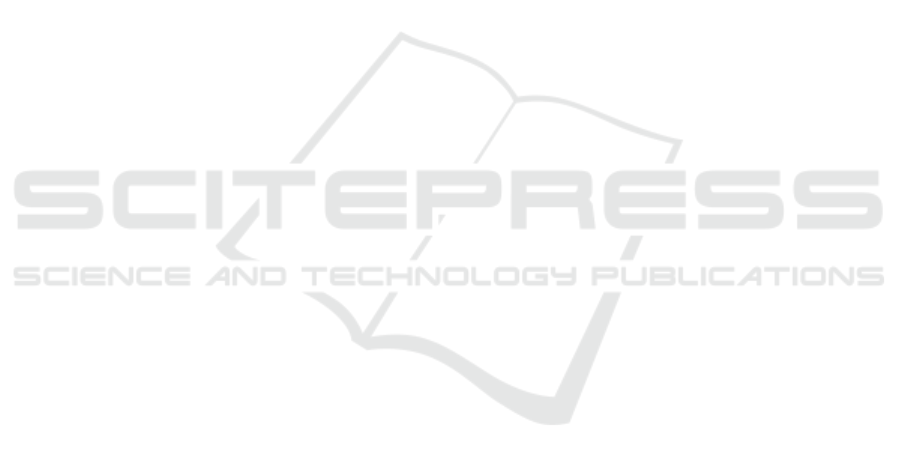
hands. This electro mechanism will move the robot's
hand to open and close then press the cover of the
strain clamp insulator, until it closes perfectly.
The concept of this research is to convert the
required mechanical compressive force at the end of
the pressure point into the required electric motor
power. Based on the power of the electric motor
needed, research on the needs of the motor driver and
microcontroller is needed.
The test of compressive force required the based
load point is carried out by giving the load at the
based load point gradually. The weight of the load at
the based load point in the time of the robot hand
closes the cover strain clamp completely, the weight
of the load is recorded and multiplied by the
acceleration / gravity of the earth as the required
compressive force. The performance test of the DC
motor and control on the robotic hand is done by
observed the voltage and current changes in the DC
motor every 4 seconds until the robotic hand closes
completely.
2.2 Total Sample
This research was conducted with 100% sample that
are 3 set of robotic hands, the collection was carried
out with a total of 30 data. To obtain these 30 data, it
was done by loading the water load repeatedly for 10
time for each sample until the cover strain clamp
closed completely. The total of the water weight plus
the container weight multiplied by the gravitational
force of the earth is recorded as the force required to
close the robotic hand.
Data on the test result of the performance of the
DC motor and control is done by observed voltage
and current in the DC motor every 4 seconds until the
robotic hand closes completely. So that for one
observation, 13 data were obtained for each sample
because the working time was 52 seconds, the total
data became 39 data for the three samples.
2.3 Variable Operational Definition
The focus of this study to observing the magnitude of
the indicators of this research, that are: force, voltage,
current, power and battery capacity. Voltage is
amount in volt of potential test voltage between two
terminal of motor DC. The current is amount in
ampere of electron flow from battery to the motor
DC. Power in watt or newton yang calculated to real
load on the base point of load. Battery capacity was
calculated to the battery insertion in to the robotic
hands.
2.4 Data Analysis
Data obtained from the test results and nameplate are
processed quantitatively. Data processed
mathematically and statistically by finding the data
variation on the step on each water filling. The data
are processed mathematically to obtain the voltage,
current and power at the initial of the test. The output
mathematically data is processed trough statistically
to obtain the average data, data sequence, which is
also displayed graphically.
3 FORCE, DC MOTOR, DRIVER
AND BATTERY
3.1 Force
Newton’s second law of motion points out the
magnitude of force when velocity of body move in
force is proportional to impressed force.
Mathematically, can be describe Force was change in
velocity. That issue is now second law of motion is
based on definition of equation of force is weigh
multiple with velocity for horizontal move, and with
earth gravitation for vertical move, that are as
describe on this formula in below (Sarma, 2017)
The formula above can be explained that the value
of the force (F) is determined by the mass value (M)
of the object multiplied by the acceleration (a). The
unit of force is measured in Newtons, the unit of mass
of an object is measured in Kg and the unit of
acceleration is measured in m/s
2
(Caldwell et al.,
2020)(Ariadi & Dinata, 2018).
3.2 DC Motor for Robotic
Direct Current Motor Trough electromagnetic
converts the direct current electrical energy to
mechanic energy(Qader, 2017). Electricity in a DC
motor is flowed into the field coil so as to produce
magnetic flux, electricity is also flowed through the
charcoal brush to the rotor coil, so that the rotor coil
produces a rotor field. The size of the mechanical
power produced by the electric motor is greatly
influenced by the size of the field coil and the rotor
coil, so that the larger the coil, the greater the current
that flows and so that the electrical power consumed
is greater, resulting in large mechanical
power(Iswanto et al., 2020).
The Design of DC Motor for Robotic Hand to Install Strain Clamp Cover on Live Line Voltage 20,000 Volt
233