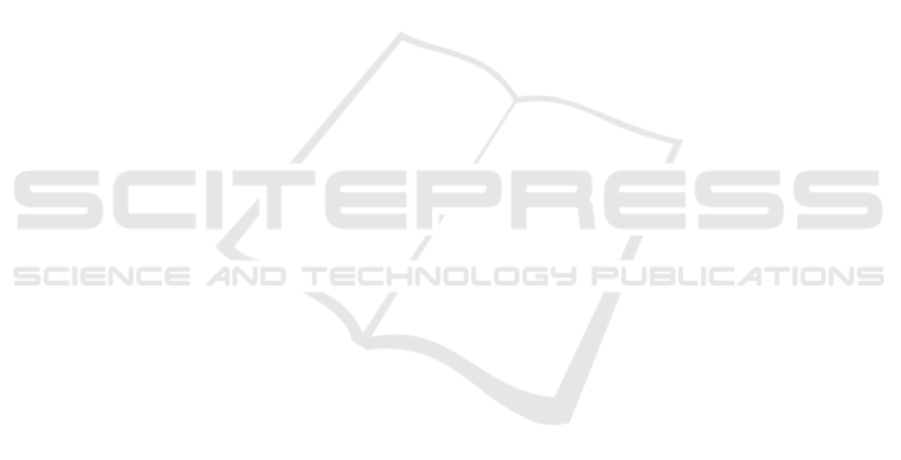
by country of destination and by country of origin.
Indonesia's charcoal exports reached 188,050 tons
with an export value of 145.09 million US dollars
(BPS, 2020). Due to the increasing demand for
Activated Charcoal., there is a strong need to sort out
the manufacturing technology for Activated Charcoal
preparation which must be cost-effective as well as on
par with commercially available Activated Charcoal.
Although various feedstocks have been explored for
the preparation of Activated Charcoal in previous
studies, scientists are still trying to explore new
materials depending on their availability and
suitability for Activated Charcoal production.
However, the utilization of Plantation waste as a raw
material for making activated charcoal has increased
rapidly in recent years. the use of making activated
charcoal by the partial oxidation method is still poorly
practiced.
Charcoal is a light carbon black residue produced
by heating wood (or other animal and plant materials)
with minimal oxygen to remove all water and other
volatile materials. In most cases, this pyrolysis
process, called charcoal burning, often results in the
formation of a charcoal furnace, where heat is
supplied by burning part of the starting material itself,
with a limited supply of oxygen. Materials can also
be heated in a closed medium. Activated charcoal has
the same initial process of making activated carbon.
Activated carbon (AC) is a non-graphite, non-
graphitizable carbon that has a very irregular
microstructure. It is famous for its high adsorption
capacity due to its high surface area and porosity.
Generally activated carbon can be made from various
raw materials including agricultural and forestry
residues. Generally most of the precursors used for
the manufacture of activated carbon are rich in carbon
(Prahas et al., 2008). AC production is achieved
usually through two methods, physical activation
method and chemical activation method (Bansal et
al., 1988)
Physical activation methods involve
carbonization of the feedstock followed by activation
at high temperatures (between 800 and 1100
o
C) in
the presence of an oxidizing gas such as carbon
dioxide or steam, while the chemical activation
method is mixing chemicals with precursors and then
followed by pyrolysis at moderate temperatures in the
absence of air High activated carbon uptake is closely
related to pore characteristics such as surface area,
pore volume, and pore size distribution. All activated
carbon has a porous structure, containing up to 15%
mineral matter in the form of ash content (Bansal et
al., 1988). The AC structure is formed during the
carbonization process and is continued during
activation, when the space between the forming
crystals is cleared of tar and other carbonated
materials. The structure of the hole and the size of the
hole are very dependent on the nature of the raw
material and the activation process. The activating
process removes the disorganized carbon by exposing
the crystallites to the action of the activating agent
leading to the construction of the diamond structure.
Activated carbon pore systems are of various types
and the individual pores may differ greatly in size and
shape. The drying, pyrolysis, and reduction processes
are heat-absorbing (endothermic), while the oxidation
process is heat-releasing (exothermic). On drying, the
moisture content of the solid fuel is evaporated by
heat absorbed from the oxidation process. In
pyrolysis, the separation of volatile matters (water
vapor, organic liquids, and non-condensed gases)
from charcoal or fuel carbon solids also uses heat
absorbed from the oxidation process. Combustion
oxidizes the carbon and hydrogen content of the fuel
by an exothermic reaction, whereas gasification
reduces the combustion product to gas by an
endothermic reaction. Further explanation regarding
these processes is given in the following description.
One of the important aspects of bioenergy to generate
heat, power and biofuels and products in the form of
activated charcoal for useful applications is biomass
gasification. As technology and materials advanced,
the development of gasification technology has
increased significantly for applications compared to
conventional power sources. This article presents an
overview of technical advances, developments in
biomass gasification technology and obstacles faced
by various stakeholders in the widespread
dissemination of technology for the needs of
individual communities and the business world to
support downstream to upstream activities (Shuit et
al., 2009).
2 METHODOLOGY
Palm oil shells from PT. Kebun Mandiri Sejahahtera
there are still impurities in the form of fibers and palm
seeds. Before carrying out the main process, it is
necessary to clean the shell by separating the
impurities. After it is considered clean, the drying
stage is carried out using sunlight. After that, five
kilograms of each process are weighed and then
stored and ready for use. The method used in this
research is to measure the results of the analysis of
activated charcoal based on SNI 06-3730-1995
standards with the main parameters of Moisture
content (%). The quality of activated charcoal greatly
iCAST-ES 2022 - International Conference on Applied Science and Technology on Engineering Science
424