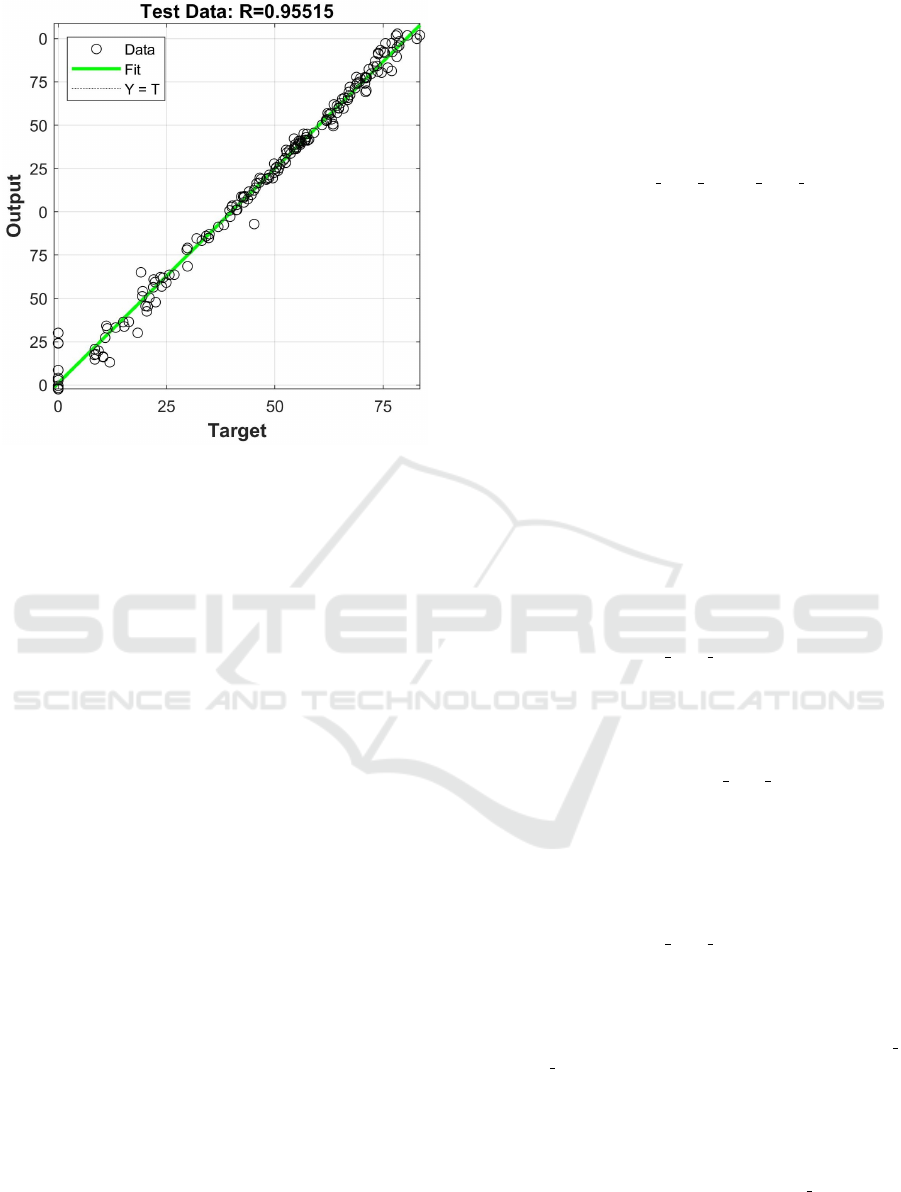
Figure 8: Modelling results.
4 CONCLUSIONS
To reduce negative impacts of vibrations occurring
in the drill string at deep drilling of hard rocks, a
mathematical model is proposed to consider param-
eters of the drilling process and predict the penetra-
tion rate. When studying the data on the drilling pro-
cess, the above parameters are used as input variables:
WOB, RPM, torque, MSE, longitudinal, transverse
and torsional vibrations. The resulting variable is the
ROP of the borehole. Considering the above param-
eters, a mathematical model of the drilling process is
formed on the basis of adaptive neural-fuzzy infer-
ence structures (ANFIS). The accuracy of the given
model makes 95.56 %.
REFERENCES
Aarsnes, U. J. F. and Aamo, O. M. (2016). Linear stabil-
ity analysis of self-excited vibrations in drilling using
an infinite dimensional model. Journal of Sound and
Vibration, 360:239–259. https://doi.org/10.1016/j.jsv.
2015.09.017.
Bogomolov, R. M. and Serikov, D. Y. (2018). Vibration
damper-calibrator. Equipment and Technologies for
Oil and Gas Complex, 3:39–43. https://doi.org/10.
30713/1999-6934-2018-3-39-43.
Cobern, M. E. (2003). Downhole vibration monitoring &
control system. Final report, APS Technology. https:
//doi.org/10.2172/831129.
Deng, P., Zhang, A., Fu, K., and Li, H. (2021). Nonlin-
ear Vibration of a Time-Space Coupled Drill String
System Based on the Surface Morphology of Rock.
Journal of Sound and Vibration, 506:116153. https:
//doi.org/10.1016/j.jsv.2021.116153.
Golik, V., Komashchenko, V., Morkun, V., and
Zaalishvili, V. (2015). Enhancement of
lost ore production efficiency by usage of
canopies. Metallurgical and Mining Indus-
try, 7(4):325–329. https://www.metaljournal.
com.ua/assets/MMI 2014 6/MMI 2015 4/
047-GolikKomashchenkoMorkunZaalishvili.pdf.
Liu, Y., Li, Q., Qi, Z., and Chen, W. (2021). Defect sup-
pression mechanism and experimental study on lon-
gitudinal torsional coupled rotary ultrasonic assisted
drilling of CFRPs. Journal of Manufacturing Pro-
cesses, 70:177–192. https://doi.org/10.1016/j.jmapro.
2021.08.042.
Moharrami, M. J., de Arruda Martins, C., and Shiri, H.
(2021). Nonlinear integrated dynamic analysis of
drill strings under stick-slip vibration. Applied Ocean
Research, 108:102521. https://doi.org/10.1016/j.apor.
2020.102521.
Morkun, V., Morkun, N., and Pikilnyak, A. (2014). Mod-
eling of ultrasonic waves propagation in inhomoge-
neous medium using fibered spaces method (k-space).
Metallurgical and Mining Industry, 6(2):43–48. https:
//www.metaljournal.com.ua/assets/Journal/a8.pdf.
Morkun, V., Morkun, N., and Tron, V. (2015a). Dis-
tributed control of ore beneficiation interrelated
processes under parametric uncertainty. Met-
allurgical and Mining Industry, 7(8):18–21.
https://www.metaljournal.com.ua/assets/Journal/
english-edition/MMI 2015 8/004Morkun.pdf.
Morkun, V., Morkun, N., and Tron, V. (2015b). Iden-
tification of control systems for ore-processing
industry aggregates based on nonparametric kernel
estimators. Metallurgical and Mining Industry,
7(1):14–17. https://www.metaljournal.com.ua/assets/
Journal/english-edition/MMI 2015 1/3%20Morkun,
%20Tron.pdf.
Morkun, V., Morkun, N., and Tron, V. (2015c).
Model synthesis of nonlinear nonstationary dy-
namical systems in concentrating production
using Volterra kernel transformation. Met-
allurgical and Mining Industry, 7(10):6–9.
https://www.metaljournal.com.ua/assets/Journal/
english-edition/MMI 2015 10/001Morkun.pdf.
Morkun, V. and Tron, V. (2014). Automation of
iron ore raw materials beneficiation with the op-
erational recognition of its varieties in process
streams. Metallurgical and Mining Industry, 6(6):4–
7. https://www.metaljournal.com.ua/assets/MMI
2014 6/1-MorkunTron.pdf.
Novikov, A. S. and Serikov, D. Y. (2020). Some features of
the work of drill bits and practical techniques for their
use [Nekotorye osobennosti raboty burovykh dolot i
prakticheskie priemy pri ikh ispolzovanii]. Sphere. Oil
and Gas, 2:44–49. https://xn--80aaigboe2bzaiqsf7i.
xn--p1ai/upload/journal/sphereoilandgas 2020-2.pdf.
Serikov, D. Y. and Ginzburg, E. S. (2015). Increasing the
efficiency of destruction of medium and hard rocks
Drill String Vibration Monitoring as an Element of Automatic Control of Drilling
61