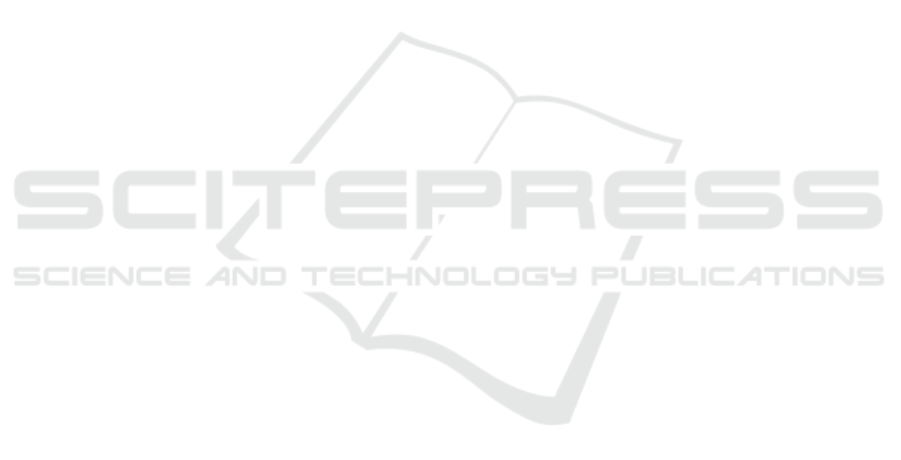
3.3.1 CI/CD Testing
As large parts of a CI/CD testing environment will
be carried out in a classical IT-environment, no chal-
lenges stem from this part. However, there is a gen-
eral challenge: the heterogeneity of hardware and
operating systems typical of Industry 4.0 can make
these tasks more complex than usual. Also, intelli-
gent methods require additional CI/CD tests. These
include tests for features and data, model develop-
ment, ML infrastructure, and monitoring tests for ML
serving, e.g., performance. A particular challenge is
that ML elements are typically analyzed on a statis-
tical basis, while traditional testing requires correct-
ness of each individual test case. Moreover, in au-
tomated adaptation scenarios even these tasks may
happen within the factory environment, making this
a rather complex task.
3.3.2 Model Deployment
MLOps activities can be performed on the factory
floor, in the cloud, or in corporate IT environments.
Specifically, in the case of the factory floor, edge re-
sources are needed, leading to the typical problems of
sufficient and appropriate resources to ensure neces-
sary technical performance requirements.
3.3.3 Monitoring
In Industry 4.0, monitoring physical processes is an
integral part. Ideally, the existing monitoring solu-
tion is suitable for MLOps or can be extended easily.
If this is not the case, e.g., if physical separation of
groups or networks is required, a specific challenge
arises. Additional hardware requirements or develop-
ment efforts become necessary.
3.4 Support Activities
Support Activities are cross-cutting activities related
to infrastructure, tools, versioning and automation.
Here, we address challenges refering to support ac-
tivities.
3.4.1 Infrastructure
A major general challenge related to the infrastruc-
ture is the heterogeneity, which is even larger than for
MLOps in information systems. Some parts need to
run in an embedded context, some in corporate IT-
environments. In the case that model engineering ac-
tivities are also automated to some extend, there may
even exist the case that for the same steps multiple dif-
ferent infrastructures are needed (IT vs. embedded).
If frameworks like TensorFlow are used for ma-
chine learning in the manual environment, they are
typically not available as implementations on the fac-
tory floor. Rather this requires special frameworks
available for edge computing that may not bring the
same features, e.g., TensorFlow-light. The higher the
level of automation and the requirements for the prop-
erties associated with MLOps become, the more dif-
ficult it is to deploy them in the environment of IoT
and edge devices.
Another general problem is the lack of widely and
homogeneously adopted standards; while there are
standards, many different standards are around and
applied in inhomogeneous fashion, partially also due
to (expensive) legacy machines or retrofitting of fac-
tory equipment.
This also leads to a lack of standardization of
tools, making tool selection in the context of Indus-
try 4.0 a major challenge.
The extent to which parts of the MLOps cycle
are automated varies significantly among cases. Of
course, several steps, like deployment or productive
operation are usually automated. However, so far our
observation is that while many companies envision a
high degree of automation, and even are interested in
full automation of model adaptation, so far none, we
are aware of, implemented this degree of automation
in production.
We envision for the future that some degree of
automated adaptation will become standard practice
also in Industry 4.0. Nevertheless, difficult ques-
tions about what may be changed independently in the
model and productive operation will remain. In par-
ticular, changes by self-adaptation may impact hard-
ware requirements and reliability.
MLOps emphasizes the management of inter-
dependencies among data, models, and code. Thus,
versioning this information is important. If these in-
formation should be available at edge nodes, e.g., as
feature stores, appropriate versioning infrastructure
must also be available there.
3.4.2 Tools
Here, we present a general challenge. Typically,
a more complex tool environment is required for
MLOps in Industry 4.0. This is due to the fact
that some steps will be done manually in an IT-
environment, but also corresponding tools in the em-
bedded environment are needed. Also tools that ad-
dress the specifics of the industry environment (e.g.,
cross-compilation) are required. Special tools like
simulation environments may also be needed in order
to study the impact of the ML solutions. In particular,
if they influence the factory behavior.
Is MLOps different in Industry 4.0? General and Specific Challenges
165