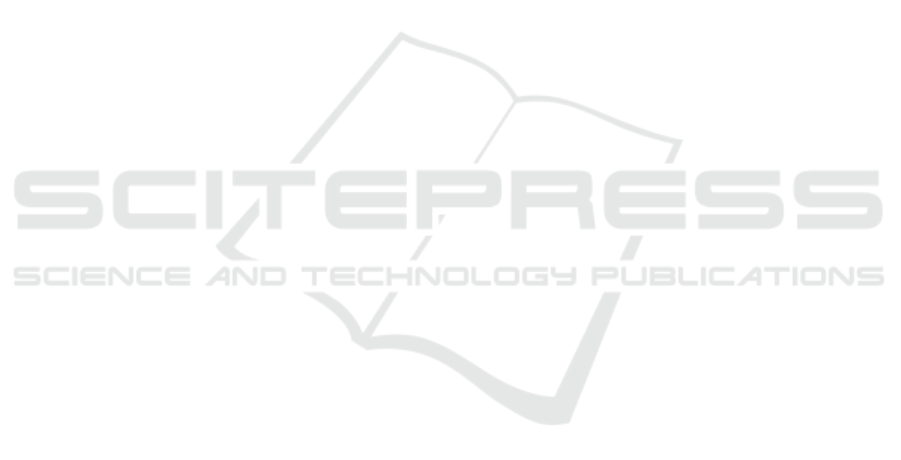
of Indonesia. estimated Part of anthracite and
bituminous coal is only 0.3% and 14.3% each while
most are classified as low-rank coal. Low-rank coal
can be added value by making it an adsorbent, where
the low-rank coal must be activated first. Activation
is a process to increase the absorption of adsorbents
by physical means, namely by high-temperature
treatment. A chemical process can be done by adding
a chemical substance (activator) that aims to build
porosity and enlarge surface area (Kirk-Othmer,
1983).
As raw material for the manufacture of activated
carbon, various basic materials that have hydrocarbon
bonds can be used, in this research the coal with the
lowest rank is used. Activated carbon uses coal from
East Kalimantan as raw material requires more
difficult activation compared to raw materials derived
from wood, husks, coconut shells, and others so a
carbonization technique is needed first and a
combination of chemical and physical activation.
Chemical activation involves impregnation of a given
precursor with activating agents such as phosphoric
acid (H3PO4), chloric acid (HCl), nitric acid
(HNO3), zinc chloride (ZnCl2), and alkali metal
compounds. Research with chemical activation of
bituminous coal in East Kalimantan used a
combination of H3PO4-NH4HCO3 activator solution
as discussed in the previous discussion, but in this
research, NH4CO3 will be substituted with NaHCO3
The application of the use of adsorbents is usually in
adsorption technology, which is a process or
phenomenon of accumulation of substances on the
surface of other substances, such events are usually
referred to as absorption of adsorbate molecules. to
the adsorbent surface. (Treybal, 1981)
Adsorbents are solid substances that can absorb
certain components of a fluid phase. In general,
adsorbents are very porous materials. Because the
pores are usually very small, they can be referred to
as nanoparticles with large surface areas. Many
adsorbents that can be used including low-cost ones,
including natural materials, bio-sorbents, and
industrial and agricultural waste materials can be used
because they have a high carbon content and low
inorganic content (Akil Ahmad et al., 2015). One of
the adsorbents is activated carbon which is
amorphous carbon that has a large surface area and
internal volume so that it has a high adsorption
capacity (Ali et al., 2012). It is amorphous carbon that
has a large surface area and internal volume so that it
has a high adsorption capacity. Activated carbon was
a material that has many very small pores (Liu et al.,
2019). These many pores will be able to make
activated carbon have the ability to adsorb various
other substances that are close to it. the wider the
surface of the activated carbon, in principle, the more
pores it has to increase the surface area, then several
materials containing activated carbon will be present
(Jawad et al., 2019; Lilibeth et al., 1996). There were
at least 2 ways that can be done for activation, the first
is a physical process, namely by using a high
temperature, and the second is through a chemical
process, namely using certain chemicals that can be
in the form of acids or bases, or even a combination
of both (Han et al., 2018; Yan et al., 2020).
Research conducted by Ghafarunnisa et. al
(2017), namely the manufacture of activated carbon
through the carbonization and activation stages
carried out at a temperature of 600
o
C for 3 hours.
Activation is carried out twice, namely chemical and
physical activation. Chemical activation using a
single reagent, namely a solution of H
3
PO
4
, and a
combination reagent, namely a solution of H
3
PO
4
-
NH
4
HCO
3
at a temperature of 600
o
C for 2 hours
showed the best-activated carbon activated by the
combination reagents H
3
PO
4
2M - NH
4
HCO
3
2M and
H
3
PO
4
2.5M - NH
4
HCO
3
2.5M. In general, activated
carbon does not meet the standards of SNI 06-3730-
1995. However, this study shows that the single
reagent H
3
PO
4
and the combination reagent H
3
PO
4
and NH
4
HCO
3
are good reagents for chemical
activation.
In this study, H
3
PO
4
-NaHCO
3
activator was used,
the use of this activator will produce H
2
CO
3
and
Na
3
PO
4
compounds where Na
3
PO
4
can reduce ash
because it can bind calcium magnesium and silica
(Saragih, 2009) while H
2
CO
3
can dissolve calcium
(Tahrini, et al, 2009). The results to be achieved from
this study are focused on the effect of carbonization,
chemical activation using H
3
PO
4
-NaHCO
3
, physical
activation, and Combination Chemical-Physical
activation on the quality of activated carbon in order
to increase the economic value of low-rank coal
which is abundant in East Kalimantan as an
alternative raw material for making activated carbon.
2 METHODOLOGY
First, the brown coal is reduced to -100+120 mesh,
then carbonized at T=600
0
C for 3 hours, then
chemical activation of the carbonized brown coal is
soaked using 2.5 M H
3
PO
4
solution - 2.5 M NaHCO
3
in 8 hours. The immersion results obtained were then
washed with distilled water until the pH was neutral
and then placed in an oven to remove the water
content at a temperature of 105
0
C and physical
activation was carried out by heating at T=800
0
C for
Characterization of Low Rank Coal as an Adsorbent Media through Physical-Chemical Activation Using H3PO4-NaHCO3 as an Activator
291